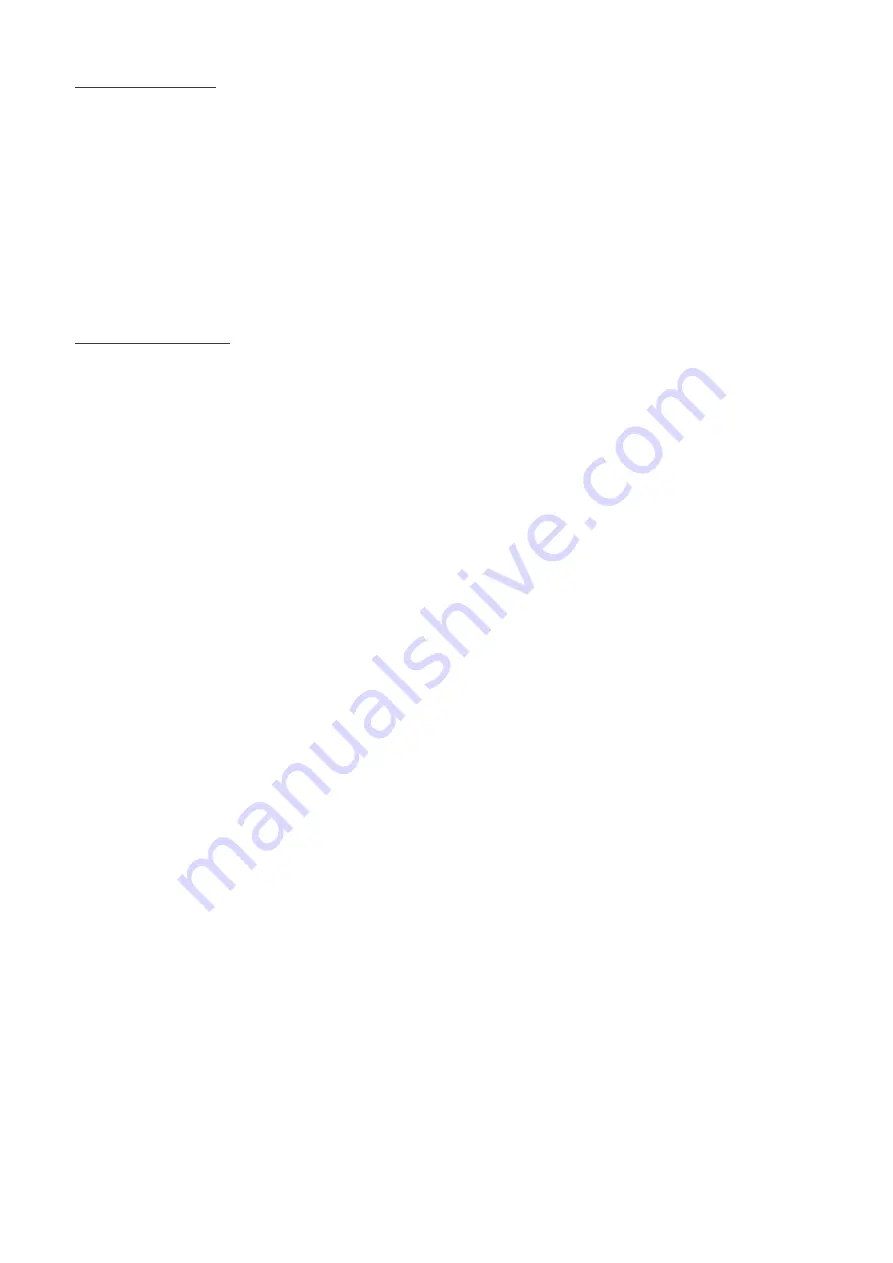
Using IRxxx :
Ü
Connect Work lead to working table or job. Keep welding holder away from work
connections.
Ü
Switch on mains from socket and from backside MCB.
Ü
Select and clamp desired welding electrode in holder and set welding current according
to rod size as mentioned on it’s cartoon.
Ü
Make a trial weld, then modify current setting if needed.
Ü
Machine is ready for production work.
Using IRTxxx :
Ü
For arc welding, move toggle switch towards MMA on front panel of machine and do
the same procedure as written above for IRxxx.
Ü
For Tig Welding do following steps.
Ü
Connect Work lead from +ve terminal to working table or job.
Ü
Connect Tig torch at -ve terminal and connect gas pipe at gas nipple and connect torch
plug.
Ü
Place a sharp grinded tungsten electrode in torch head and tight 2-4 mm outside of
ceramic nozzle.
Ü
Connect shielding gas(argon) at gas inlet nipple, backside of machine.
Ü
Switch on mains from socket and from backside MCB.
Ü
Push Gas Check Button from front panel and adjust the gas flow from gas regulator
and flow-meter according to working conditions. Preferably between 2 to 6 liter per
minute
Ü
Program Gas Pre-flow time:
1. Set TIG/MMA switch back to MMA.
2. Rotate post-flow knob in MMA position. Screen show Pre-flow sec., Set the
desired value, if not sure set it to minimum (0.1 sec.). After a second screen
shows pre flow saving. when saving message changed to Welding Current. Set
TIG/MMA seitch to TIG mode.
3. Every time when Pre-flow will done. Don’t forget to set Post Flow Time.
Ü
Set Post-Flow time between 2 to 5 sec. If want to use machine at full current set it to 5
second.
Ü
Set welding current according to job.
Ü
Make a trial weld, then modify current setting if needed.
Ü
Machine is ready for production work.
6