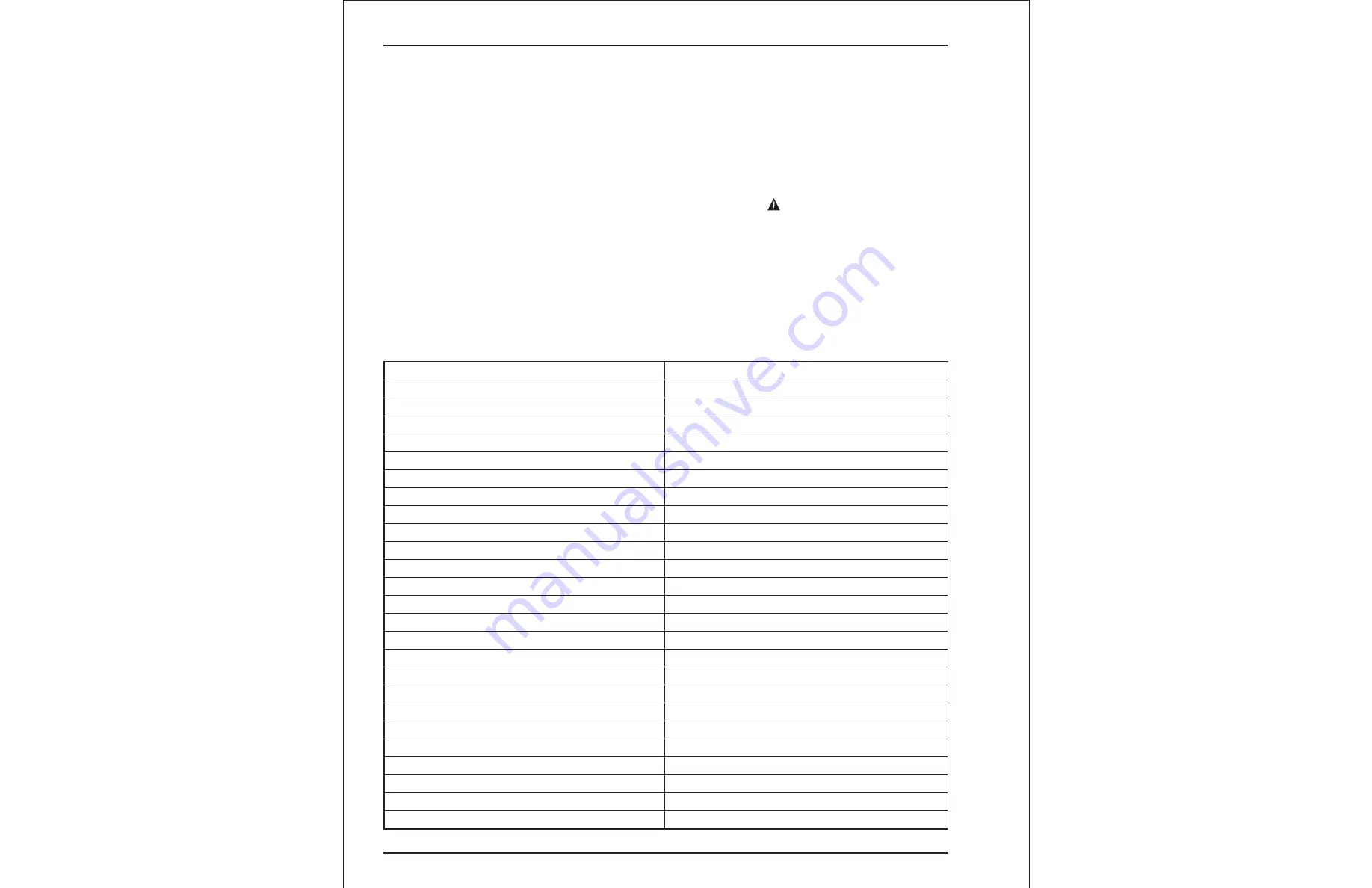
2
TB125
Maintenance schedules
Snorkel has established a Preventive Maintenance
Schedule that includes Daily Maintenance (Operator's
Inspection), 90 Day or 150 Hour (frequent) Maintenance
and Yearly or 500 Hour (annual) Maintenance, to detect
any defective, damaged or improperly secured parts
and provide information regarding lubrication and other
minor maintenance items.
The Maintenance Schedule following, outlines the re-
quirements of these maintenance checks for each time
interval. The Operator's Daily Maintenance and inspec-
tion must be performed by a trained operator. All other
maintenance and inspections must be performed by a
trained service technician only.
Note that the 90 Day or 150 hour (frequent) and yearly or
500 hour (annual) Maintenance, require use of the Pre-
ventive Inspection Maintenance Checklist to pinpoint all
inspection items. Retain a copy of these forms for your
records.
They also require that all placards and decals on the unit
are to be inspected.
All placards and decals must be in place and legible. Use
the placards installation drawing and parts listing in the
repair parts section 1 of this manual to check these plac-
ards and decals.
Snorkel recommends that you make additional copies of
the Preventive Inspection Maintenance Checklist forms
for your use in performing these inspections.
Failure to perform the Preventive Maintenance at
the intervals outlined in the Maintenance Schedule
may result in a unit being operated with a defect that
could result in INJURY or DEATH of the unit opera-
tor. Do not allow a unit to be operated that has been
found to be defective.
Repair all defects before returning the unit to service.
Daily maintenance
(operator’s inspection)
Components
Service Required
Axle/boom interlock
Check operation
Emergency power motor/pump
Check operation
Air filter
Check condition
Engine oil
Check oil level
Fuel leaks
Visually inspect (hoses, connections, etc.)
Fuel tank cap
Visually inspect (installation)
Engine coolant
Check fluid level
Engine fuel level
Check fuel gauge
Bolts and fasteners
Visually inspect (looseness)
Platform gate
Visually inspect (operation)
Slide pads
Visually inspect (boom wear marks)
Structural damage and welds
Visually inspect (weld cracks, dents)
Tires and wheels
Visually inspect (condition)
Battery fluid level
Check fluid level
Battery terminals
Visually inspect (corrosion)
Charging system
Visually inspect (belt, gauge)
Control switches
Visually inspect (operation)
Wiring harnesses
Visually inspect (installation, condition)
Hydraulic leaks
Visually inspect (hoses, tubes, fittings)
Hydraulic oil
Check fluid level
Slider power unit
Check operation
Platform rotator hydraulic power unit
Check fluid level and operation
Envelope management system
EMS
Check operation as outlined on page 6
Placards and decals
Visually inspect (installation, condition)
DANGER
Summary of Contents for T125J
Page 50: ...REPAIR PARTS TB125J PARTS MANUAL SWING DRIVE SWING DRIVE Tue Mar 23 02 56 00 UTC 2021 2 11 ...
Page 85: ...REPAIR PARTS TB125J PARTS MANUAL AIR CLEANER AIR CLEANER Tue Mar 23 02 56 09 UTC 2021 2 26 ...
Page 90: ...TB125J PARTS MANUAL COWLING INSTALL COWLING INSTALL Tue Mar 23 02 56 12 UTC 2021 2 28 ...
Page 91: ...TB125J PARTS MANUAL COWLING INSTALL COWLING INSTALL Tue Mar 23 02 56 13 UTC 2021 2 28 ...
Page 96: ...TB125J PARTS MANUAL BOOM ASSEMBLY BOOM ASSEMBLY Tue Mar 23 02 56 16 UTC 2021 2 29 ...
Page 97: ...TB125J PARTS MANUAL BOOM ASSEMBLY BOOM ASSEMBLY Tue Mar 23 02 56 17 UTC 2021 2 29 ...
Page 98: ...TB125J PARTS MANUAL BOOM ASSEMBLY BOOM ASSEMBLY Tue Mar 23 02 56 18 UTC 2021 2 29 ...
Page 132: ...TB125J PARTS MANUAL PLACARDS AND DECALS PLACARDS AND DECALS Tue Mar 23 02 56 25 UTC 2021 2 39 ...
Page 161: ...HYDRAULICS TB125J PARTS MANUAL CAM VALVE CAM VALVE Tue Mar 23 02 56 30 UTC 2021 3 11 ...
Page 378: ......
Page 379: ......
Page 380: ......
Page 381: ......
Page 382: ......
Page 383: ......