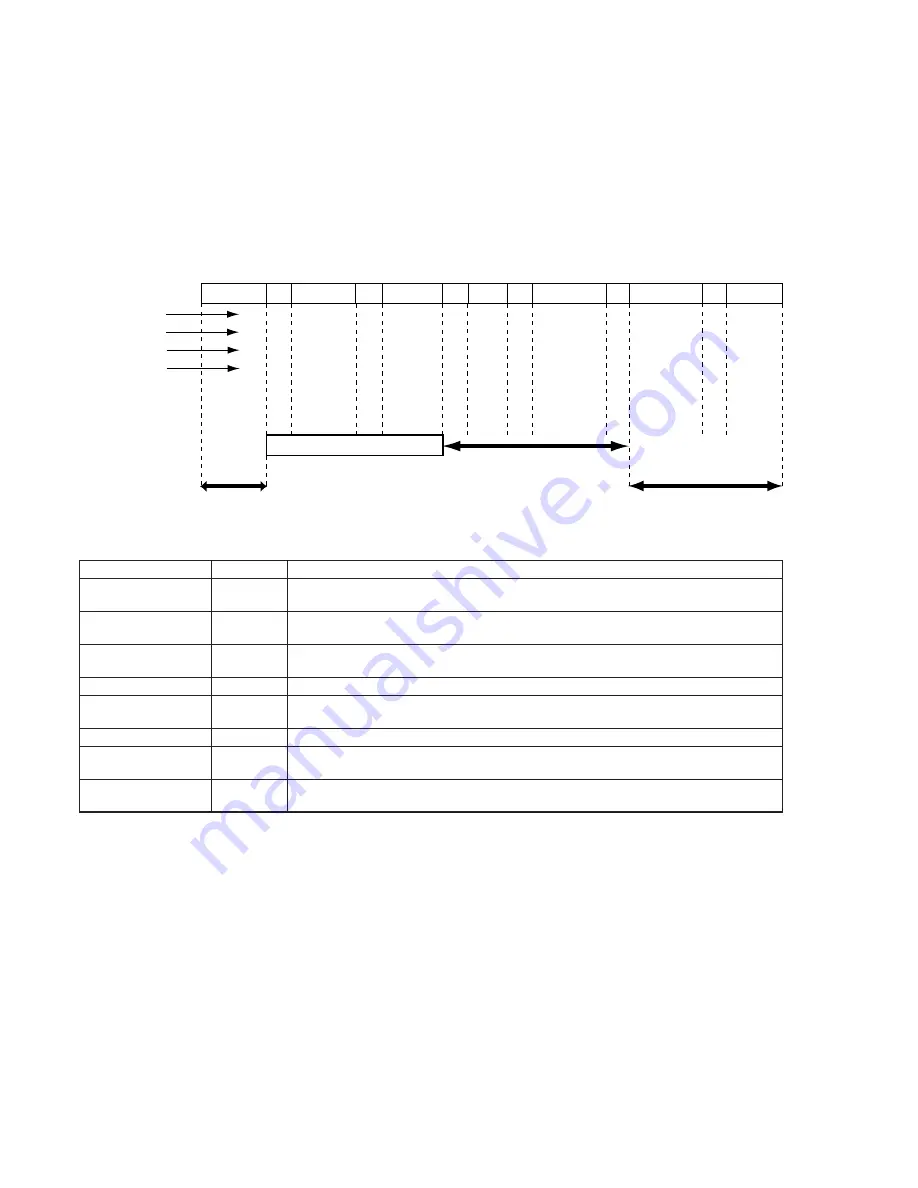
5-62
0001=1
0111=7
0011=3
0010=2
0111=7
0101=5
0111=7
0111=7
0000=0
0111=7
0100=4
0111=7
0110=6
Mechanism position
MODE SW C
MODE SW B
MODE SW A
MSB
←
Unloading
Releasing lock of
cassette campartment
LS chassis movement range
Pinch roller is pressed
Pinch roller is detached
EJECT
BL
USE
LOAD
BL
REW
BL
BL
REC/PB
BL
TURN
BL
STOP
Loading
→
Contents
Position at which the cassette compartment lock is released. The mechanism will not move any
further in the unloading direction.
BLANC code. Between two codes. The mechanism will not be stopped by this code while it is
operating.
EJECT completion position. When the cassette is ejected, the mechanism will stop at this
position.
Code during loading/unloading. Code that is used while the LS chassis is moving.
Normal stop position. The pinch roller separates, the tension regulator returns, and the brakes of
both reels turn on.
Position at which is used when the pendulum gear swings from S to T or from T to S.
PB, REC, CUE, REV, PAUSE, FF positions.
The pinch roller is pressed and tension regulator is on.
REW position. REW are carried at this position.
The mechanism will not move any further in the loading direction.
Mechanism Position
EJECT
BL
USE
LOAD
STOP
TURN
REC/PB
REW
MSW Code
1
7
3
2
6
4
0
5
2-4. MSW Code
• The lower parts of the data of C page, addresses F6, FA and FE
(or F page, addresses 12, 16 and 1A) represent the MSW codes
(mode switch mechanism position) when errors occurs.
• The upper parts of the data of C page, addresses F6, FA and FE
(or F page, addresses 12, 16 and 1A) represent, when the
mechanism position is to be moved, the MSW codes at the start
movement (when moving the loading motor).
• The lower parts of the data of C page, addresses F7, FB and FF
(or F page, addresses 13, 17 and 1B) represent the MSW codes
of the desired movement when the mechanism position is to be
moved.
Summary of Contents for HANDYCAM DCR-TRV230
Page 13: ...1 2 ...
Page 14: ...1 3 ...
Page 15: ...1 4 ...
Page 16: ...1 5 ...
Page 17: ...1 6 ...
Page 18: ...1 7 ...
Page 19: ...1 8 ...
Page 20: ...1 9 ...
Page 21: ...1 10 ...
Page 22: ...1 11 ...
Page 23: ...1 12 ...
Page 24: ...1 13 ...
Page 25: ...1 14 ...
Page 26: ...1 15 ...
Page 27: ...1 16 ...
Page 28: ...1 17 ...
Page 29: ...1 18 ...
Page 30: ...1 19 ...
Page 31: ...1 20 ...
Page 32: ...1 21 ...
Page 33: ...1 22 ...
Page 34: ...1 23 ...
Page 35: ...1 24 ...
Page 36: ...1 25 ...
Page 37: ...1 26 ...
Page 38: ...1 27 ...
Page 39: ...1 28 ...
Page 40: ...1 29 ...
Page 41: ...1 30 ...
Page 42: ...1 31 ...
Page 43: ...1 32 ...
Page 44: ...1 33 ...
Page 45: ...1 34 ...
Page 46: ...1 35 ...
Page 47: ...1 36 ...
Page 48: ...1 37E ...
Page 101: ...DCR TRV230 TRV330 TRV530 4 57 DIGITAL STILL CONTROL DS STILL PROCESS PC 082 ...
Page 107: ...DCR TRV230 TRV330 TRV530 4 69 4 70 USER FUNCTION EVF DRIVE CF 079 ...
Page 109: ...DCR TRV230 TRV330 TRV530 4 73 4 74 USER FUNCTION EVF DRIVE CF 080 ...
Page 132: ...5 1 DCR TRV230 TRV330 TRV530 SECTION 5 ADJUSTMENTS ...
Page 229: ... Take a copy of OPTICAL AXIS FRAME with a clear sheet for use 294 OPTICAL AXIS FRAME ...