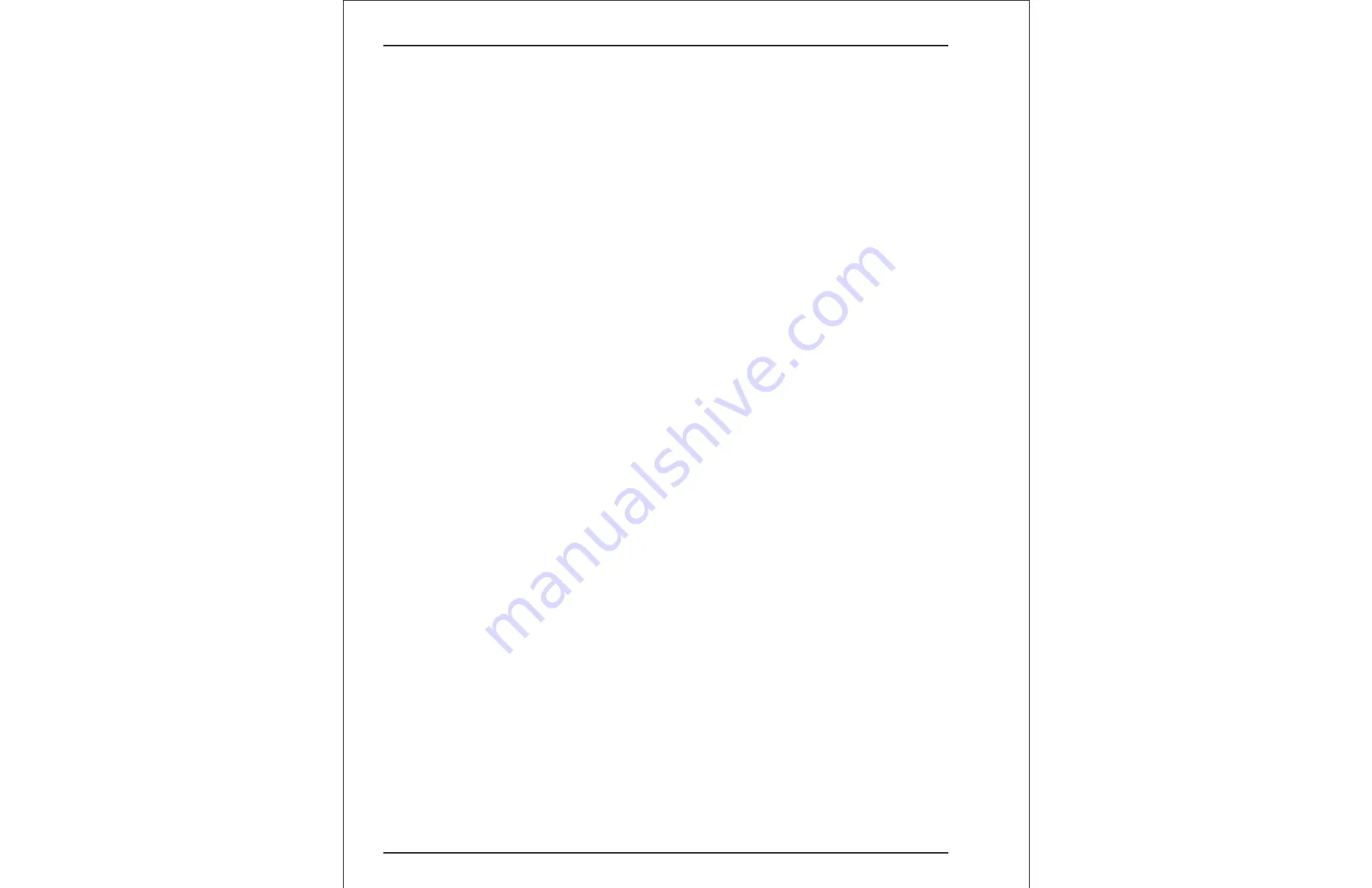
Service information
Boom/Axle Interlock System Inspection:
If following inspection of the unit revels the systems are
not functioning properly, DO NOT allow personnel to op-
erate the unit in an elevated position until the problem
has been located and corrected. DEATH or serious
INJURY of personnel may occur, if the unit should be-
come unstable and overturn.
Boom/axles Stowed Platform Interlock System:
The Boom/Axle interlock system is designed to prevent
raising or extending the boom unless axle is extended
and lock pin is in place and to prevent retracting the axle
unless the boom is in the stowed (travel) position (re-
tracted and down). The Boom/Axle interlock system is to
be checked as follows to confirm proper operation. If any
of the following tests are not successfully completed, the
malfunction MUST be corrected before putting the ma-
chine in service.
Limited lift and extend with axle retracted.
With axle retracted, boom down and retracted,
Boom/Axles switch on “BOOM”, Platform/Ground
switch in either position, raise boom and check for auto-
matic stop slightly above horizontal. Lower boom. Ex-
t e n d b o o m a n d c h e ck fo r a u t o m a t i c s t o p a t
approximately seven (7) feet of extension. Retract
boom.
Limited lift and extend with axle extended and not
pinned.
With axle extended, boom down and retracted,
Boom/Axles switch on “Boom”, Platform/Ground switch
is either position, and lock pin not in place, raise boom
and check for automatic stop slightly above horizontal.
Lower boom. Extend boom and check for automatic stop at
approximately seven (7) feet of extension. Retract boom.
Axle system inoperative with boom in working posi-
tion.
With axle extended and locked, Boom horizontal and ex-
tended approximately ten (10) feet, Boom/Axles switch
on “Axles”, Platform/Ground switch on “Ground”, check
that you cannot raise or retract axle.
Boom/Axles switch operation.
Axle and boom may be in any position. Platform/Ground
switch on “Ground”, check that when switch is set on
“Axles” the boom cannot be raised beyond horizontal or
extended beyond seven (7) feet and that no other boom
function operate. When the switch is set on “Boom” that
the axles system in inoperative (cannot lift or extend ax-
les).
Envelope Management System (
EMS
):
Use the following procedures to assure that the
EMS
system is operating properly prior to use of the unit by
operating personnel.
1. Disconnect primary boom angle transducer, pri-
mary
EMS
should error out. ONLY boom retract
should function until inside boom speed switch,
then ONLY boom lower should function.
2. Disconnect primary boom angle transducer, pri-
mary
EMS
should error out. ONLY boom retract
should function until inside boom speed switch,
then ONLY boom lower should function.
3. Disconnect primary boom angle transducer, pri-
mary
EMS
should error out. ONLY boom retract
should function until inside boom speed switch,
then ONLY boom lower should function.
4. Disconnect backup boom angle transducer,
backup
EMS
should error out then the primary
EMS
should error out. ONLY boom retract should
function until inside boom speed switch, then
ONLY boom lower should function.
5. Pull out three (3) feet of primary boom length trans-
ducer string, primary
EMS
should error out, boom
elevation and extension functions should not work.
6. With boom retracted and horizontal, open manual
bleed down valve. Primary
EMS
should error out,
boom elevation and extension functions should not
work.
7. Power up
EMS
and let unit sit for ten (10) to fifteen
(15) minutes without operating booms; Backup
EMS
should give five (5) quick beeps once every
minute.
8. Without depressing foot switch, hold Raise/Lower
or Extend/Retract controller full on; Boom should
not move and
EMS
should error out within thirty
(30) seconds.
If the
EMS
system is not operating properly, follow the
procedures outlined in the ENVELOPE MANAGEMENT
SYSTEM (
EMS
) CALIBRATION MANUAL for your unit
to recalibrate the system to proper working order.
Recalibration of your unit will require the following test
wire harnesses:
Part no. 0191024 – 2 way test harness
Part no. 0191025 – 3 way test harness
6
TB125
Summary of Contents for T125J
Page 50: ...REPAIR PARTS TB125J PARTS MANUAL SWING DRIVE SWING DRIVE Tue Mar 23 02 56 00 UTC 2021 2 11 ...
Page 85: ...REPAIR PARTS TB125J PARTS MANUAL AIR CLEANER AIR CLEANER Tue Mar 23 02 56 09 UTC 2021 2 26 ...
Page 90: ...TB125J PARTS MANUAL COWLING INSTALL COWLING INSTALL Tue Mar 23 02 56 12 UTC 2021 2 28 ...
Page 91: ...TB125J PARTS MANUAL COWLING INSTALL COWLING INSTALL Tue Mar 23 02 56 13 UTC 2021 2 28 ...
Page 96: ...TB125J PARTS MANUAL BOOM ASSEMBLY BOOM ASSEMBLY Tue Mar 23 02 56 16 UTC 2021 2 29 ...
Page 97: ...TB125J PARTS MANUAL BOOM ASSEMBLY BOOM ASSEMBLY Tue Mar 23 02 56 17 UTC 2021 2 29 ...
Page 98: ...TB125J PARTS MANUAL BOOM ASSEMBLY BOOM ASSEMBLY Tue Mar 23 02 56 18 UTC 2021 2 29 ...
Page 132: ...TB125J PARTS MANUAL PLACARDS AND DECALS PLACARDS AND DECALS Tue Mar 23 02 56 25 UTC 2021 2 39 ...
Page 161: ...HYDRAULICS TB125J PARTS MANUAL CAM VALVE CAM VALVE Tue Mar 23 02 56 30 UTC 2021 3 11 ...
Page 378: ......
Page 379: ......
Page 380: ......
Page 381: ......
Page 382: ......
Page 383: ......