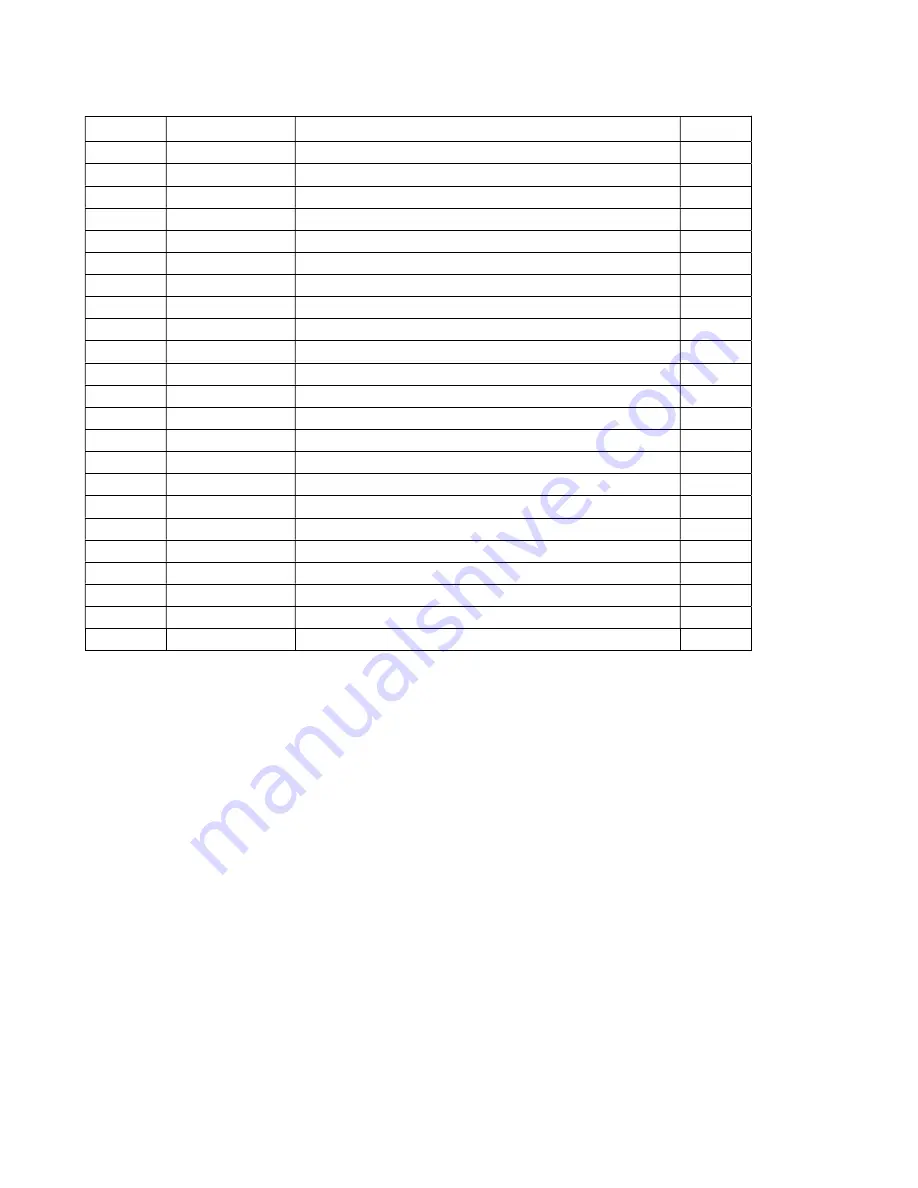
65
of
84
TURNPLATE ASSEMBLY: PARTS LIST
Item#
P/N#
Description
Qty
1
EAM0047J60A TOP - TT, MACH.
1
2
6-3954
SCREW GB/T 70.3-2008 M5X10
3
3
EAC0105J18A SEPARATOR-SCREW,TT
3
4
1-19388A
FHCS,#10-32 UNF X 3/4,STAINLESS STEEL
6
5
1-3719
TURN TABLE,LOCKING LABEL-
1
6
EAM0113V40A LOCKING MECHANISM CENTERING RING
1
7
EAM0113V41A LOCKING MECHANISMSTUB SHAFT
1
8
EAM0113V42A LOCKING MECHANISM CYLINDER STAND-OFF
4
9
EAM0047J52A PAD - TT
2
10
1-19488A
HEX SCREWGB/T 70.1-2008 M5X115
4
11
6-3955
PHIL SCREW - M6 X 16mm
10
12
EAH0069V01A LOCKING CYLINDER ASSEMBLY
1
13
EAM0113V43A LOCKING MECHANISM CENTERING CONE
1
14
EAA0441V53A FRONT LED LIGHT ASSY
1
15
2-2931
TT BASE MACH,LOCKS & LIGHT
1
16
EAA0361J20A PLATE ASM.-BOTTOM,TT
1
17
1-26603A
SCREW-FHSC,M5X10mm FHMS,PHIL
3
18
EAA0333J59A BALL PLATE ASM.
1
19
EAM0047J57A WEAR PLATE-TOP
1
20
6-3956
SCREW GB/T 70.3-2008 M14X30
1
21
1-0326A
M4X8 SCREW
2
22
1-3347
WASHER
2
23
EAM0113V94A BACK PLATE
2
Note: Please contact customer service for items not listed.
Summary of Contents for EELR587A
Page 7: ...7 of 84 3 0 SAFETY WARNING DECALS...
Page 18: ...18 of 84 Figure 8 Hydraulic Connections...
Page 22: ...22 of 84 TO LEFT DECK ASSEMBLY Figure 11 Air Safety Auxiliary Air Connections...
Page 26: ...26 of 84 Figure 15b Optional LED Driver Box Circuit Connections...
Page 35: ...35 of 84 Figure 28 Filler Angle Installation...
Page 64: ...64 of 84 20 0 ACCESSORY ASSEMBLY 20 1 Front Turnplate...
Page 67: ...67 of 84 20 3 Airline Routing for Locking Turnplates and Rear Slip Plates...
Page 79: ...79 of 84 22 0 POWERPACK ASSEMBLY 22 1 Powerpack Assembly EAA0441V72A...