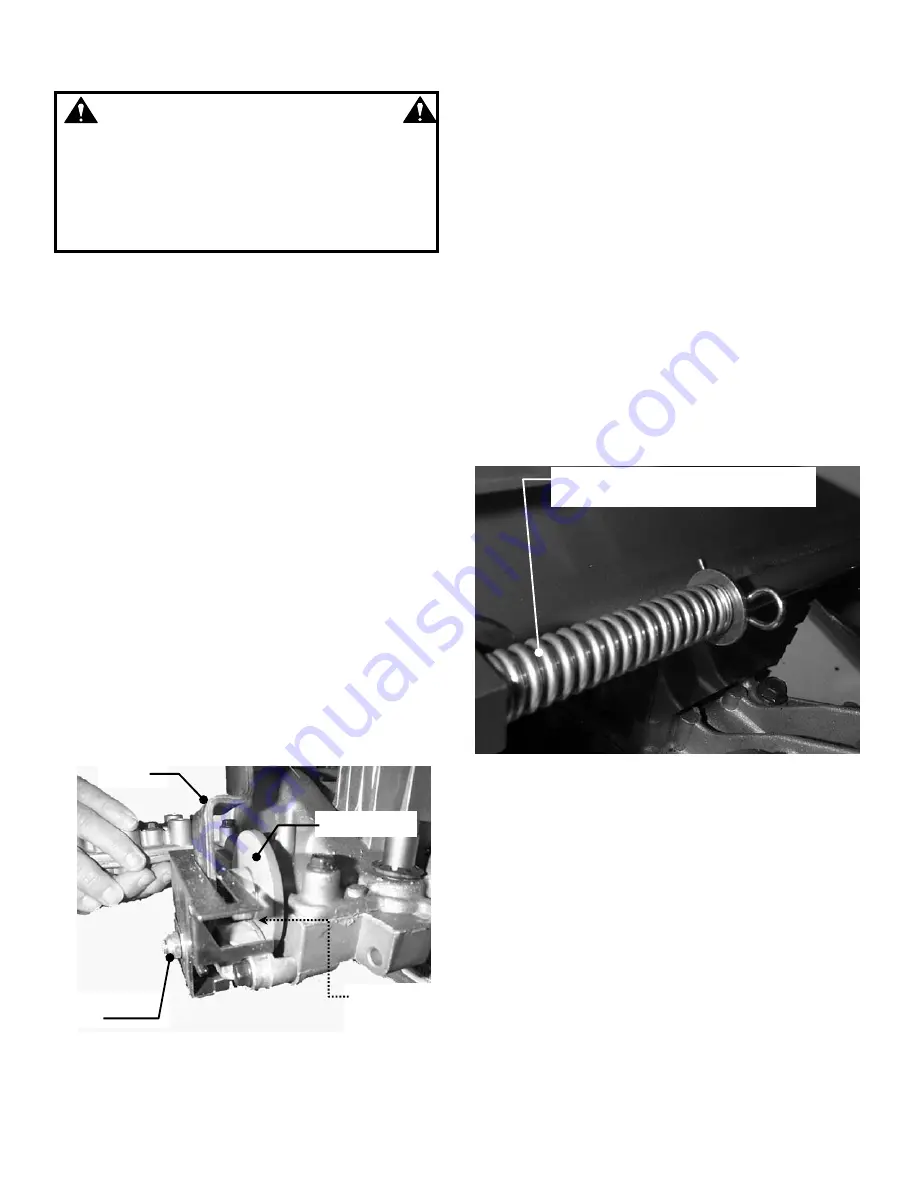
21
Section 4 - ADJUSTMENTS & REPAIR
WARNING
DO NOT attempt any adjustments, maintenance,
service or repairs with the engine running. STOP
engine. STOP blade. Engage parking brake. Remove
key. Remove spark plug wire from spark plug and
secure away from plug. Engine and components are
HOT. Avoid serious burns, allow all parts to cool
before working on machine.
4.6 MOWER DECK LEVEL ADJUSTMENT
If you are experiencing an uneven cut refer to
“TROUBLESHOOTING” section in this manual.
Before attempting any deck adjustments ADJUST
TIRE PRESSURE - 12 PSI FRONT & 12 PSI REAR
The mower blades should be level side to side
within 1/8” or less. Check level and adjust as
follows:
1. Park machine on flat surface. Stop engine. Stop
blades. Engage parking brake. Remove key.
2. Wearing heavy gloves, carefully grasp blades
and rotate until both are perpendicular to the
machine frame.
3. Check side to side level. Measure distance from
the blade tip to the ground. Record this for both
blades.
4. The two distances should not differ more than
1/8”. If difference is greater than 1/8”, adjustment
will be required.
5. Locate the threaded deck hanger rod on the
side of the deck that was measured to be low.
6. Remove hairpin from hanger rod. Rotate
CLOCKWISE one to two turns.
7. Recheck side to side level. If 1/8” or less
adjustment is complete. If still greater than 1/8”
adjust hanger rod as needed.
8. Reinstall hairpin into hanger rod.
FIGURE 4.11
4.7 SERVICE BRAKE / PARK BRAKE ADJUSTMENT
1. Park machine on flat surface. Stop engine. Stop
blades. Remove key.
NOTE: DO NOT engage parking brake.
2. Locate disc brake on left side of transmission.
Move brake arm fully forward in slot. See Figure 4.11.
3. Use a .020” thick feeler gage to adjust the
clearance between the brake pad and disc.
4. Insert the .020” feeler gage vertically up at the
bottom of the disc and between the disc and pad.
5. Tighten the brake adjustment nut until a light
drag is felt on feeler gage. Remove feeler gage.
6. Check disc. With brake released the disc
should be free to move.
7. Engage parking brake. Pedal effort should not
be excessive. Check brake rod spring. With brake
engaged there should be clearance between the
coils. See Figure 4.12.
8. Check brake function. Refer to Section
“CHECKING SERVICE BRAKE/PARK BRAKE”.
FIGURE 4.12
BRAKE DISC
BRAKE
ARM
ADJUSTMENT
NUT
INSERT FEELER
GAGE BETWEEN
DISC & PAD
BRAKE SPRING - CLEARANCE BETWEEN
COILS WITH PARK BRAKE ENGAGED.
Summary of Contents for 381451HBVE
Page 29: ...29 PRIMARY MAINTENANCE ...
Page 30: ...30 PRIMARY MAINTENANCE ...
Page 31: ...31 PRIMARY MAINTENANCE ...
Page 32: ...32 PRIMARY MAINTENANCE ...