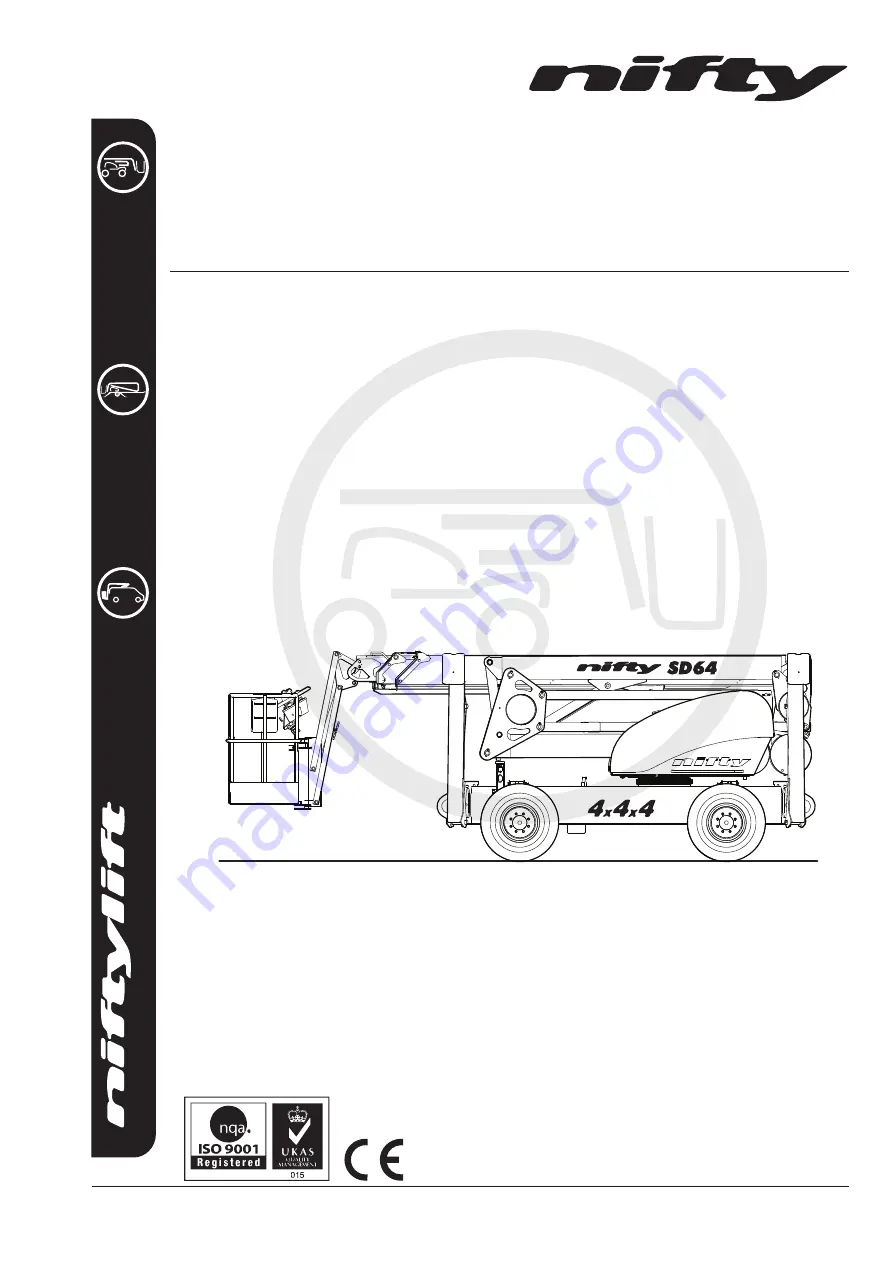
in
fo
@
n
if
ty
li
ft
.c
o
m
.com
SD64
Operating & Safety Instructions
MODEL SD64 SERIES
SCALE
1.000
M50407/0
4
Niftylift Limited
www.niftylift.com
e-mail: [email protected]
Tel: 864-968-8881
Fax: 864-968-8836
1525 S. Buncombe Road
Greer
SC 29651
USA
Summary of Contents for SD64 4x4x4
Page 2: ......
Page 21: ...SD64 Series Operating Safety Instructions USA 04 16 Issue 04 19...
Page 48: ......