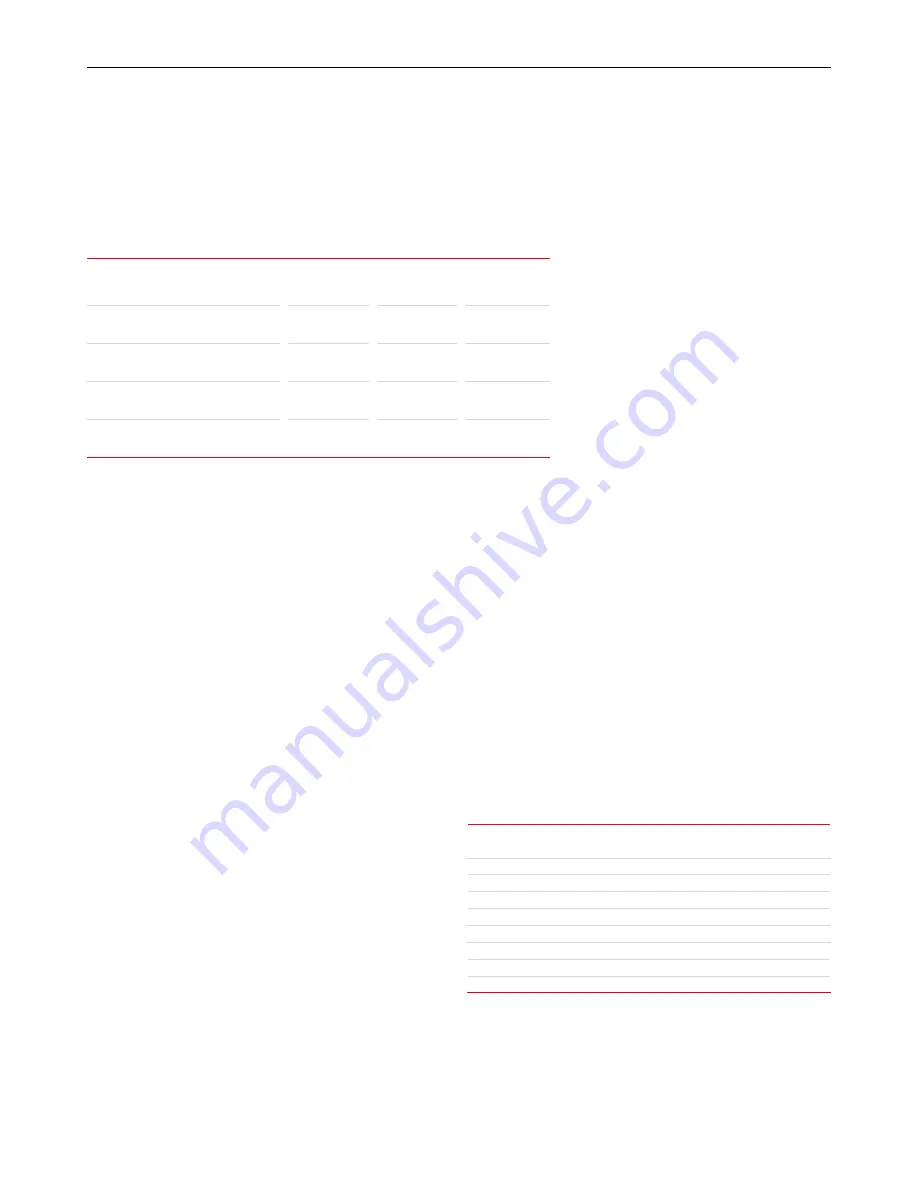
13
BOC Smootharc 180 Multiprocess operating manual
Typical Metal Transfer Mode
Process
Dip
Transfer
Globular
Transfer
Spray Transfer
Metal Inert Gas (MIG)
Metal Active Gas (MAG)
�
�
�
Flux Cored (Gas Shielded)
�
�
�
*
Flux Cored (Self Shielded)
�
�
�
Metal Cored
�
�
�
* Not True Spray
Pulsed Transfer
Pulsed arc welding is a controlled method of spray transfer, using
currents lower than those possible with the spray transfer technique,
thereby extending the applications of MIG/MAG welding into the range
of material thickness where dip transfer is not entirely suitable. The
pulsed arc equipment effectively combines two power sources into one
integrated unit. One side of the power source supplies a background
current which keeps the tip of the wire molten. The other side produces
pulses of a higher current that detach and accelerate the droplets of
metal into the weld pool. The transfer frequency of these droplets is
regulated primarily by the relationship between the two currents. Pulsed
arc welding occurs between ±50-220A, 23–35 arc volts and only with
argon and argon-based gases. It enables welding to be carried out in all
positions.
2.5 Fundamentals of MIG/MAG, FCAW and MCAW
Welding Technique
Successful welding depends on the following factors:
1
Selection of correct consumables
2
Selection of the correct power source
3
Selection of the correct polarity on the power source
4
Selection of the correct shielding gas
5
Selection of the correct application techniques
a
Correct angle of electrode to work
b
Correct electrical stickout
c
Correct travel speed
6
Selection of the welding preparation
Selection of Correct Consumable
Chemical composition
As a general rule the selection of a wire is straightforward, in that it
is only a matter of selecting an electrode of similar composition to
the parent material. It will be found, however, that there are certain
applications that electrodes will be selected on the basis of its
mechanical properties or level of residual hydrogen in the weldmetal.
Solid MIG/MAG wires are all considered to be of the 'low Hydrogen type'
consumables.
The following table gives a general overview of the selection of some of
the BOC range of MIG/MAG wires for the most common materials.
Common Materials Welded with BOC MIG Wire
Material
BOC MIG Wire
AS2074 C1,C2,C3,C4-1,C4-2,C5,C6
BOC Mild Steel MIG Wire
AS/NZS1163 C250
BOC Mild Steel MIG Wire
AS/NZS3678 200,250,300
BOC Mild Steel MIG Wire
ASTM A36,A106
BOC Mild Steel MIG Wire
Stainless Steel
Grade 304/L
BOC Stainless Steel 308LSi
Grade 309
BOC Stainless Steel 309LSi
Grade 316/L
BOC Stainless Steel 316LSi
Physical condition
Surface condition
The welding wire must be free from any surface contamination including
mechanical damage such as scratch marks.
A simple test for checking the surface condition is to run the wire
through a cloth that has been dampened with acetone for 20 secs. If a
Summary of Contents for 180 Multiprocess
Page 1: ...180 Multiprocess Operating manual 6PRRWKDUF GYDQF GYDQF ...
Page 45: ...45 BOC Smootharc 180 Multiprocess operating manual ...
Page 53: ......
Page 54: ......
Page 55: ......