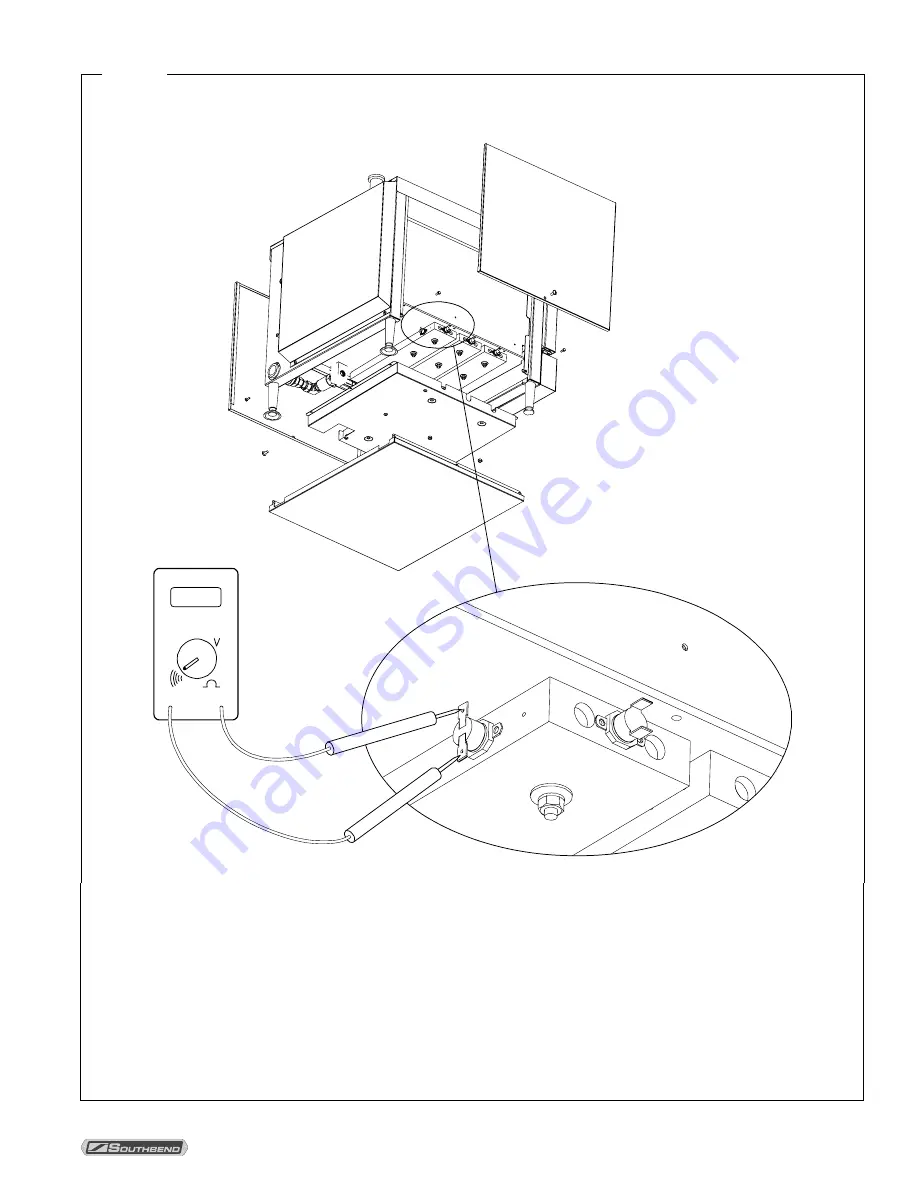
S
TRATO
S
TEAM
E
LECTRIC
C
OUNTERTOP
S
TEAMER
S
ERVICE
O
WNER
’
S
M
ANUAL
1189951
(10/08) P
AGE
31
OF
56
Figure 20
Water-Level-Control Sensor Check
Continuity
1.
DISCONNECT POWER AT CIRCUIT BREAKER
.
2. Remove the left and right side panels.
3. Remove bottom panel (four screws).
4. Remove insulation cover panel (four nuts).
5. Locate the water-level-control sensor (at the rear edge of the rear element block). Disconnect wires B1 and B2
from the sensor.
6. Place test leads across water-level-control sensor terminals (as shown above) and check for continuity when
the sensor is cool. If no continuity, replace sensor.
7. Reconnect wires and reassemble.
Summary of Contents for StratoSteam STRE-3D
Page 53: ...STRATOSTEAM ELECTRIC COUNTERTOP STEAMER OWNER S MANUAL 1189951 10 08 PAGE 53 OF 56 Notes...
Page 54: ...STRATOSTEAM ELECTRIC COUNTERTOP STEAMER PAGE 54 OF 56 OWNER S MANUAL 1189951 10 08 Notes...
Page 55: ...STRATOSTEAM ELECTRIC COUNTERTOP STEAMER OWNER S MANUAL 1189951 10 08 PAGE 55 OF 56 Notes...