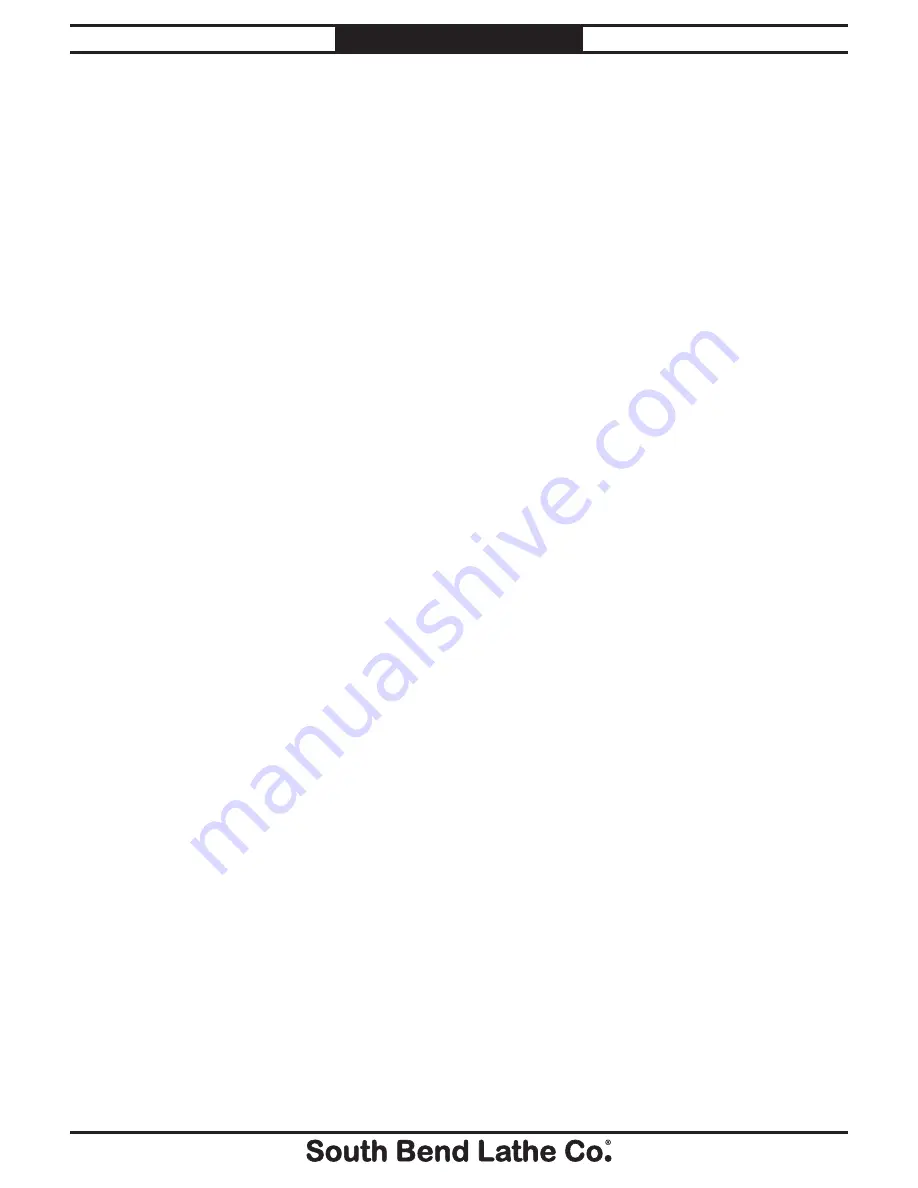
INTRODUCTION
-2-
For Machines Mfg. Since 8/09
Model SB1017
I N T R O D U C T I O N
About This Machine
Capabilities
This metal cutting bandsaw uses a gravity-fed
blade to make straight cuts through workpieces
that are clamped in a vise. Since the workpiece is
secured and remains stationary while the blade
feeds automatically, accuracy and operator safety
are maximized.
The vise on the Model SB1017 is capable of
holding rectangular stock up to 5" x 6" and round
stock up to 5".
After a cut is complete, the OFF switch is
triggered and the motor automatically turns off.
Features
In addition to its capabilities, the Model SB1017
has several features to increase versatility and
efficiency.
The vise can be rotated to perform angled cuts up
to 45° while three blade speeds ensure that the
proper cutting rate is available for a variety of
workpiece sizes and materials.
Both the downfeed rate and pressure are
adjustable for fine-tuning each cutting operation
and an adjustable auto-OFF power switch
maximizes safety and minimizes energy use by
turning the machine off at the end of every cut.
A storage compartment in the cabinet base
provides a convenient location for keeping spare
blades or other accessories and the transport
handle makes moving the machine easy.
Finally, the cast-aluminum knobs and belt cover
proudly bear the legendary South Bend name.