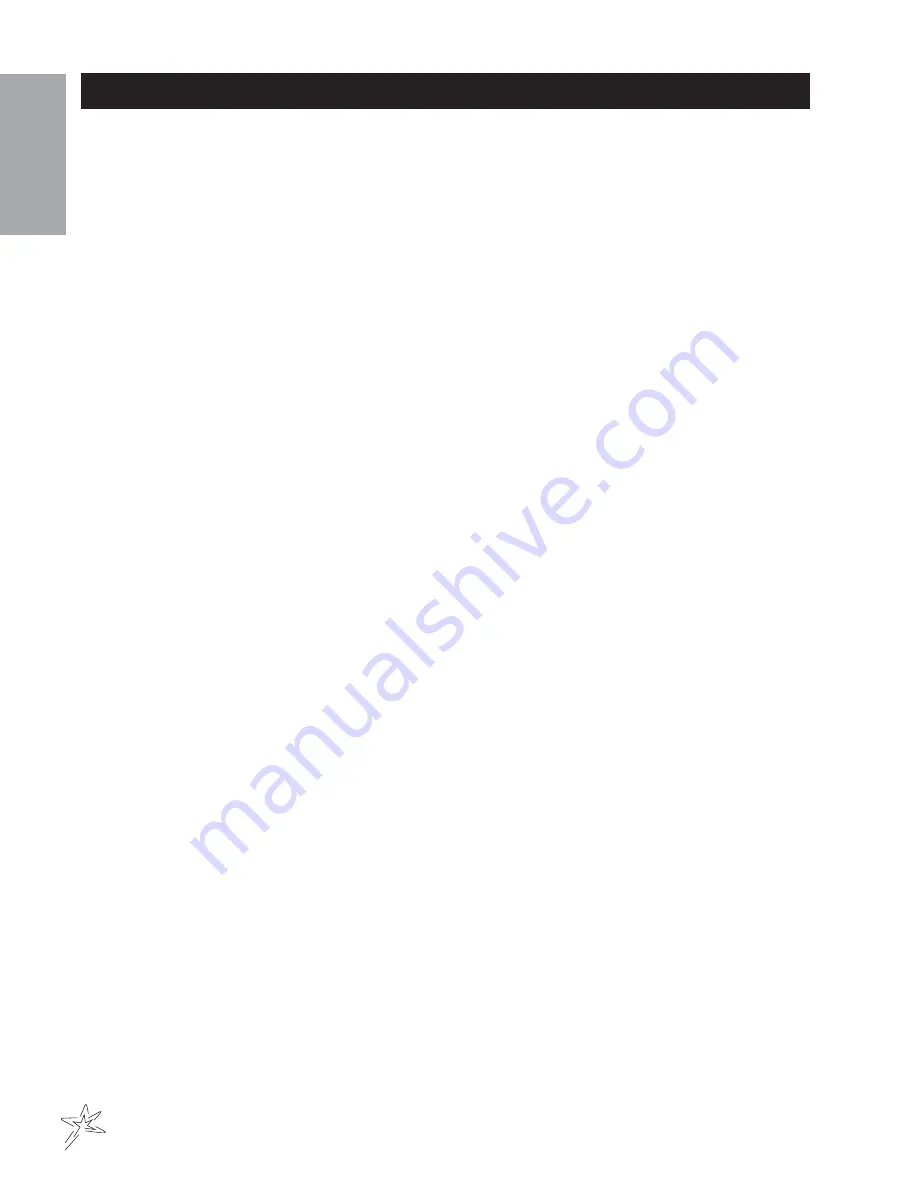
2
Introduction
SAFE PRACTICES
1. It is your responsibility to read this manual and all publications associated with this machine (engine,
accessories and attachments).
2. Never allow anyone to operate or service the machine or its attachments without proper training and
instructions. Never allow minors to operate any equipment.
3. Learn the proper use of the machine, the location and purpose of all the controls and gauges before you
operate the equipment. Working with unfamiliar equipment can lead to accidents.
4. Wear all the necessary protective clothing and personal safety devises to protect your head, eyes, ears,
hands and feet. Operate the machine only in daylight or in good artificial light.
5. Inspect the area where the equipment will be used. Beware of overhead obstructions and underground
obstacles. Stay alert for hidden hazards.
6. Never operate equipment that is not in perfect working order or without decals, guards, shields, or other
protective devices in place.
7. Never disconnect or bypass any switch.
8. Carbon monoxide in the exhaust fumes can be fatal when inhaled, never operate a machine without
proper ventilation.
9. Fuel is highly flammable, handle with care.
10. Keep engine clean. Allow the engine to cool before storing and always remove the ignition key.
11. After engine has started, machine must not move. If movement is evident, the neutral mechanism is not
adjusted correctly. Shut engine off and readjust so the machine does not move when in neutral position.
13. Never use your hands to search for oil leaks. Hydraulic fluid under pressure can penetrate the skin and
cause serious injury.
14. This machine demands your attention. To prevent loss of control or tipping of the vehicle:
A. Use extra caution in backing up the vehicle. Ensure area is clear.
B. Do not stop or start suddenly on any slope.
C. Reduce speed on slopes and in sharp turns. Use caution when changing directions on slopes.
D. Stay alert for holes in the terrain and other hidden hazards.
15. Before leaving operator’s position for any reason:
A. Disengage all drives.
B. Lower all attachments to the ground.
C. Set park brake.
D. Shut engine off and remove the ignition key.
16. Keep hands, feet and clothing away from moving parts. Wait for all movement to stop before you clean,
adjust or service the machine.
17. Keep the area of operation clear of all bystanders.
18. Never carry passengers.
19. Stop engine before making repairs/adjustments or checking/adding oil to the crankcase.
20. Use parts and materials supplied by SMITHCO only. Do not modify any function or part.
21. Do not remove the radiator cap when the engine is hot. When cooled, loosen cap slightly to the stop to
relieve any pressure before removing the cap completely.
These machines are intended for professional maintenance on golf courses, sports turf, and any other
area maintained turf and related trails, paths and lots. No guaranty as to the suitability for any task is
expressed or implied.
Summary of Contents for 48-000-C
Page 13: ...11 NOTES ...
Page 18: ...16 Diagrams BODYANDFRAMEDRAWING HIGH LIFT ...
Page 20: ...18 Parts ROLLOVERPROTECTIONDRAWING ...
Page 22: ...20 Parts STEERINGDRAWING ...
Page 24: ...22 Parts FRONTFORKDRAWING ...
Page 26: ...24 Parts LINKAGEDRAWING HIGH LIFT ...
Page 28: ...26 Parts CONSOLEDRAWING HIGH LIFT ...
Page 30: ...28 Parts FUELANDOILTANKDRAWING HIGH LIFT 60 213 Strainer ...
Page 32: ...30 Parts HYDRAULICLIFTCYLINDERDRAWING INCLINOMETERDRAWING ...
Page 34: ...32 Parts REELLIFTCYLINDERDRAWING TAILGATECYLINDERDRAWING ...
Page 36: ...34 Parts ENGINEANDEXHAUSTDRAWING HIGH LIFT ...
Page 38: ...36 Parts ENGINEANDEXHAUSTDRAWING HIGH LIFT ...
Page 40: ...38 Parts ELECTRICCLUTCHDRIVENBELTDRIVE MUFFLERDRAWING ...
Page 42: ...40 Parts FINGER BRUSHREELDRAWING HIGH LIFT ...
Page 44: ...42 Parts REARAXLEDRAWING HIGH LIFT ...
Page 48: ...46 Parts NOTE 8 is Gage Port 76 32215SERIESSUNDSTRANDPUMPDRAWING HIGH LIFT ...
Page 50: ...48 Parts 48 137REARWHEELMOTOR 10 3C I DRAWING ...
Page 52: ...50 Parts 76 023 3 BANKHYDRAULICVALVE DRAWING ...
Page 54: ...52 NOTES ...
Page 58: ......