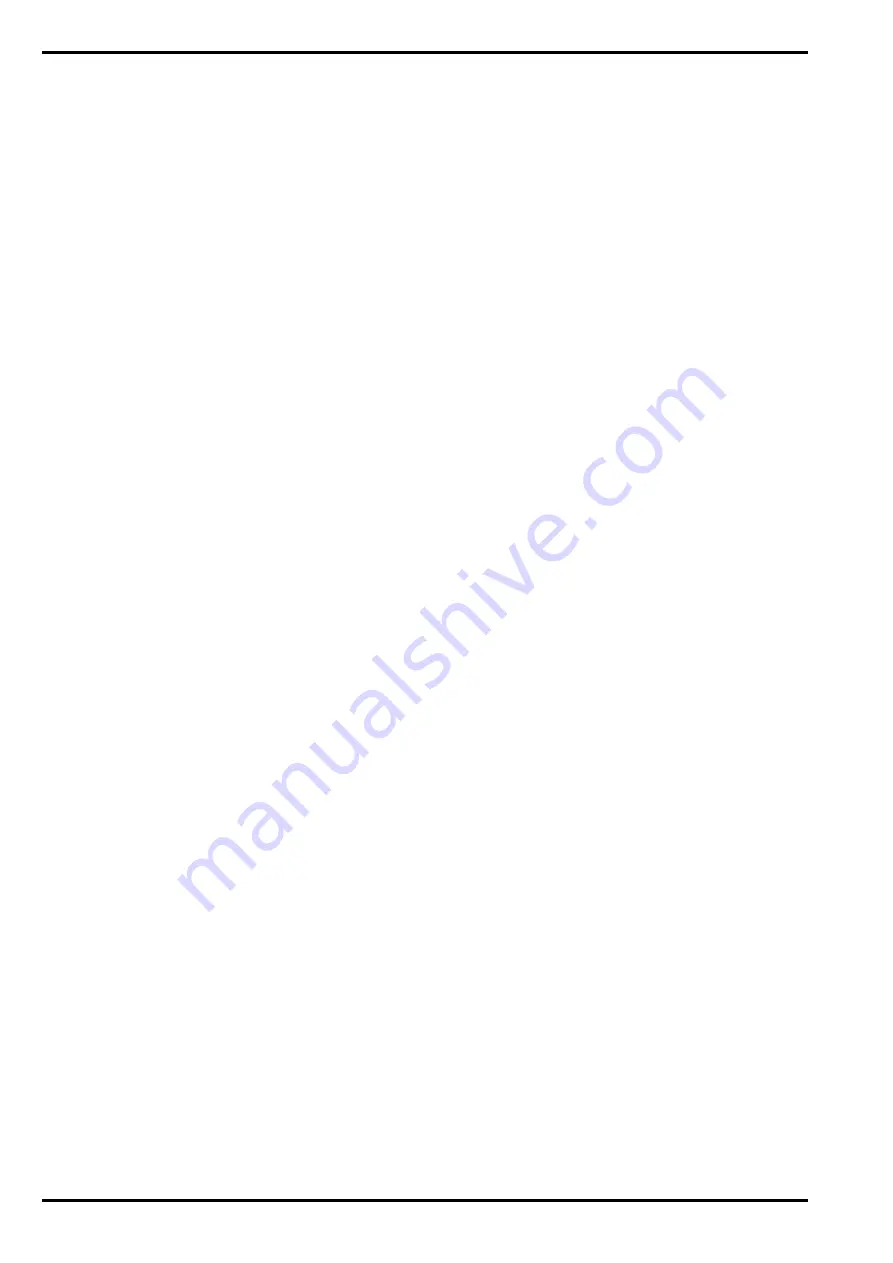
ZINGO DU X-002
Appendix C Page 54
NOTE:
This is a minimum guide only.
3.3
ESTABLISH DATUM LEVEL
i)
If a rubber tiled Impact Absorbing surface is to be laid, see separate instructions (base may incorporate up to
2% falls etc).
ii)
If equipment is to sit in loose fill or wet pour rubber surfaces allowances will need to be made for its
recommended thickness. Generally it is recommended that loose fill surfaces are installed to a minimum
depth of 300mm, however, with certain loose fill materials a greater depth may be required. This will need to
be determined by allowing 100mm for the dispersal in addition to the thickness required for the particular Free
Fall Height. The foundation illustrated will allow for a thickness up to 300mm.
PRE-INSTALLATION INSPECTION
Inspect all parts for damage (that may have occurred during transportation & storage). Finish Coatings, if found to be
damaged these should be made good before erection (Refer to maintenance instructions). Any damaged or missing
parts must be replaced.
4
INSTALLATION & ASSEMBLY PROCEDURES
4.1
ASSEMBLY METHOD OF CLAMPS TO POSTS
1)
CLAMP RING (half) WITH LOCATION SCREW
(See detail X & Y)
i)
Position Clamp Ring (half) (item 46) on to leg with fixing hole aligned with appropriate M6 insert.
ii)
Place 1/4” Screw Insulator (item 64) into hole and then screw the Resistorx bolt M6 x 25 (item 54) into M6
insert to retain and locate the Clamp Ring (half). (Do not over tighten).
iii)
Position the other Clamp Ring (half) (item 46) and assemble to leg using 2 off 1/4” x 1-1/4” BHCS fixings
(item 65). Fully tighten bolts to a maximum torque setting of 20Nm. Into the unused fixing hole insert 1 off
white plastic plug (item 71)
2)
CLAMP RING (half) WITHOUT LOCATION SCREW
(See detail Z)
i)
Position 2 off Clamp Ring (half) (item 46) at stated height on post and secure using 2 off 1/4” x 1-1/4”
BHCS fixings (item 65). Fully tighten bolts to a maximum torque setting of 20Nm. Into the unused fixing
holes insert 1 off white plastic plug (item 71)
3)
TOP & BOTTOM SOCKETS TO CLAMP RING (half)
i)
Hook over the Clamp Ring (half) both the Top (item 48) & Bottom (item 47) Bar Sockets to grip the fixing
rail of the appropriate unit.
ii)
Align the tapped hole in the Bar Socket Top (item 48) with the hole in the top of the unit fixing rail and
secure the sockets together using the 1/4” x 5/8” BHCS fixings (item 66).
iii)
Tighten the BHCS fixings up equally to ensure that the Top (item 48) & Bottom (item 47) Bar Sockets pull
up square and grip the unit fixing rail evenly.
iv)
When the unit fixing rail is in the correct position with the legs square and plumb tighten fastenings to a
maximum torque setting of 20Nm.
v)
Once clamp is fully tightened lock each Bar Socket Top to unit fixing rail by screwing into the tapped hole
a 3/8” x 3/8” Set Screw (item 67) for Bar Socket Top (item 48).
4.2
MAIN ASSEMBLY METHOD
1)
Refer to site layout for position and orientation of product, then mark the outline of the position of the footings
with e.g. spray or chalk etc. Excavate the holes. See
Pages 5-8
depending on type of unit to be installed.
2)
Assemble to 1 off Curved Leg - 1200 deck (item 1), 2 off Clamp Rings (half) (item 46) and 1 off Deck Support
Casting (item 45) at the pre-inserted hole position for the 1200 high deck.
STEP 1
(Detail Y)
i)
For assembly method see Note 4.1, 1), i) to iii) ensuring that the Deck Support Casting (item 45) is
slotted over one of the Clamp Ring (half) before assembling the second Clamp Ring (half).
3)
Assemble to 1 off Curved Leg - 1200 deck (item 1) and 2 off Clamp Rings (half) (item 46) at the pre-inserted
hole position for the top clamp rail.
STEP 1 (
Detail X)
i)
For assembly method see Note 4.1, 1), i) to iii).
ISSUE L 15-11-2010
Summary of Contents for ZINGO DU X-002/P
Page 2: ...ZINGO DU X 002 Page 2 ISSUE L 15 11 2010...
Page 23: ...ZINGO DU X 002 Page 23 STEP 5 STEP 3 ISSUE L 15 11 2010...
Page 24: ...ZINGO DU X 002 Page 24 STEP 6 5 30 60 STEP 1 STEP 3 STEP 2 62 63 x 3 ISSUE L 15 11 2010...
Page 26: ...ZINGO DU X 002 Page 26 STEP 9 10 51 58 67 48 10 66 47 20Nm ISSUE L 15 11 2010...
Page 27: ...ZINGO DU X 002 Page 27 STEP 10 5 62 63 5 x 2 ISSUE L 15 11 2010...
Page 28: ...ZINGO DU X 002 Page 28 STEP 11 60 5 0 5 STEP 3 62 63 ISSUE L 15 11 2010...
Page 32: ...ZINGO DU X 002 Page 32 300 9 STEP 18 67 48 66 47 0 0 20Nm y73 ISSUE L 15 11 2010...
Page 35: ...ZINGO DU X 002 Page 35 STEP 22 5 8 STEP 23 49 36 4 x 10 ISSUE L 15 11 2010...
Page 36: ...ZINGO DU X 002 Page 36 STEP 24 52 58 27 25 58 52 STEP 25 ISSUE L 15 11 2010...
Page 39: ...ZINGO DU X 002 Page 39 STEP 30 37 38 59 51 41 41 49 49 ISSUE L 15 11 2010...
Page 40: ...ZINGO DU X 002 Page 40 STEP 31 3 70 43 50 44 69 68 42 58 70 ISSUE L 15 11 2010...
Page 44: ...ZINGO DU X 002 Appendix A Page 44 ISSUE L 15 11 2010...
Page 48: ...ZINGO DU X 002 Appendix B Page 48 ISSUE L 15 11 2010...