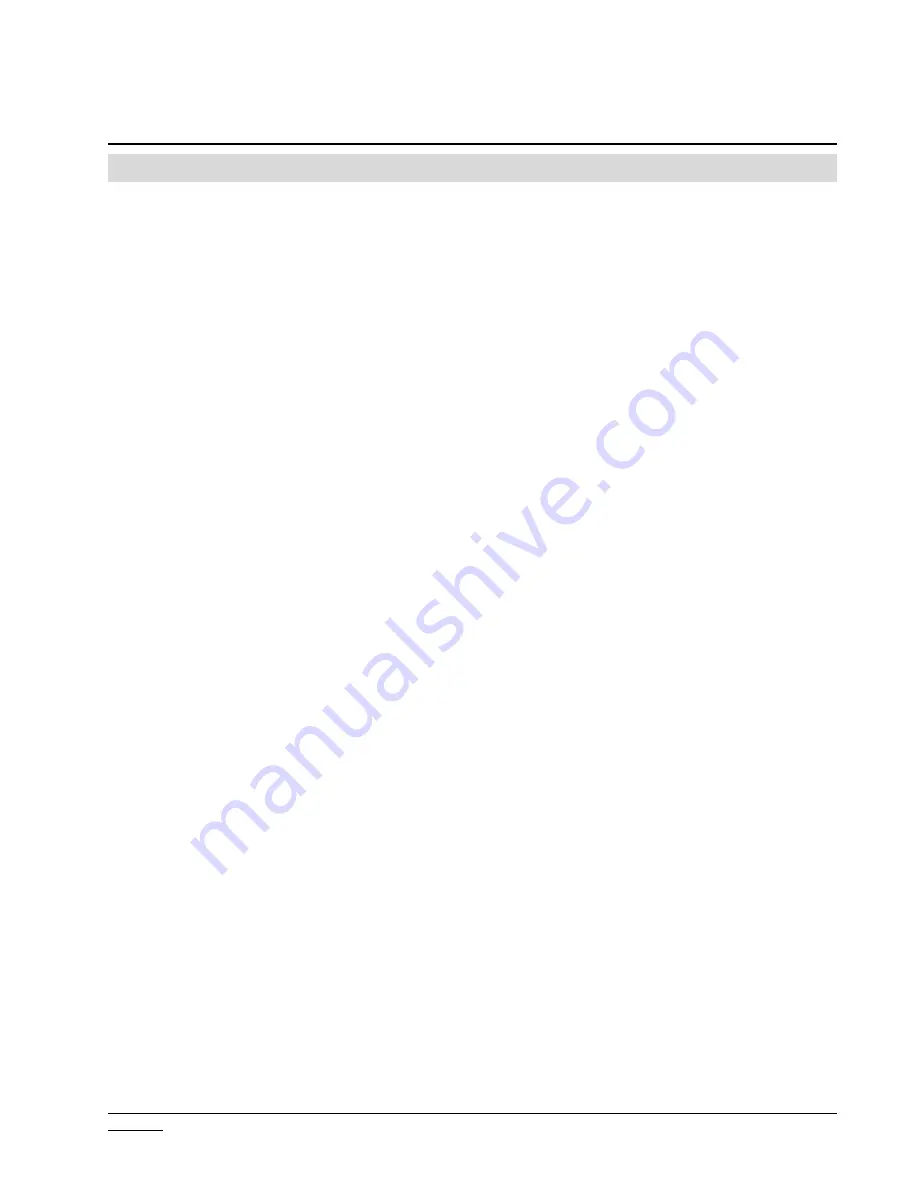
Page 2-1
Effective
09/2005
CHAPTER 2
THEORY OF OPERATION
FUNCTIONAL DESCRIPTION
The EEWB314A wheel balancer is designed to compute static and dynamic imbalance of car, light truck,
motorcycle and truck wheels.
Wheels are attached to the shaft using precision centering adapters and retainers. The shaft rotates on
precision bearings on the shaft support. The rotating shaft is perfectly balanced. The wheels attached
normally represent an imbalance, which creates centrifugal force and a dynamic momentum as it is spun on
the balancer shaft. The wheel is spun by hand.
The centrifugal force and dynamic momentum created by the imbalance are detected by 2 transducers located
between the shaft support and the machine frame. These transducers contain small discs of special quartz
which generate millivolts of electric current when compressed. The current created is linearly proportional to
the compression force.
Centrifugal force and momentum vectors are generated by a rotating wheel imbalance. This causes a signal
to be generated by the transducers (which pick up only the vertical component of the constrained forces) in
the form of a periodic sine wave.
This signal is not perfectly sinusoidal, due to periodic noises from shaft bearings, support frame vibration,
gyroscopic effect, etc., which are added to the signal generated by the imbalance of the wheel. Because of
these extraneous noises, the signal produced must be filtered to compute actual imbalance.
To find wheel imbalance, knowledge of signal magnitude and timing are both required. Timing is determined
by the encoder, which consists of a electronic pcb connected to the tube of the shaft. A series of timing marks
are on the shaft which trigger light being transmitted between two optocouplers, thus generating a DC Square
wave each time a mark moves past an optocoupler. One additional mark offset from the encoders’ metallic
strip, interrupts the third optocoupler on the board, and creates a zero-signal reset or home position. The
encoder detects 512 angular positions during each turn of the shaft, plus the home or reset position. The
frequency of the DC square wave generated by the encoder allows the balancer to compute wheel speed,
wheel acceleration and weight location. The encoder and transducer signals are processed together by the
CPU to give weight amount and location readings.
The CPU board gathers the information generated from the encoder and transducer via ribbon cable. This
board is powered with 9 VAC received from the transformer.
To compute correct imbalance values, the parameters (diameter, width, and offset) of the wheel to be bal-
anced must be entered. Enter wheel parameters using the Distance Entry Arm. Slide the gauge to touch the
rim and hold. The distance to the rim will be entered automatically. Measure the rim width with the rim width
calipers (supplied) and enter the measured value. This is done by manually turning the left hand knob on the
display panel. The rim diameter is measured by turning the right hand knob on the display panel until the
desired number is shown.
Calculated imbalance values are then shown on the LED display panel after a spin cycle.