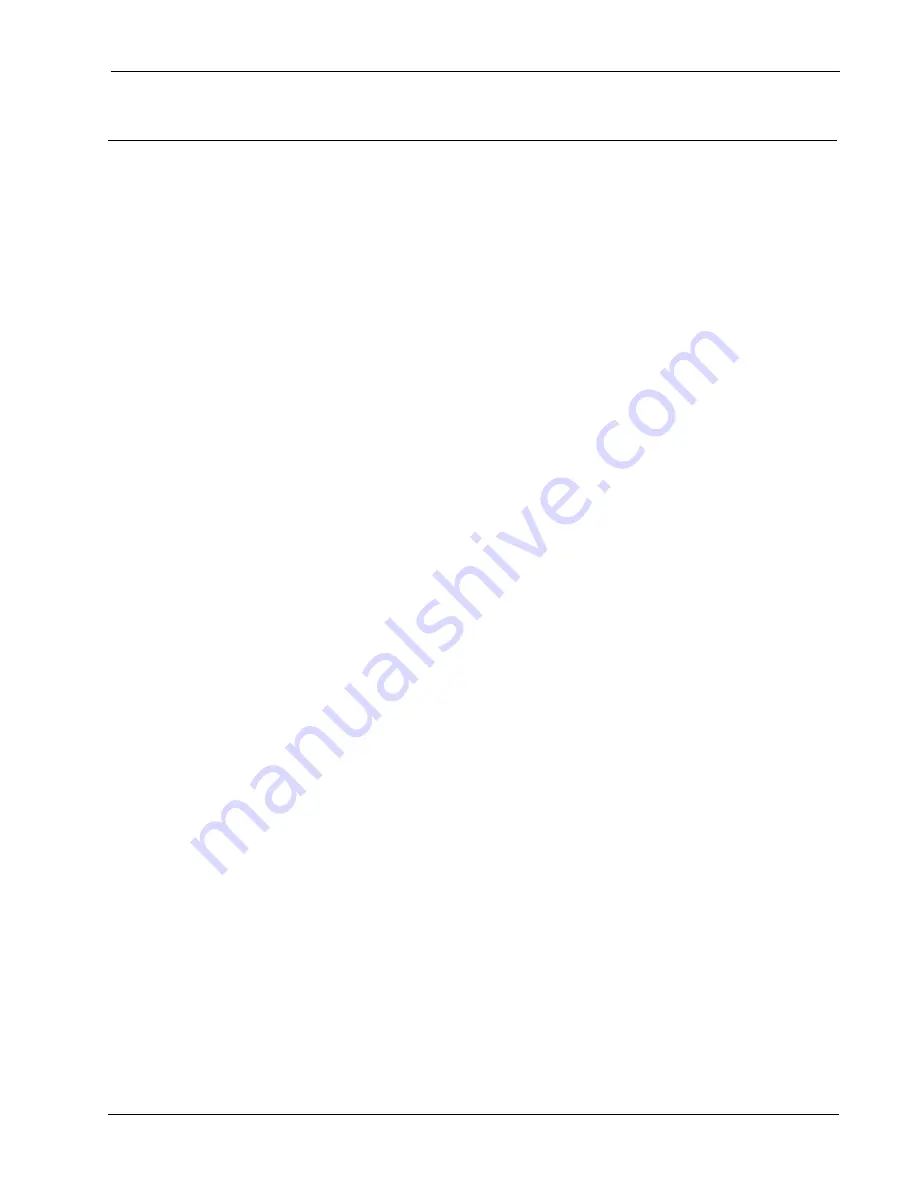
13
Theory of Operation
CHAPTER 2
THEORY OF OPERATION
GENERAL
The 3D Image Aligner is a revolutionary concept in performing wheel alignments. The system uses a camera
based machine vision technology that provides many benefits to the shop owner and alignment technicians.
It is the fastest, most accurate, and easiest to use aligner ever made. One of the benefits to new technolo
-
gies is the use of state-of-the-art components and computer programming that makes the task of servicing
this product easier than previous generations of alignment equipment. One of the most obvious differences is
the lack of an electronic measuring head, the source of many of the failures and inaccuracies on conventional
products. There is not much about this aligner that is conventional.
Shop owners and alignment technicians easily recognize the many strengths of this system compared to
conventional measuring-head systems. As the 3D Aligner was prepared for introduction into other Internation-
al markets such as Asia and Latin America, it became evident that the tasks of developing language transla-
tions and market-specific vehicle specification databases was overwhelming. The decision was made in 1998
to develop a Windows-based user interface for the 3D aligner in parallel with efforts to do the same for the
company’s conventional wheel alignment system. In the fall of 1998, the Windows environment was intro-
duced. The Windows compliant Pro32 software had a robust set of features, added the familiarity and power
of Windows, and had 27 different languages and 13 different specification databases. In addition, Windows
offered powerful networking capabilities that gained an importance as the automotive service industry discov-
ers the benefits of information sharing between the front point-of-sale counter and the back shop. In the fall of
2010 Pro42 was introduced. Pro42 added the versatility of added features plus it also opened up the area of
using a higher resolution camera system Ultra High Resolution(UHR). The UHR system also incorporates a
true 3D target. This target is much smaller and lighter.
CAMERAS
The “eyes” of the vision-based 3D Aligner are the two cameras mounted on either end of a camera beam.
The cameras are high-resolution CCD video type operating in gray-scale, similar to those used in security and
surveillance applications. The proprietary design lens is for this usage, and is permanently mounted to the
camera and triple-sealed for protection. The camera also has a band-pass filter, limiting the spectrum of light
that can enter the lens. With any camera there is an optical “field of view” that is a characteristic of the lens
design. Anyone who has used a camera knows that what you see is what you get no more, no less. The
cameras on the 3D Aligner are no different.
The field of view
(Figure 1 / 2)
is located along each side of the alignment rack and is a cone-shaped “tun-
nel” that expands in size as it moves further away from the cameras. The tunnel is approximately 2½ feet in
diameter near the front turntables. The centerlines of the tunnels are close to vehicle spindle height and about
18 inches outside of the outer wheel surface of an average car. In fact, the cameras are initially aimed at the
factory so that the targets, when mounted onto an average vehicle, would be located in the center of that tun-
nel. This insures that any vehicle placed on the rack in front of the 3D Aligner, from the widest to the narrow-
est, will have the targets mounted within the cameras’ field of view.
The Strobe Board contains 80 infared LED’s in an array to provide a source of bright light to reflect off the
targets when camera images are taken. These LED’s are rated for 100,000 hours continuous operation, and
up to 50% of the LED’s can fail without affecting the cameras ability to see the targets. These infared LED’s
are synchronized with the cameras so an image is “captured” every time the lights flash (roughly 2 times per
second).
Summary of Contents for UHR Ultra
Page 1: ...Service Manual Ultra UHR Ultra and V3400 WHEEL ALIGNER May 2014 ...
Page 13: ...11 AC DC POWER DISTRIBUTION ...
Page 14: ...12 AC DC POWER DISTRIBUTION ...
Page 16: ...14 Theory of Operation Figure 2 Top Field of View Figure1 Side Field of View ...
Page 19: ...17 Theory of Operation Configuration using single pole wheel clamp ...
Page 46: ...44 NOTES ...
Page 67: ...65 Diagnostics ...
Page 68: ...66 NOTES ...
Page 83: ......
Page 84: ...05 07 2014 2014 Impreso en U S A 309 Exchange Avenue Conway AR 72032 TEEWA546P4 Rev C ...