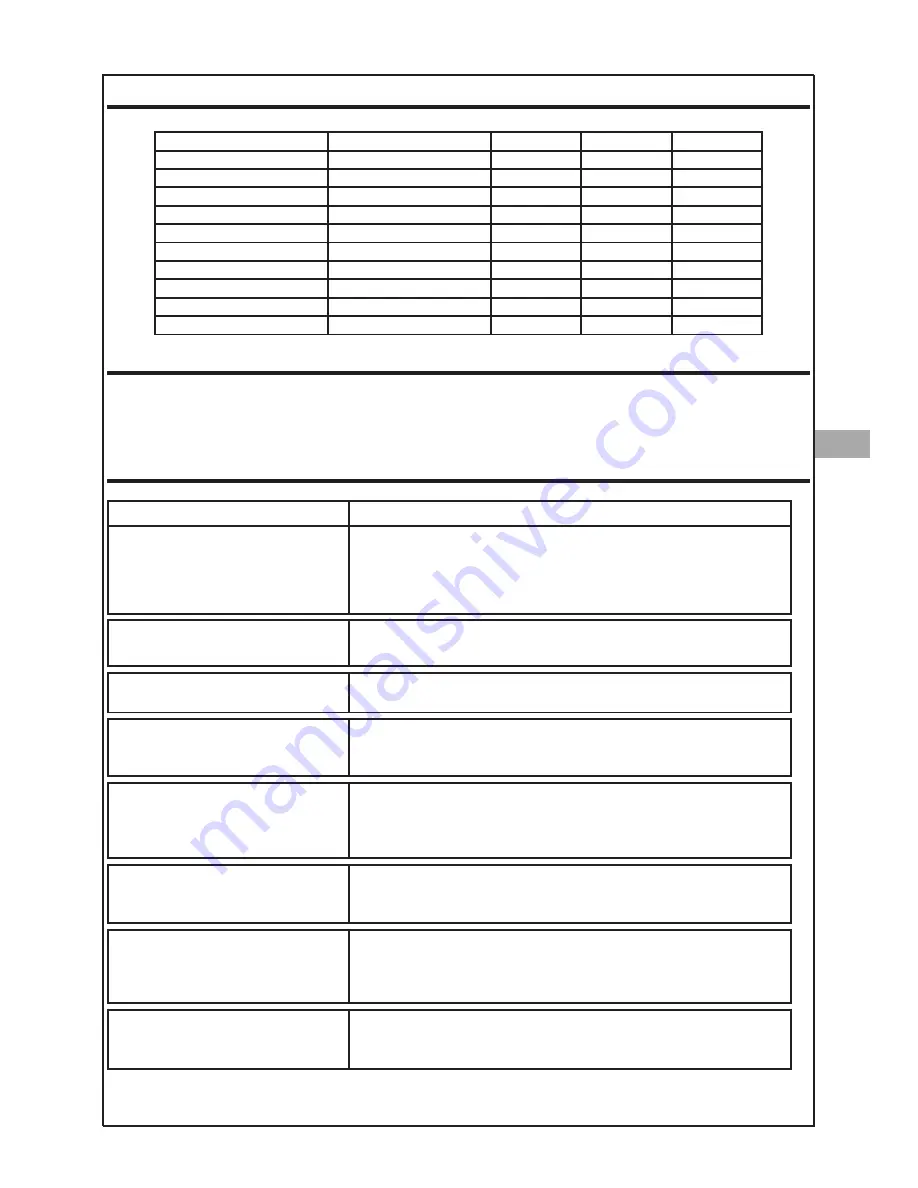
ROLLERS
FAULTS
In the event of any fault that may be hazardous to people, the machine and/or the environment, you must disconnect
the machine immediately and make sure it cannot be reconnected until the problem that caused the fault has been
solved. Faults should only be eliminated by qualified personnel, taking into account the safety instructions of the ma-
chine.
POSSIBLE ANOMALIES AND SOLUTIONS
ROLLERS
MATERIAL
2000
3200
3220
0,6 - 0,8 V groove
Fe, SS,CuSi, CuAl
56105
-
55606
0,8 - 1,0 V groove
Fe, SS,CuSi, CuAl
56106
55600
-
1,0 - 1,2 V groove
Fe, SS,CuSi, CuAl
55986
55601
55607
1,2 - 1,6 V groove
Fe, SS,CuSi, CuAl
-
55602
55608
0,8 - 1,0 U groove
Al
55987
55612
-
1,0 - 1,2 U groove
Al
55988
55603
55609
1,2 - 1,6 U groove
Al
-
-
55610
0,8 - 1,0 Knurled groove
Flux Core, Metal Core
56116
-
-
1,0 - 1,2 Knurled groove
Flux Core, Metal Core
55989
55604
55611
1,2 - 1,6 Knurled groove
Flux Core, Metal Core
-
55605
55613
ANOMALY
POSSIBLE CAUSE
The machine doesn’t start up
Verify the mains
Defective main switch.
Turn off the machine or unplug it from the mains for 1 minute and try to
start it up again.
Electronic circuit is defective.
Anomaly indicator lights up
Turn off the equipment for a minute and start it up again. If the error
persists, contact technical service.
Overtemperature indicator lights up
The machine has become overheated. Wait until the machine regains a
safe temperature.
Output indicator is flashing
The equipment has found that the torch push button was pressed du-
ring startup or when recovering from an overtemperature fault. Release
the button of the torch and/or pedal.
The wire does not come out correctly
Verify that the drive system rotates correctly.
Verify that the coil brake is not too tight.
Verify that the drive system accessories are in good conditions.
Verify that the torch and consumables are in good conditions.
The wire does not come out at the
proper speed
At the beginning of the welding, the wire always comes out with a mini-
mum speed. Verify that the wire feeding system works properly with the
manual feeding button
.
Shielding gas doesn’t comes out
Check that there is gas in the bottle.
Check that the flow rate adjustment is correct.
Verify that torch is not pinched and / or perforated.
Gas valve defective.
The arc is not stable and the wire
collides with the workpiece.
Check if the material used corresponds to the selected in the machine.
Verify that consumables and rollers are appropriate with the material in
use.
SOLTER
SOLDADURA S.L.
AEROPROCESS
19
EN
Summary of Contents for aeroprocess 2000
Page 44: ...AEROPROCESS 2000 AEROFEED 5 69000271 SOLTER SOLDADURA S L AEROPROCESS A1...
Page 45: ...AEROPROCESS 3200 SOLTER SOLDADURA S L AEROPROCESS A2...
Page 46: ...AEROPROCESS 3220 SOLTER SOLDADURA S L AEROPROCESS A3...
Page 47: ...SOLTER SOLDADURA S L AEROPROCESS A4...
Page 48: ...SOLTER SOLDADURA S L AEROPROCESS A5...
Page 49: ...SOLTER SOLDADURA S L AEROPROCESS A6...
Page 50: ...SOLTER SOLDADURA S L AEROPROCESS A7 SOLTER SOLDADURA S L AEROPROCESS A7...