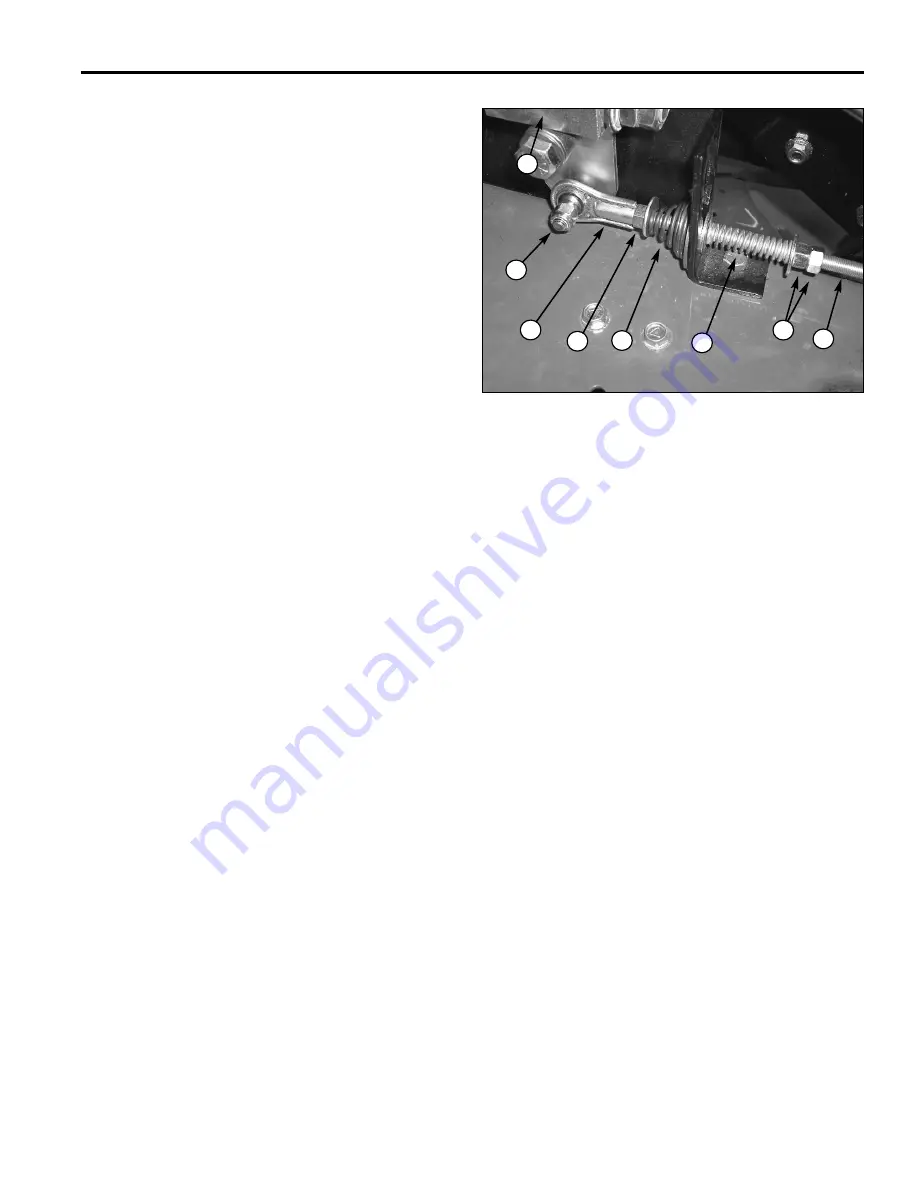
250 Z & Javelin Series
1/2006
13
TP 300-5148-00-HZ-SN
Figure 10. Neutral Adjustment (Right Side Shown)
A. Control Bracket Weldment
B. Rod End
C. Rod End Connecting Hardware
D. Jam Nut
E. Front Compression Spring
F. Rear Compression Spring
G. Spring Adjustment Nuts (2)
H. Link Rod
B
D
C
E
F
A
G
H
into its neutral locked position with little or no addi-
tional forward movement.
c. If additional rearward movement is required,
increase the length of the rear compression spring
set in step a by 1/16 - 1/8”. If additional forward
movement is required, decrease the length of the
rear compression spring by 1/16 - 1/8”. Recheck
operation. Repeat as needed.
NOTE: If equal amounts of forward and rearward
movement are required, do not adjust the spring.
d. Repeat steps a through c for left motion control
lever.
Neutral Adjustments
If the machine creeps while the motion control levers are
locked into their neutral locked positions, then it may be
necessary to adjust the link rods.
Perform this adjustment on a hard level surface such as
a concrete floor.
IMPORTANT NOTE: This adjustment should be per-
formed with the engine OFF. Perform the adjustment,
then start the engine to check the adjustment. If further
adjustment is required, stop the engine before perform-
ing the adjustment.
1. Determine which wheel is creeping. The left side
transmission and link rod control the left wheel, the
right link rod controls the right wheel.
2. Disengage the PTO, lock the motion control levers
into their neutral locked positions, turn the engine off,
remove the key, and wait for all moving parts to stop.
3. Remove the hardware (C, Figure 10) connecting the
rod end (B) to the control bracket weldment (A).
Note: The rod end is located under the fender beside
the operator seat.
4. Loosen the rod end jam nut (B).
If the transmission is creeping forward, turn the rod
end in (clockwise) one or two turns to shorten the link
rod (H).
If the transmission is creeping in reverse, turn the rod
end out (counterclockwise) one to two turns to length-
en the link rod.
5. Retighten the jam nut, and reconnect the rod end to
the control bracket weldment.
6. Start the unit and check for transmission creep.
Repeat steps 2-5 if necessary.
7. Once the correct adjustment is achieved, check oper-
ation of the neutral return system:
a. With the right motion control lever in its neutral
locked position, and the engine stopped, check the
length of the rear compression spring (F). The length
of the rear compression spring should initially be set
to 2”. Turn the two adjustment nuts (G) in or out until
the desired measurement is achieved.
b. With the engine stopped, move the lever from its
neutral locked position into neutral, then from neutral
into the forward position. Release the lever. The
lever should swiftly return to the neutral position and
be able to be moved out into its neutral locked posi-
tion with little or no additional rearward movement.
Now move the lever from neutral into the reverse
position and release. The lever should swiftly return
to the neutral position and be able to be moved out