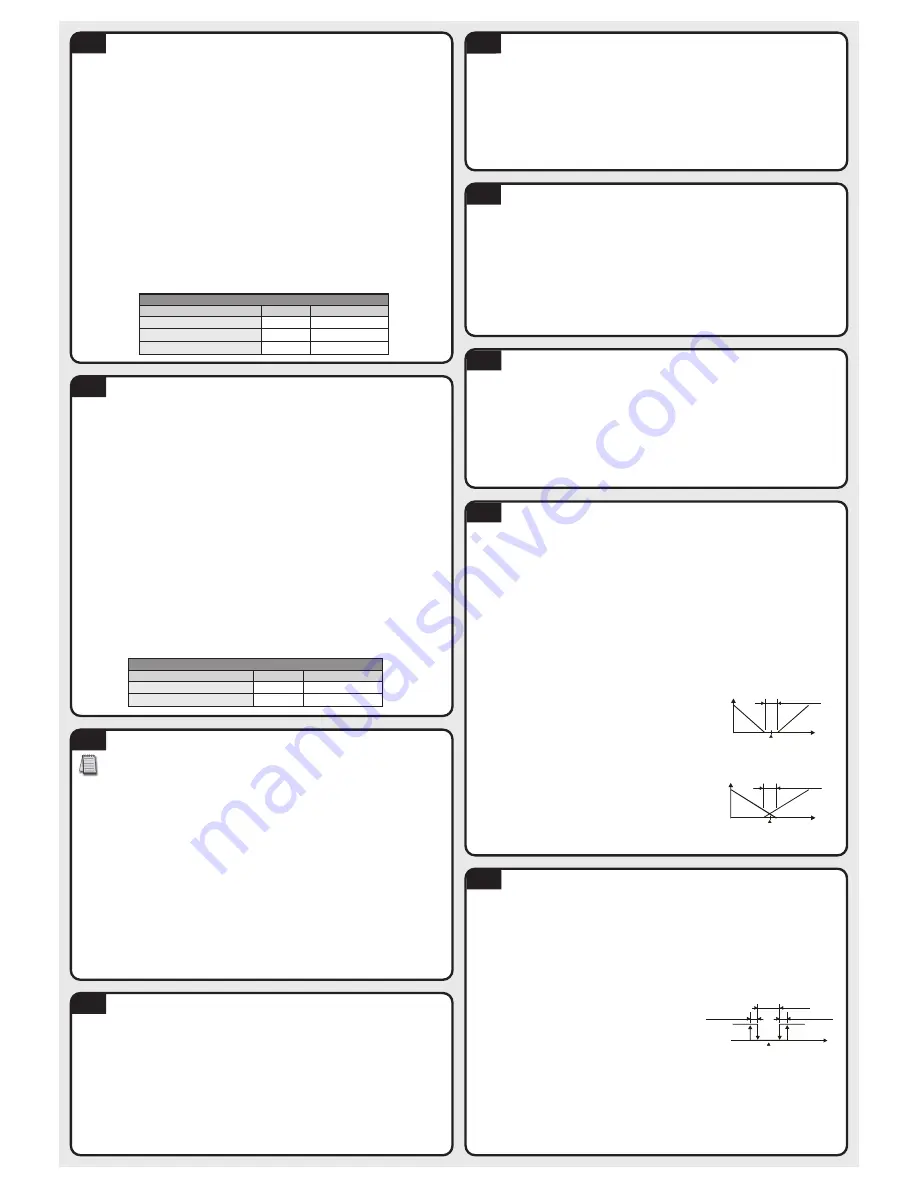
Current Input
1. Install the supplied 249 ohm resistor between terminal #4 and #6.
2. Access the Initial Setup mode by pressing and holding the
;
button for three seconds. In the parameter
inpt
, use the
,
and
.
buttons to select the value that corresponds to the current input that will be
applied to the controller. See the table for current specifications. Press the
;
button to save the selected
value. The controller will display the module information splash screen for three seconds and then return to the
main screen.
3. Press the
;
button for three seconds again. Press the
'
button repeatedly until the parameter
tp-h
appears. Use the
,
and
.
buttons to select the high engineering value that corresponds to the maximum
current signal that will be applied to the input of the controller. For example, if the
ma4
4-20mA input is to be
used, this is the value the controller will display when the input equals 20mA. Press the
;
button to save the
selected value. Press the
'
button to access the parameter
tp-l
. Use the
,
and
.
buttons to select
the low engineering value that corresponds to the minimum current signal that will be applied to the input of the
controller. For example, if the
ma4
4-20mA input is to be used, this is the value the controller will display when
the input equals 4mA. Press the
;
button twice to save the selected value and return to the controller main
screen.
4. Press the
'
button repeatedly until the parameter
sp
appears. Use the
,
and
.
buttons to select
0
,
1
,
2
or
3
to indicate the position of the decimal point for the PV and SV values on the controller. Press the
;
button twice to save the selected value and return to the controller main screen.
5. If the current input PV value displayed on the controller needs to be adjusted, press the
;
button for less
than 3 seconds. Press the
'
button repeatedly until the parameter
tpof
appears. Use the
,
and
.
buttons to adjust a positive or negative offset to the PV value displayed on the controller. Press the
;
button
twice to save the selected value and return to the controller main screen.
Current Input Type and Range
Current Input Type
LED Display
Engineering Range
4~20mA Analog Input
ma4
-999 ~ 9999
0~20mA Analog Input
ma0
-999 ~ 9999
Heating Loop with PID Control
PID Control Setup
1. Access the Initial Setup mode by pressing and holding the
;
button for three seconds. Press the
'
button repeatedly until the parameter
Ctrl
appears. Confirm the default value
Pid
is selected for PID
control. Press the
'
button to access the parameter
s-hC
.
Confirm the default value
heat
is select-
ed for controlling a heating loop. Press the
;
button to return to the controller main screen.
2. Press the
'
button to access the parameter
r-s
. Verify that the default value
run
is selected. Press
the
;
button to return to the controller main screen.
3. Refer to Section 12-1 of this Quick Start Guide to set up the PID control parameters.
4. If the temperature controller’s output #1 is discrete, access the regulation mode again by pressing the
;
button for less than three seconds. Press the
'
button repeatedly until the parameter
htpd
appears. Use
the
,
and
.
buttons to set the time period in seconds for the heating control. Press the
;
button twice
to save the value and return to the controller main screen.
There are four groups for storing PID parameters,
pid0
(PID0) -
pid3
(PID3). Press the
;
button for
less than three seconds and press the
'
button repeatedly until the parameter
pid0
appears. Use the
,
and
.
buttons to select which group to use for storing the PID parameters. Press the
;
button to
confirm the setting. The groups
pid0
-
pid3
can be individually set up with different SV values to be used
in the control process. If the group
pid4
is selected, the controller will automatically select the most useful
PID parameters based on the current temperature setting and the SV value set in each PID group.
The parameters for PID can be auto-tuned using the
At
parameter. Access this parameter by pressing the
;
button for less than three seconds. Use the
.
button to turn the auto-tune feature
on
. Press the
;
button
to save the value. Optimal PID values are automatically determined with the auto-tune feature. PID operation
can also be controlled by programming the individual
p
,
i
, and
d
parameters for each PID group. Access these
parameters by pressing the
;
button for less than three seconds and press the
'
button repeatedly until
the parameter
pn
appears where
n
corresponds to the PID group you are programming. Use the
,
and
.
buttons to change the value for the Proportional band if desired and press the
;
button to save the
value. Press the
'
button to access the
in
parameter. Use the
,
and
.
buttons to change the value
for the Integral time if desired and press the
;
button to save the value. Press the
'
button to access the
dn
parameter. Use the
,
and
.
buttons to change the value for the Derivative time if desired and press
the
;
button twice to save the value and return to the controller main screen.
Voltage Input
1. Access the Initial Setup mode by pressing and holding the
;
button for three seconds. In the parameter
inpt
, use the
,
and
.
buttons to select the value that corresponds to the voltage input that will be
applied to the controller. See the table for voltage specifications. Press the
;
button to save the selected
value. The controller will display the module information splash screen for three seconds and then return to the
main screen.
2. Press the
;
button for three seconds again. Press the
'
button to access the parameter
tp-h
. Use
the
,
and
.
buttons to select the high engineering value that corresponds to the maximum voltage signal
that will be applied to the input of the controller. For example, if the
V5
0V-5V input is to be used, this is the
value the controller will display when the input equals 5V. Press the
;
button to save the selected value.
Press the
'
button to access the parameter
tp-l
. Use the
,
and
.
buttons to select the low engi-
neering value that corresponds to the minimum voltage signal that will be applied to the input of the controller.
For example, if the
V5
0V-5V input is to be used, this is the value the controller will display when the input
equals 0V. Press the
;
button twice to save the selected value and return to the controller main screen.
3. Press the
'
button repeatedly until the parameter
sp
appears. Use the
,
and
.
buttons to select
0
,
1
,
2
or
3
to indicate the position of the decimal point for the PV and SV values on the controller. Press the
;
button twice to save the selected value and return to the controller main screen.
4. If the voltage input PV value displayed on the controller needs to be adjusted, press the
;
button for less
than 3 seconds. Press the
'
button repeatedly until the parameter
tpof
appears. Use the
,
and
.
buttons to adjust a positive or negative offset to the PV value displayed on the controller. Press the
;
button
twice to save the selected value and return to the controller main screen.
Cooling Loop with ON / OFF Control
1. Access the Initial Setup mode by pressing and holding the
;
button for three seconds. Press the
'
button repeatedly until the parameter
Ctrl
appears. Use the
,
and
.
buttons to select
onof
for ON
/ OFF control. Press the
;
button to save the value. Press the
'
button to access the parameter
s-hC
.
Use the
.
button to select
Cool
for controlling a cooling loop. Press the
;
button twice to save the value
and return to the controller main screen.
2. Press the
'
button to access the parameter
r-s
. Verify that the default value
run
is selected. Press
the
;
button to return to the controller main screen.
3. Press the
;
button for less than three seconds to access the parameter
Cts
. Use the
,
and
.
buttons to enter hysteresis. This is the amount the PV must go above the SV before the controller output turns
on. Press the
;
button twice to save the selected value and return to the controller main screen.
Dual Heating / Cooling Loop with PID Control
1. Access the Initial Setup mode by pressing and holding the
;
button for three seconds. Press the
'
button repeatedly until the parameter
Ctrl
appears. Confirm the default value
Pid
is selected for PID
control. Press the
'
button to access the parameter
s-hC
. Use the
.
button to select
h1C2
for
controlling a dual heating / cooling loop. This parameter sets the heating control to output #1 and the cooling
control to output #2. Press the
;
button twice to save the value and return to the controller main screen.
2. Press the
'
button to access the parameter
r-s
. Verify that the default value
run
is selected. Press
the
;
button to return to the controller main screen.
3. Refer to Section 12-1 of this Quick Start Guide to set up the PID control parameters.
4. If the temperature controller’s output #1 is discrete, access the regulation mode again by pressing the
;
button for less than three seconds. Press the
'
button repeatedly until the parameter
htpd
appears. Use
the
,
and
.
buttons to set the time period in seconds for output #1, the heating control. Press the
;
button to save the value. If the temperature controller’s output #2 is discrete, press the
'
button repeatedly until
the parameter
hCpd
appears. Use the
,
and
.
buttons to enter the cycle period in seconds for output
#2, the cooling output. Press the
;
button twice to save the value and return to the controller main screen.
5. Optional regulation parameters can be programmed for a second
control output. If this is desired, access the regulation mode again by
pressing the
;
button for less than three seconds. Press the
'
button until the parameter
Coef
appears. This value allows the cooling
control to have a different proportional setting than the heating loop. The
heating loop proportional band setting is multiplied by the
Coef
value to
create a proportional band setting for the cooling loop control. Use the
,
and
.
buttons to change this value if desired. Press the
;
button to save the selected value. Press the
'
button to access the
parameter
dead
. Use the
,
and
.
buttons to enter a deadband
zone value around the setpoint where the output is not effected by the
proportional control value. As long as the PV remains within the deadband
zone the output is not affected by the proportional control. The integral and
derivative controls ignore the deadband setting and may cause the output
to be on within the deadband zone. Press the
;
button twice to save
the value and return to the controller main screen.
11-2
Voltage Input Type and Input Range
Voltage Input Type
LED Display
Engineering Range
0~50mV Analog Input
mv
-999 ~ 9999
0V~10V Analog Input
v10
-999 ~ 9999
0V~5V Analog Input
v5
-999 ~ 9999
11-3
12-1
12-2
12-5
12-6
Dual Heating / Cooling Loop with ON / OFF Control
1. Access the Initial Setup mode by pressing and holding the
;
button for three seconds. Press the
'
button repeatedly until the parameter
Ctrl
appears. Use the
,
and
.
buttons to select
onof
for ON
/ OFF control and press the
;
button to save the selected value. Press the
'
button to access the param-
eter
s-hC
. Use the
.
button to select
h1C2
for controlling a cooling / heating loop. This parameter sets
the heating control to output #1 and the cooling control to output #2. Press the
;
button twice to save the
value and return to the controller main screen.
2. Press the
'
button to access the parameter
r-s
. Verify that the default value
run
is selected. Press
the
;
button to return to the controller main screen.
3. Press the
;
button for less than three seconds to access the
parameter
hts
. Use the
,
and
.
buttons to enter hysteresis
for output #1, the heating control. This is the amount the PV must go
below the SV before the controller output turns on. Press the
;
button to save the selected value. Press the
'
button to access
the parameter
Cts
. Use the
,
and
.
buttons to enter
hysteresis for output #2, the cooling control. This is the amount the
PV must go above the SV before the controller output turns on. Press
the
;
button twice to save the selected value and return to the
controller main screen.
4. Optional regulation parameters can be programmed for additional dual loop control. If this is desired, access
the regulation mode again by pressing the
;
button for less than three seconds. Press the
'
button
repeatedly until the parameter
dead
appears. Use the
,
and
.
buttons to enter a deadband zone value
around the setpoint where the output is not on. The PV must go beyond the deadband range in order for either
the heating or cooling output to turn on. Press the
;
button twice to save the selected value and return to the
controller main screen.
12-7
OFF
PV
Set point
ON
Heating
Dead band
Heating hysteresis
Cooling hysteresis
Cooling
hts
Cts
dead
Dual loop ON / OFF control
output operation
PV
0
Output
Dead band: dead
band width=positive
Set point
Heating
Cooling
dead
PV
0
Output
Dead band: dead
band width=negative
Set point
Heating
Cooling
dead
Dual control with PID
positive deadband
Dual control with PID
negative deadband
Heating Loop with ON / OFF Control
1. Access the Initial Setup mode by pressing and holding the
;
button for three seconds. Press the
'
button until the parameter
Ctrl
appears. Use the
,
and
.
buttons to select
onof
for ON / OFF
control. Press the
;
button to save the value. Press the
'
button to access the parameter
s-hC
.
Confirm the default value
heat
is selected for controlling a heating loop. Press the
;
button to return to
the control
ler main screen.
2. Press the
'
button to access the parameter
r-s
. Verify that the default value
run
is selected. Press
the
;
button to return to the controller main screen.
3. Press the
;
button for less than three seconds to access the parameter
hts
. Use the
,
and
.
buttons to enter hysteresis. This is the amount the PV must go below the SV before the controller output turns
on. Press the
;
button twice to save the selected value and return to the controller main screen.
12-3
Cooling Loop with PID Control
1. Access the Initial Setup mode by pressing and holding the
;
button for three seconds. Press the
'
button repeatedly until the parameter
Ctrl
appears. Confirm the default value
Pid
is selected for PID
control. Press the
'
button to access the parameter
s-hC
. Use the
.
button to select
Cool
for
controlling a cooling loop. Press the
;
button twice to save the value and return to the controller main screen.
2. Press the
'
button to access the parameter
r-s
. Verify that the default value
run
is selected. Press
the
;
button to return to the controller main screen.
3. Refer to Section 12-1 of this Quick Start Guide to set up the PID control parameters.
4. If the temperature controller’s output #1 is discrete, access the regulation mode again by pressing the
;
button for less than three seconds. Press the
'
button repeatedly until the parameter
Clpd
appears. Use
the
,
and
.
buttons to set the time period in seconds for the cooling control. Press the
;
button twice
to save the value and return to the controller main screen.
12-4
Note: Select the desired control mode before beginning PID Control Setup.