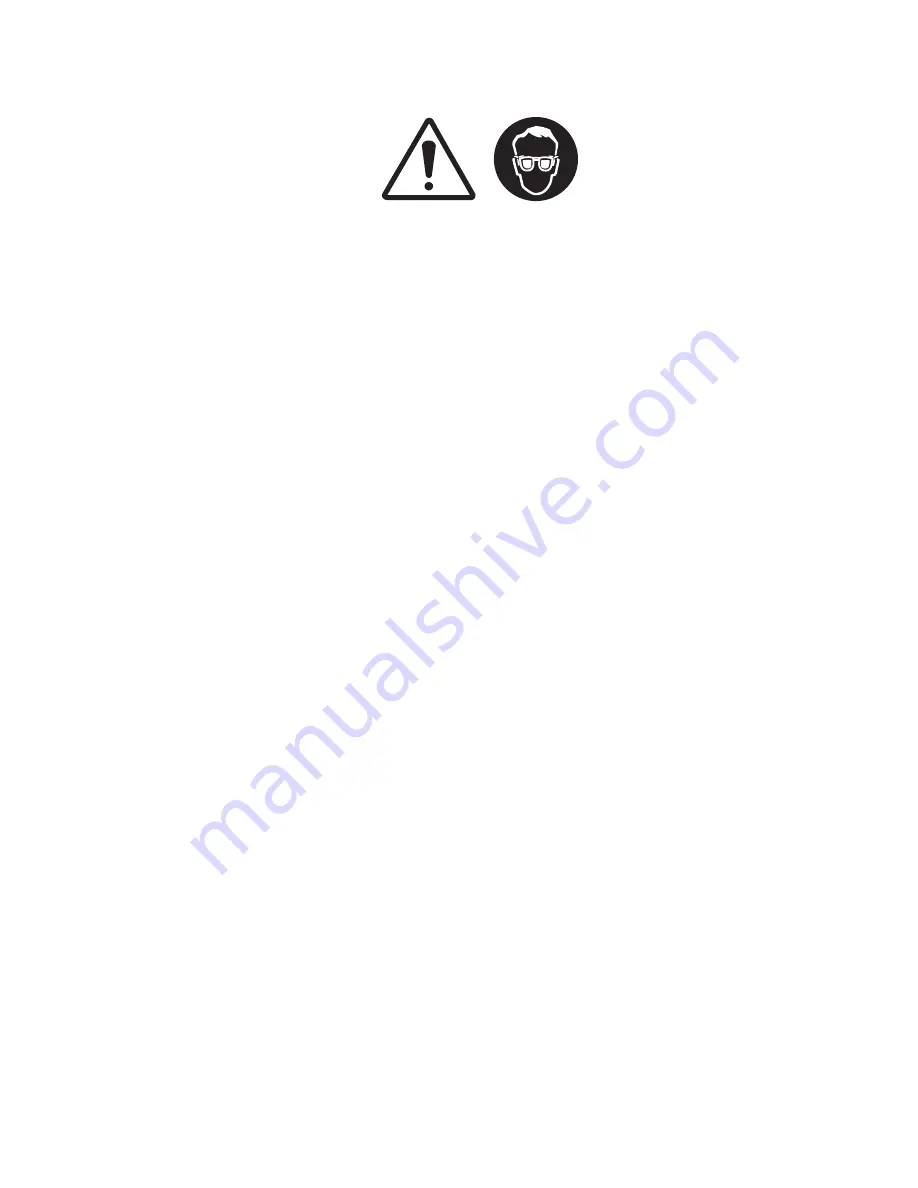
INK FOUNTAIN CLEANING INSTRUCTIONS
MODEL 6503 MACHINE
Suggest Sohn C-100 cleaning kit which contains the following essential items: Rubber Gloves, 1 Small
Handle Brush, 1 Round Brush, 1 Square Shallow Pan, 1 Scraping Knife, 1 Alignment Tool, 1 Gallon Sohn
Super Cleaner (Type C), 1 Qt. Sohn Fountain Cleaner (Type B).
It is recommended to disassemble and clean the fountain at end of job.
1. Remove ink fountain from machine and place on flat surface. Loosen Dr. Blade screws.
2. Remove the four brass thumb screws and take cover off.
3. Remove Dr. Blade assembly (inspect for need of replacement).
4. With a 3/32 allen wrench, loosen the set screws on the left and right side of the ink roller.
5. Remove the shaft and gear assembly from the ink fountain (pry with screwdriver if necessary).
1. Wash in Type C Cleaner when using water base ink.
2. Rinse in water. Dry with paper towel.
To reassemble, reverse the disassembly process. A fountain line-up tool (T-bar) should be used to
assist you in realigning the ink roller.
1. Insert the gear and shaft assembly on the left side of the fountain body (as the front of the ink
fountain is facing you).
2. Slide the "O" ring first, then the retainer onto the shaft.
3. Insert the T-bar on the right side of the fountain body.
4. Slide the "O" ring first, then the retainer onto the T-bar.
5. Place the ink roller between the retainers on the left and right side. Align the shaft of the gear and
shaft assembly into the roller on the left side, and the shaft of the T-bar into the roller on the right
side.
6. Push the gear and shaft assembly completely through, replacing the T-bar shaft.
7. Lock the set screws on the roller (there are two flat areas on the shaft. The set screws should be
tightened on these flat areas).
8. Put Dr. Blade assembly into fountain.
9. Replace cover and tighten with four brass thumb screws.
10. Put a small amount of pressure on Dr. Blade screws.
***********
The ink fountain is the heart of your printing machine. Use a regular cleaning schedule and keep the
fountain away from lint and dust. Extreme gear wear and bad printing can often be traced to a dirty fountain.
Inspect the doctor blade regularly and replace if excessive wear is apparent.
It is recommended that the ink fountain be returned to the factory for inspection and maintenance if
excessive wear or malfunction is apparent.
DISASSEMBLY:
WASHING FOUNTAIN:
REASSEMBLY:
12
Summary of Contents for 6503
Page 9: ...E G G E 7 ...