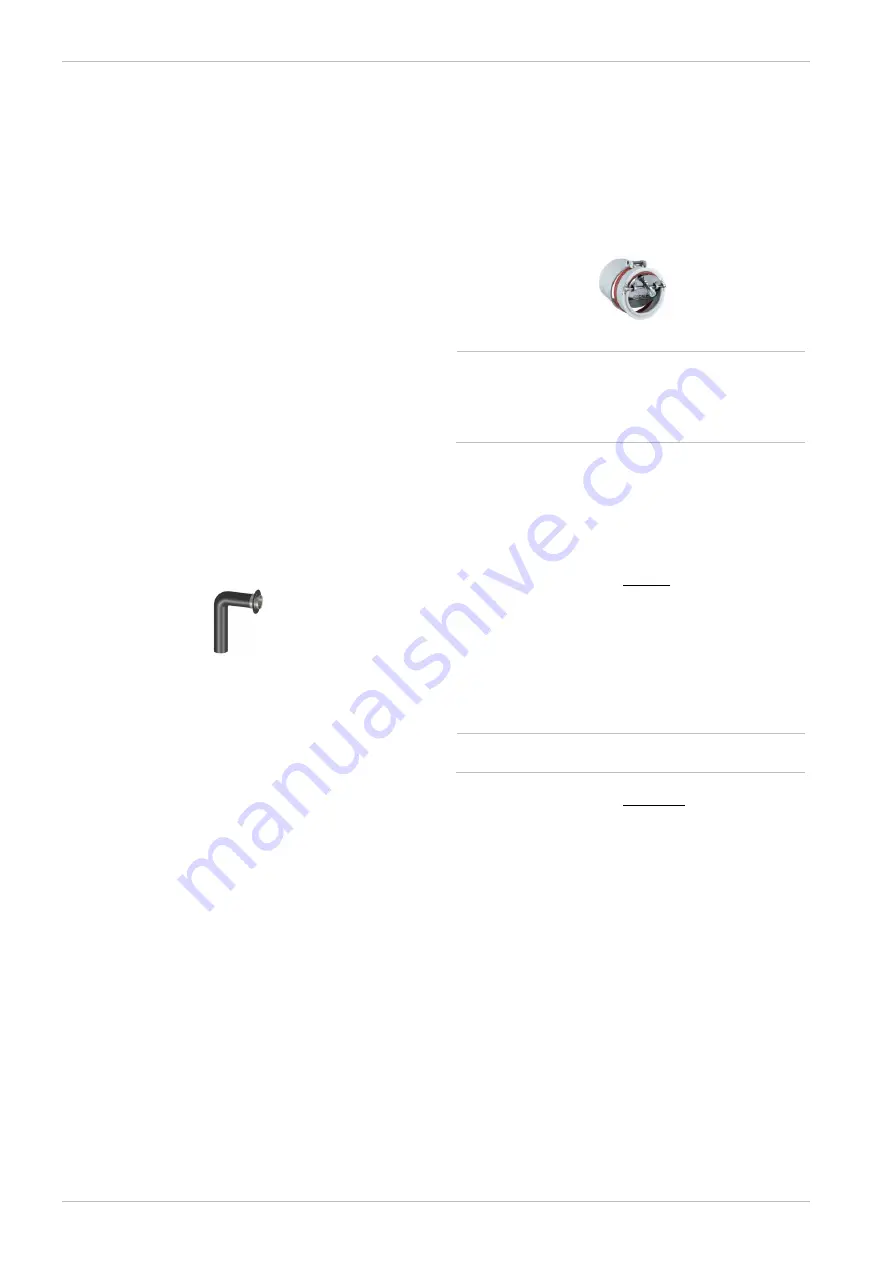
Technical requirements
6
Installation manual
octo
plus
Provide each boiler with its own chimney
- The boiler and the chimney must be coordinated.
This is the only way to ensure the proper function-
ing of the heating system and the correct dis-
charge of the flue gases.
- If there is only one chimney available for two boil-
ers, there is a risk (considering the different oper-
ating states of the boilers - full load/partial load) of
poor coordination. This can lead to problems (e.g.
the flue gas has too little energy during the as-
cent, and does not lift off sufficiently from the
chimney mouth, ...odour pollution by flue gases).
- Chimneys with just one device are more reliable
and safer than chimneys with multiple devices.
Do not connect a gas boiler and blower boiler to
the same chimney
Do not connect a wood-burning stove and
blower boiler to the same chimney
- A wood-burning stove typically requires a larger
chimney diameter than the blower boiler.
- Acoustic disturbance from the blower boiler may
be possible in the living room (by the wood-burn-
ing stove).
- Unnecessary risk due to gas leakage, e.g. if the
blower boiler is defective.
Execution of the flue gas pipe
-
Run the flue gas pipe towards the chimney in
a short and rising direction, with as few
changes of direction as possible.
- Change direction in the form of aerodynamically
favourable arcs, do not build kinks.
- The diameter of the flue gas pipe to the chimney
may be enlarged if required, but may not be re-
duced.
- Place the inlet of the flue gas pipe in the chimney
just below the ceiling.
- The flue gas pipe must be tight. Seal seal-less
flue gas pipes on site with heat-resistant silicone.
Insulate flue gas pipe
- Insulate the flue gas pipe continuously from the
boiler to the chimney.
- Recommended insulation thickness: 50 mm rock-
wool.
- Serves to prevent temperature loss and prevents
the consequential formation of condensation.
Cleaning opening in the flue gas pipe
- To clean the flue gas pipe (e.g. removal of accu-
mulated flue ash) there must be an easily accessi-
ble cleaning opening.
- Recommendation: Coordinate the number and
placement of the cleaning openings with the chim-
ney sweep.
Opening for emissions measurement in the flue
gas pipe
Make an opening (hole) in the flue gas pipe to per-
form the prescribed emission measurement
Minimum draught requirement for boiler: 5 Pa
A draught stabiliser must be fitted if the specified
draught of 15 Pa is exceeded.
Install explosion flap
Fig. 2-1: Explosion flap integrated into draught stabiliser
Before longer horizontal pipe sections
(L>20xD) and at the high point before drop-
ping down the flue gas pipe, an explosion flap
must be installed, independent of the boiler
output.
In the case of boiler output <50 kW, no explosion
flap is required (in the case of a short and rising flue
gas pipe to the chimney).
3.5 Supply air in the installation room
The following applies for Austria (in accordance with
H 5170):
- For the supply air, 2 cm² per kW thermal output of
the fuel, but allow at least 200 cm² free cross-sec-
tion. (Thermal output of fuel = boiler output / effi-
ciency) For the exhaust air, allow at least 180 cm²
free cross-section up to 100 kW nominal heat and
an additional 1 cm² free cross-section for every
further kW.
Calculate at least a further 20% for wire mesh
in the aeration cross-section.
The following applies for Germany (according to
specimen firing ordinance):
- For heating appliances with a nominal output of
up to 35 kW, a combustion air opening of at least
150 cm² or 2 x 75 cm² routed directly into the
open air must be provided.
- Alternatively, a door/window leading outside and a
room content of at least 4 m³/kW nominal heat
output are suitable. If the installation room does
not abut onto an outside wall, combustion air sup-
ply via connecting rooms is possible. Here, the
combustion air is supplied via a sufficiently dimen-
sioned adjacent room which abuts onto an outside
wall.
- From 35 to 50 kW, provide a free aeration cross-
section of at least 150 cm². From 50 kW upwards,
for aeration and ventilation, provide a minimum
free cross-section of 150 cm² for each, plus 2 cm²
per KW in excess of 50 kW.
Summary of Contents for octoplus
Page 40: ...Initial commissioning 40 Installation manual octoplus 8 1 Commissioning log...
Page 41: ...Initial commissioning Installation manual octoplus 41...
Page 42: ...Initial commissioning 42 Installation manual octoplus 8 2 Customer service order form...
Page 45: ...System schematic Installation manual octoplus 45...
Page 46: ...System schematic 46 Installation manual octoplus...
Page 47: ...System schematic Installation manual octoplus 47...