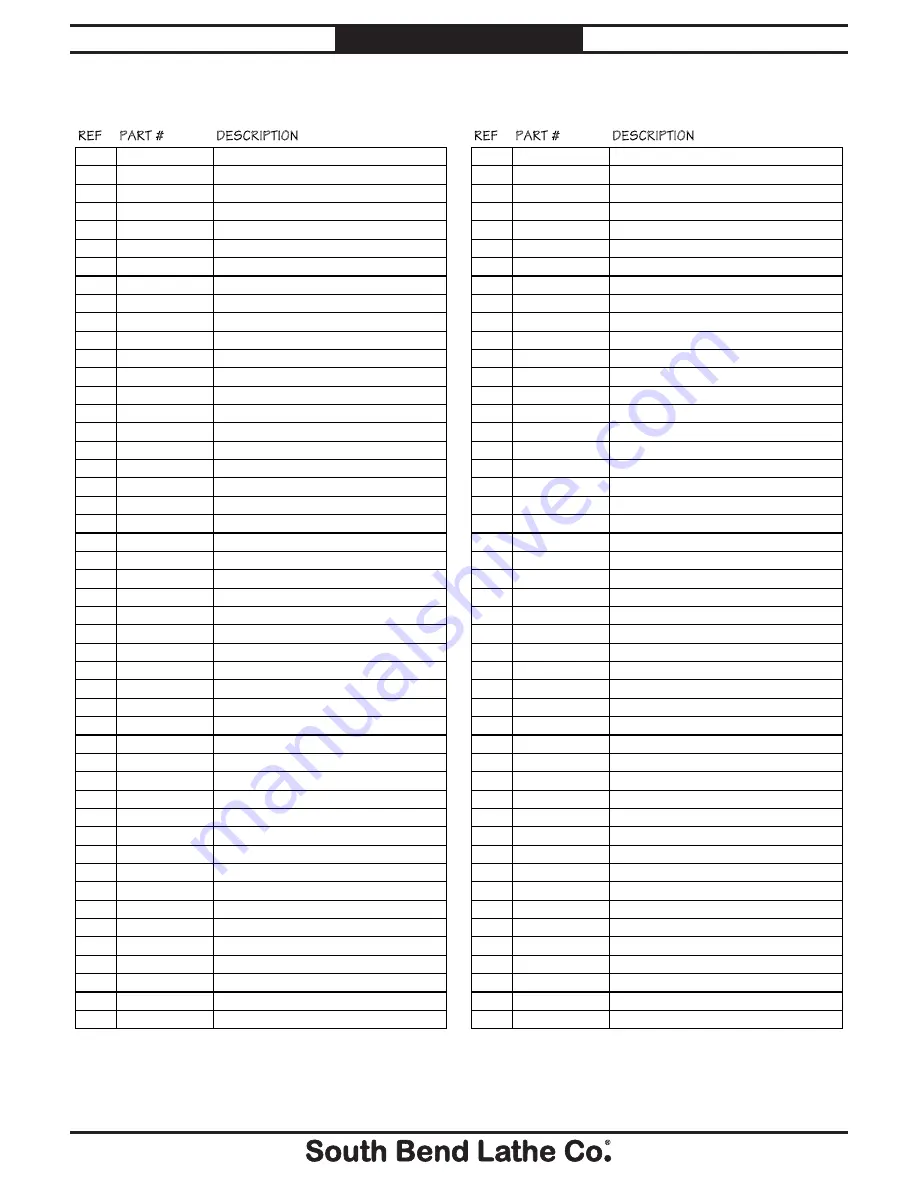
-52-
For Machines Mfg. Since 8/09
Model SB1021/SB1022
P A R T S
Drive System Parts List
REF
PART #
DESCRIPTION
REF
PART #
DESCRIPTION
100
PSB1021100
GREASE FITTING
139
PCAP84M
CAP SCREW M10-1.
5
X 3
5
101
PR03M
EXT RETAINING RING 12MM
140
PCAP63M
CAP SCREW M12-1.
75
X 60
102
P6201Z-N
BALL BEARING 6201 Z NSK
141
PSB1021141
SUPPORT ARM
103
PSB1021103
STATIONARY PULLEY
142
PSB1021142
SHAFT
104
PVM26
V-BELT M26
143
PFH0
5
M
FLAT HD SCR M
5
-.8 X 12
10
5
PSS20M
SET SCREW M8-1.2
5
X 8
144
PSB1021144
SLEEVE
106
PSB1021106
AIR PUMP PULLEY
14
5
PSB102114
5
MOVABLE PULLEY
10
7
PCAP02M
CAP SCREW M6-1 X 20
146
PFH0
5
M
FLAT HD SCR M
5
-.8 X 12
108
PLW03M
LOCK WASHER 6MM
148
PCAP11M
CAP SCREW M8-1.2
5
X 16
109
PW03M
FLAT WASHER 6MM
149
PSB1021149
SPROCKET
110
PSB1021110
PUMP HOUSING
1
5
0
PSB10211
5
0
CHAIN
111
P6201Z-N
BALL BEARING 6201 Z NSK
1
5
1
PSB10211
5
1
HUB
112
PSB1021112
PUMP ROTOR
1
5
2
PSB10211
5
2
BEARING SEAT
113
PSB1021113
ROTOR BLADE
1
5
3
P620
5
-OPEN-N BALL BEARING 620
5
OPEN NSK
114
PSB1021114
AIR NOZZLE
1
5
4
PCAP13M
CAP SCREW M8-1.2
5
X 30
11
5
PSB102111
5
AIR HOSE
1
55
PW01M
FLAT WASHER 8MM
116
PSB1021116
NOZZLE HOUSING
1
5
6
PK160M
KEY 6 X 6 X 6
5
11
7
PSB102111
7
END CAP
1
57
PK42M
KEY 6 X 6 X 30
118
PLW03M
LOCK WASHER 6MM
1
5
8
PSB10211
5
8
SHAFT
119
PCAP01M
CAP SCREW M6-1 X 16
1
5
9
PR11M
EXT RETAINING RING 2
5
MM
120
PVA40
V-BELT A40
160
PSB1021160
PILLOW BLOCK BEARING
121
PSB1021121
MOTOR PULLEY
161
PLW06M
LOCK WASHER 10MM
122
PVA36
V-BELT A36
162
PCAP84M
CAP SCREW M10-1.
5
X 3
5
123
PCAP02M
CAP SCREW M6-1 X 20
163
PSB1021163
PLATE
124
PN09M
HEX NUT M12-1.
75
164
PR08M
EXT RETAINING RING 19MM
12
5
PCAP1
7
0M
CAP SCREW M12-1.
75
X
7
0
16
5
PSB102116
5
PULLEY
126
PW06M
FLAT WASHER 12MM
166
PVA4
7
V-BELT A4
7
12
7
PSB102112
7
CONNECTOR
16
7
PCAP84M
CAP SCREW M10-1.
5
X 3
5
128
PCAP119M
CAP SCREW M12-1.
75
X
55
168
PCAP40M
CAP SCREW M8-1.2
5
X 3
5
129
PK23M
KEY
5
X
5
X 2
5
169
PSB1021169
BEARING SEAT
130
PN03M
HEX NUT M8-1.2
5
1
7
0
P6204Z-N
BALL BEARING 6204 Z NSK
131
PLW04M
LOCK WASHER 8MM
1
7
1
PK
7
4M
KEY 6 X 6 X 3
5
132
PW01M
FLAT WASHER 8MM
1
7
2
PSB10211
7
2
SPROCKET SHAFT
133
PCAP40M
CAP SCREW M8-1.2
5
X 3
5
1
7
3
PSB10211
7
3
BRACKET
134
PSB1021134
MOTOR 1HP 110/220V 1PH (SB1021)
1
7
4
PCAP84M
CAP SCREW M10-1.
5
X 3
5
134
PSB1022134
MOTOR 1HP 220V 3PH (SB1022)
1
75
PLW06M
LOCK WASHER 10MM
134-1
PSB1021134-1
MOTOR FAN COVER (SB1021)
1
7
6
PSB10211
7
6
PIVOT SHAFT
134-1
PSB1022134-1
MOTOR FAN COVER (SB1022)
1
77
PSB10211
77
PULLEY
134-2 PSB1021134-2
MOTOR FAN (SB1021)
1
7
8
PR2
5
M
INT RETAINING RING 4
7
MM
134-2 PSB1022134-2
MOTOR FAN (SB1022)
1
7
9
PSB10211
7
9
BLOCK
134-3 PSB1021134-3
MOTOR WIRING BOX (SB1021)
180
PSB1021180
SHAFT
134-3 PSB1021134-3
MOTOR WIRING BOX (SB1022)
181
PR0
5
M
EXT RETAINING RING 1
5
MM
134-4 PSB1021134-4
CAPACITOR COVER(SB1021)
182
PR21M
INT RETAINING RING 3
5
MM
134-
5
PSB1021134-
5
S CAPACITOR 400M 12
5
V (SB1021)
183
PSB1021183
PULLEY
13
5
PSB102113
5
WIRING GROMMET
184
PR21M
INT RETAINING RING 3
5
MM
136
PSB1021136
MOTOR CORD
18
5
PR0
5
M
EXT RETAINING RING 1
5
MM
13
7
PSB102113
7
BRACKET
186
P6202ZZ-N
BALL BEARING 6202 ZZ NSK
138
PLW06M
LOCK WASHER 10MM
18
7
P6202Z-N
BALL BEARING 6202 Z NSK