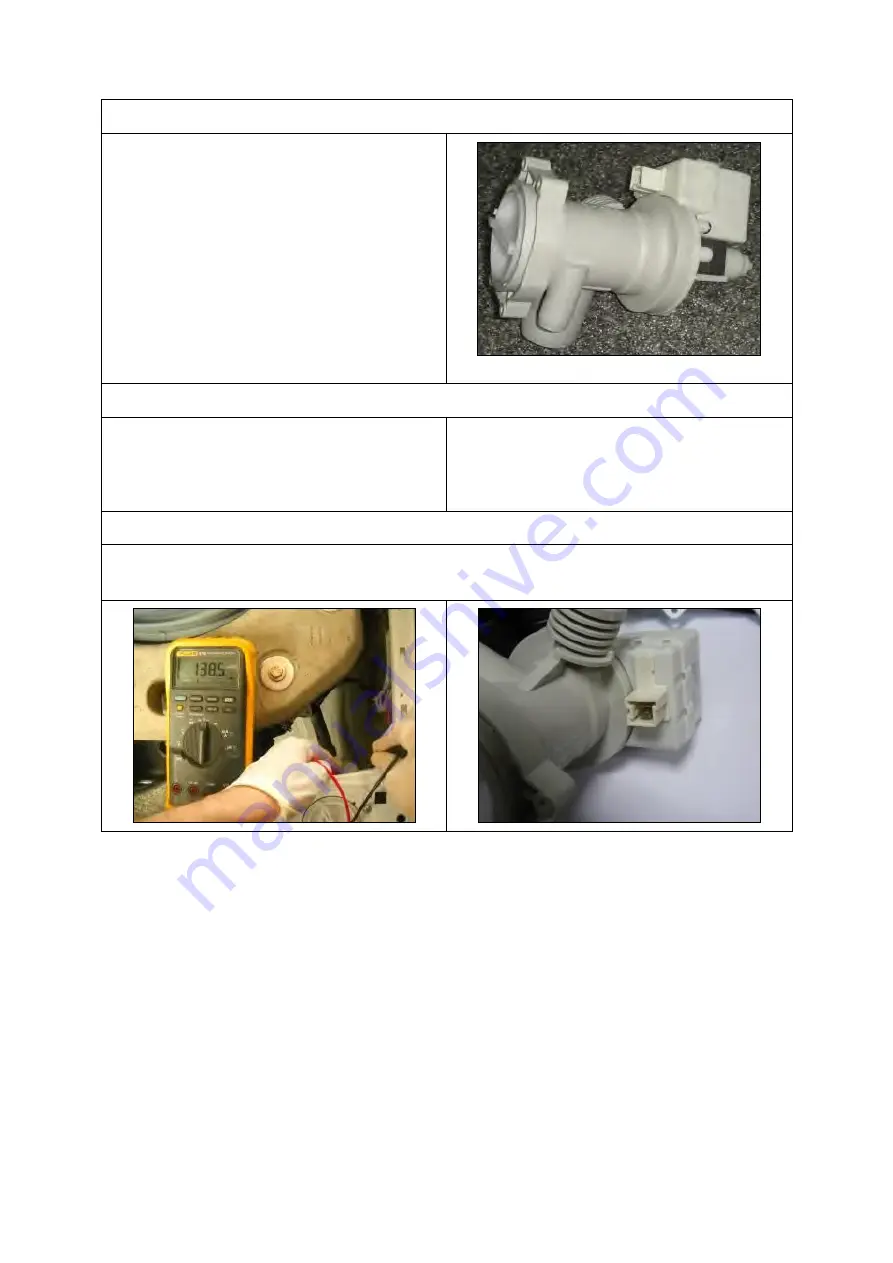
8. Component Specifications
8.1. Drain Pump
Drain pump is both a mechanical and electrical
component which is used to drain water inside
the washing machine. It has an synchronous
motor
inside.
For
better
performance
maintanance, pump filter should be cleaned
regularly.
Drain pump
Technical features
Nominal voltage
220-240 V
Nominal current
0.28 A (±10 %)
Nominal power
30 W (±20 %)
Frequency
50 Hz
Resistor (coil)
125 Ω (±5%)
Water flow
17 L/min(to 1 m
height)
Thermal protector
YES
Testing component
Check the resistance value on the component with multimeter as shown below.
Resistance value should be between 125 Ω (±5%)
Summary of Contents for D4 Series
Page 1: ...Manuel de service Séries D4 ...
Page 37: ...9 Wiring Diagram ...