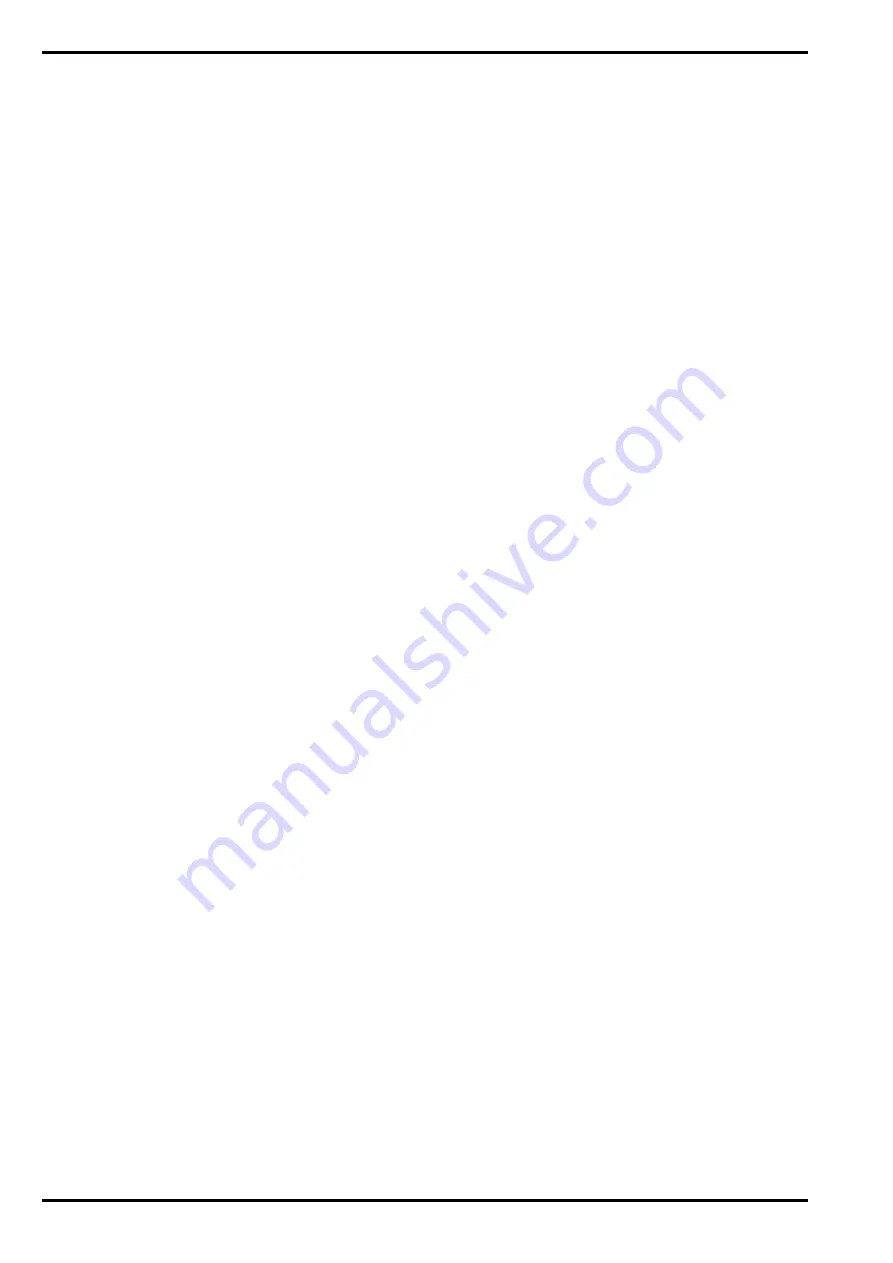
PILLARS OF HERCULES EC221
Appendix A Page 16
3.2
MARK OUT HOLES
Consult SMP layout drawing for structure position on site.
See
page 4 & 5
for concrete foundation sizes.
NOTE:
This is a minimum guide only.
3.3
ESTABLISH DATUM LEVEL
i)
If a rubber tiled Impact Absorbing surface is to be laid, see separate instructions (base may incorporate up to
2% falls etc).
ii)
If equipment is to sit in loose fill or wet pour rubber surfaces allowances will need to be made for its
recommended thickness. Generally it is recommended that loose fill surfaces are installed to a depth of
300mm, however, with certain loose fill materials an alternative depth may be required. This will need to be
determined by allowing 100mm for the dispersal in addition to the thickness required for the particular Free
Fall Height. The foundation illustrated will allow for a thickness up to 300mm.
PRE-INSTALLATION INSPECTION
Inspect all parts for damage (that may have occurred during transportation & storage). Finish Coatings, if found to be
damaged these should be made good before erection (Refer to maintenance instructions). Any damaged or missing
parts must be replaced.
4
INSTALLATION & ASSY PROCEDURES
i)
Refer to site layout for position and orientation of product, then, mark the outline of the position of the footings
with e.g. spray or chalk etc. Excavate the holes.
(SEE PAGE 4/5)
.
ii)
Fit 1 off BTN 135 Bolt (item 4) to each Upright Post (item 1 - LTB11), secure using 1 off M16 Washer (item 11)
and M16 Nyloc Nut (item 12). Check counterbores and holes are clear, ensure BTN Bolts are located in the
shallow counterbore on inside of posts. Ensure slots of the BTN Bolts are inline vertically as shown (rope must
pivot vertically only) and the pins are pulled into the grain of the timber when tightened.
(SEE STEP 1).
iii)
Place Upright Posts (item 1 - LTB11) into designated excavations, ensure BTN Bolts (item 4) on both posts
are facing inward. Brace in position and ensure all the posts are level, plumb and spaced to correct
dimensions, this is critical for correct tension of the rope.
(SEE PAGES 4 & 5, STEP 1)
iv)
Place 2 Bollard Fixing Posts (item 7) into designated excavations, brace in position taking notice of surface
type and requirements. For Type 1/2 attach Bollard Fixing Posts (item 7) to Extension Posts (item 8) using 8
off M10 X 40 Hex. Bolt (item 9) and M10 Nut (item 10).
(SEE PAGES 4 OR 5 & STEP 2A OR 2B).
v)
Verify rope fits - remove before concreting.
(STEP 3).
vi)
Fill the holes with concrete to the required level, taking into account any Impact Absorbing Surfacing
requirements. Ensure that the full volume of concrete is used. The top of the concrete should gradually (1:100)
slope down & outwards locally from the equipment upstand to the required level to form a watershed.
Concrete mix is recommended at:
1 part cement;
2 parts sand;
4 parts aggregate;
by volume with 20mm aggregate
(20 N/mm
2
min compressive strength)
vii) Keep installation off limits to the public until the concrete has completely cured. (Recommended initial curing
time is 48 hours).
(STEP 3).
viii) If installation is with a loose fill type (type 1/2) surface, the upright posts should be marked with ‘Basic level
mark’ to indicate the recommended finished surface level.
(SEE PAGE 4).
ix)
Remove any installation aids before fitting rope. Fit one end of Rope (item 2) to one of the BTN 135 Bolts (item
4) located at the top of an Upright post (item 1- LTB11), ensuring the rope is the correct way up, secure using
1 off Pivot Bar (item 5) and M5 X 25 Grub Screw (item 6), utilise 2.5mm AF Allen Key ensuring grub screw
goes fully into hole of pivot bar to full depth of BTN fitting. Fully tighten, allowing the rope to hang freely.
(SEE
STEP 4).
ISSUE C 12-03-2012