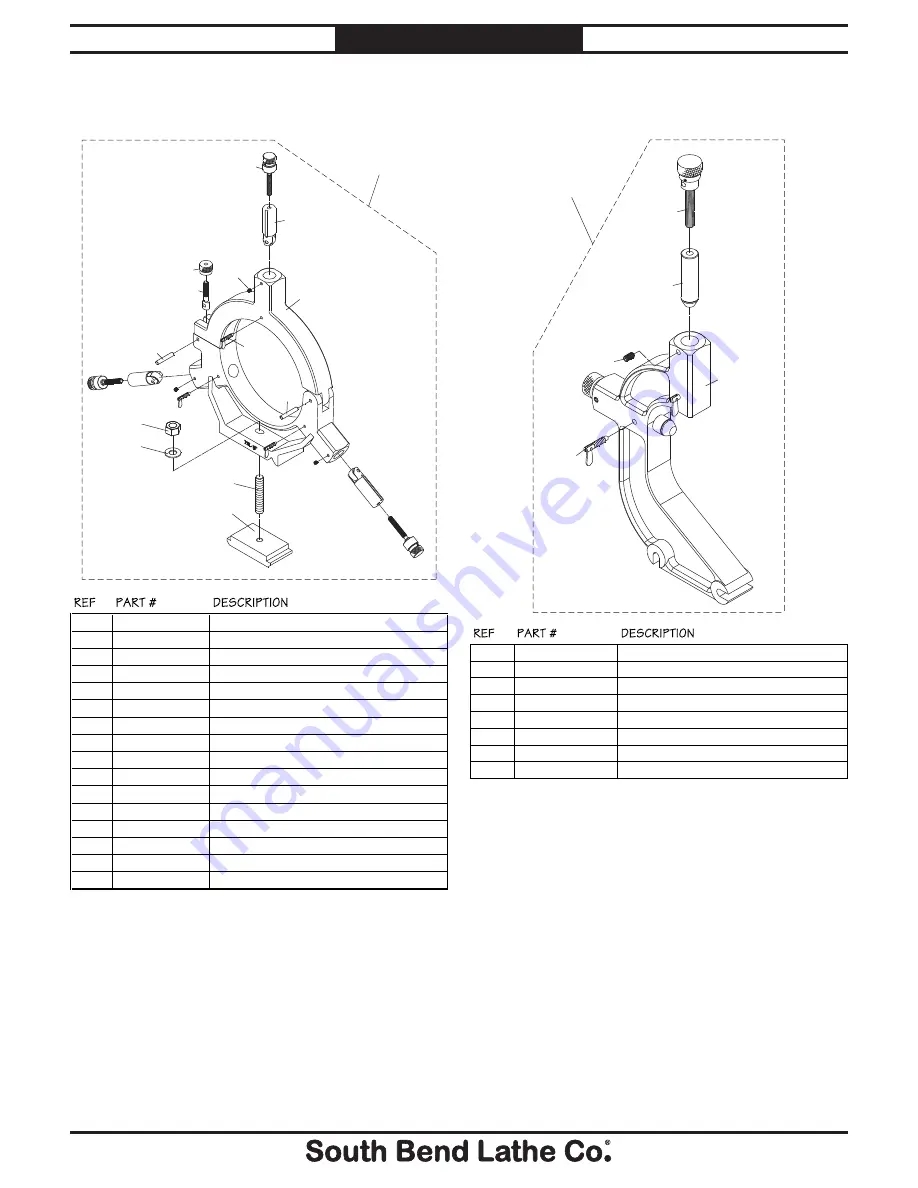
For Machines Mfg. Since 2/14
Turn-Nado
®
Gearhead Lathes
-131-
P A R T S
Steady Rest
Follow Rest
1701
1702
1703
1704
1705
1706
1700
1707
1708
1709
1710
1711
1712
1713
1801
1800
1802
1803
1804
1805
REF
PART #
DESCRIPTION
1700
PSB1046PF1700 STEADY REST ASSEMBLY (SB1046PF-48PF)
1700
PSB1056F1700
STEADY REST ASSEMBLY (SB1056F-58F)
1701
PSB1046PF1701
FINGER ADJUSTMENT KNOB ASSY
1702
PSB1046PF1702
FINGER ASSEMBLY
1703
PSS20M
SET SCREW M8-1.25 X 8
1704
PSB1046PF1704
CLAMP SCREW KNOB
1705
PSB1046PF1705
CLAMP SCREW
1706
PSB1046PF1706 CASTING 2PC (SB1046PF-48PF)
1706
PSB1056F1706
CASTING 2PC (SB1056F-58F)
1707
PSB1046PF1707
DOWEL PIN
1708
PSB1046PF1708 DOG PT LEAF SCREW M8-1.25 X 25
1709
PSB1046PF1709 HINGE PIN
1710
PSB1046PF1710
HEX NUT M18-2.25
1711
PLW12M
LOCK WASHER 18MM
1712
PSB1046PF1712
STUD-FT M18-2.25 X 75
1713
PSB1046PF1713
CLAMP PLATE
REF
PART #
DESCRIPTION
1800
PSB1046PF1800
FOLLOW REST ASSEMBLY (SB1046PF-48PF)
1800
PSB1056F1800
FOLLOW REST ASSEMBLY (SB1056F-58F)
1801
PSB1046PF1801
ADJUSTMENT KNOB ASSEMBLY
1802
PSB1046PF1802
FINGER ASSEMBLY
1803
PSS06M
SET SCREW M8-1.25 X 16
1804
PSB1046PF1804
FOLLOW REST CASTING (SB1046PF-48PF)
1804
PSB1056F1804
FOLLOW REST CASTING (SB1056F-58F)
1805
PSB1046PF1708
DOG PT LEAF SCREW M8-1.25 X 25
Summary of Contents for TURN-NADO SB1046PF
Page 138: ......
Page 140: ...Printed In U S A BLTS14126 ...