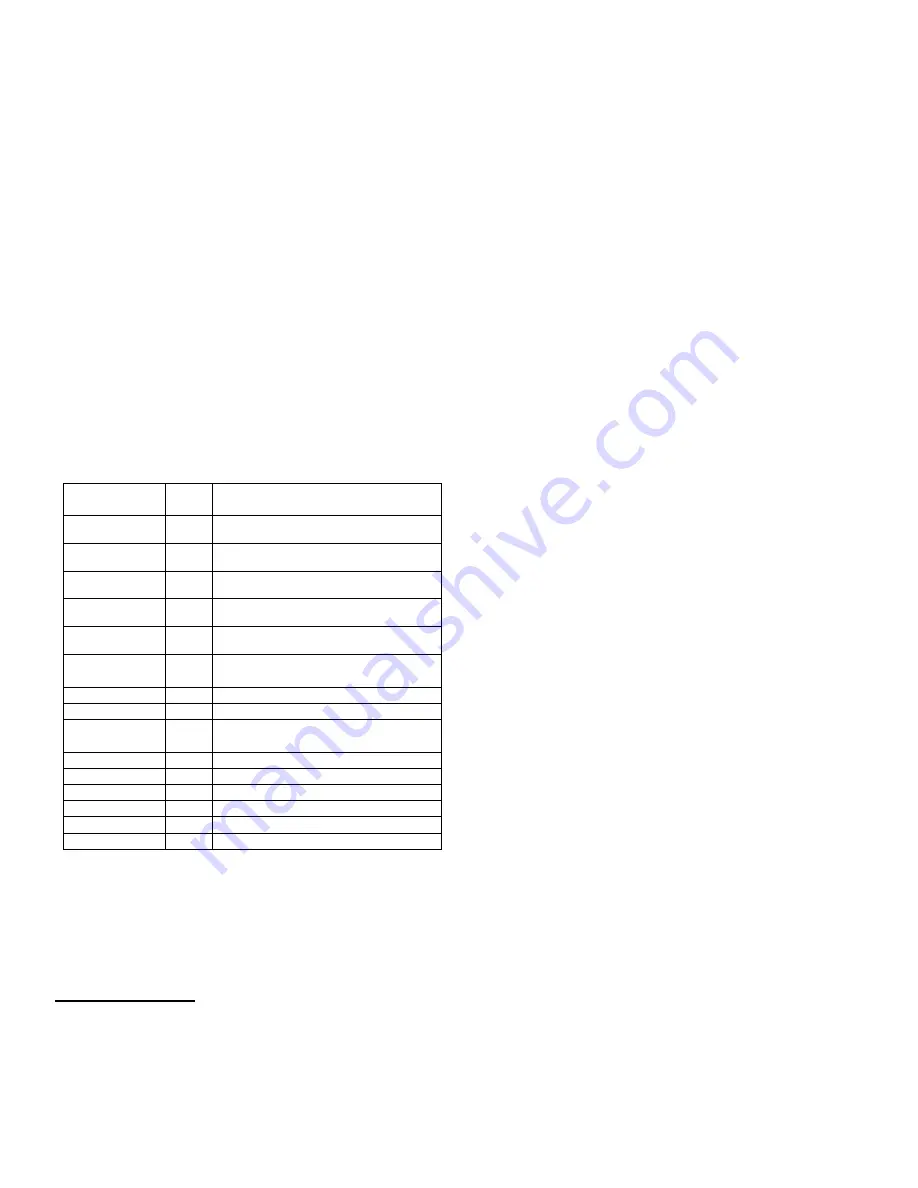
20K 2-Post Lift
Installation, Operation and Maintenance
Page 4
Rev. 11/10/2021
EAZ0080V85A
R
ECEIVING
The shipment should be thoroughly inspected as soon
as it is received. The signed bill of lading is
acknowledgement by the carrier of receipt in good
condition of shipment covered by our invoice.
If any of the goods called for on this bill of lading are
shorted or damaged, do not accept them until the
carrier makes a notation on the freight bill of the
shorted or damaged goods. Do this for your own
protection.
NOTIFY
Snap-on Equipment
AT ONCE if any
hidden loss or damage is discovered after receipt.
IT IS DIFFICULT TO COLLECT FOR LOSS OR
DAMAGE AFTER YOU HAVE GIVEN THE CARRIER
A CLEAR RECEIPT.
File your claim with
Snap-on Equipment
promptly.
Support your claim with copies of the bill of lading,
freight bill, and photographs, if available.
Component Packing List
PART #
QTY/
LIFT
DESCRIPTION
12320-P
1
P
OWER
C
OLUMN
A
SSAY
12320-
!
1
I
DLER
C
OLUMN
A
SS
’
Y
12300
1
O
VERHEAD
P
ACK
CL20-HW
1
H
ARDWARE
B
OX
12006
1
A
RM
P
ACK
12311-0
2
C
OLUMN
E
XT
.
A
SSY
(14’-6”
O.A.
H
T
.)
12311-2
C
OLUMN
E
XT
.
A
SSY
(16’-6”
O.A.
H
T
.)
12074
1
O
VERHEAD
S
HUTOFF
B
AR
A
SS
’
Y
B2064-01
1
O
VERHEAD LIMIT
S
WITCH
12302-0
2
S
YNC
.
C
ABLE
P
ACK
(14’-6”)
12302-2
S
YNC
.
C
ABLE
P
ACK
(16’-6”)
B12069
4
A
DAPTER
E
XTENSION
(4”)
B12068
2
A
DAPTER
E
XTENSION
(8”)
12091
2
A
DAPTER
R
ACK
12093
4
A
RM
R
ESTRAINT
A
SSEMBLY
AB-93178
1
P
OWER
U
NIT
–
S
INGLE
P
HASE
CL16-IOM
1
L
ITERATURE
P
ACK
A
CCEPTED
O
ILS
–
Do not use oils with detergents
Hydraulic fluid is not provided with the lift shipment
-10
wt.
anti-foam, anti-rust hydraulic / biodegradable oil
-Dexron III ATF
I
NSTALLATION
S
AFETY
R
EQUIREMENTS FOR
I
NSTALLATION AND
S
ERVICE
Refer to ANSI/ALI ALIS (current edition)
I
MPORTANT
:
Always wear safety glasses while installing lift.
T
OOLS
(
MINIMUM REQUIRED
)
a. Tape measure, 16ft
b. Chalk line
c. 4ft level
d. 10” adjustable wrench
e. Standard open end wrenches 7/16”, 1/2",
(2) 9/16”, (2) 11/16”, 3/4"
f. 5/16” Hex wrench FF
g. Needle nose pliers
h. Hammer drill with 3/4” diameter carbide tipped
bits
i. 2 lb. hammer
j. Torque wrench: 150 foot pounds minimum with 1
1/8” socket
k. 12
ft.
Step
ladder
l. Anti-Seize lubricant (for arm pins and foot pad
screw threads and stop rings)
L
AYOUT
Note:
•
This lift can be installed at three different heights
and three different widths. The Cable adjustment
for the Height variation will be accommodated by
the Lower Sheave Bracket. The Cable
adjustment for the Width variation will be
accommodated by the take-up tube in later
steps.
•
The height and width must be established before
beginning, as this will determine the lower
sheave position and cable take up tubes to be
used.
1) Once the lift location has been established,
ensure that the vertical clearance and flooring
requirements have been met per page 3.
2) See
Fig 1
for the lift layout. Determine which side
of the bay that the power unit will be on and
identify the column assembly with the power unit
bracket. Layout the service bay according to the
architect’s plans or owner’s instructions
(see Fig.
1b
).
Failure to install in this orientation can
result in personal and property damage.
Be
certain that the proper conditions exist, see pg. 3.
L
IFT
P
REPARATION
3) With column assemblies lying flat, remove cable
and hose rolls from inside the column.
4) Manually push carriages up enough to unhook the
cylinder hose from the base plate tabs. Proceed
with pushing the cylinder and carriage up enough
to access all three sheave locations on the
sheave bracket, see
Fig 2
.