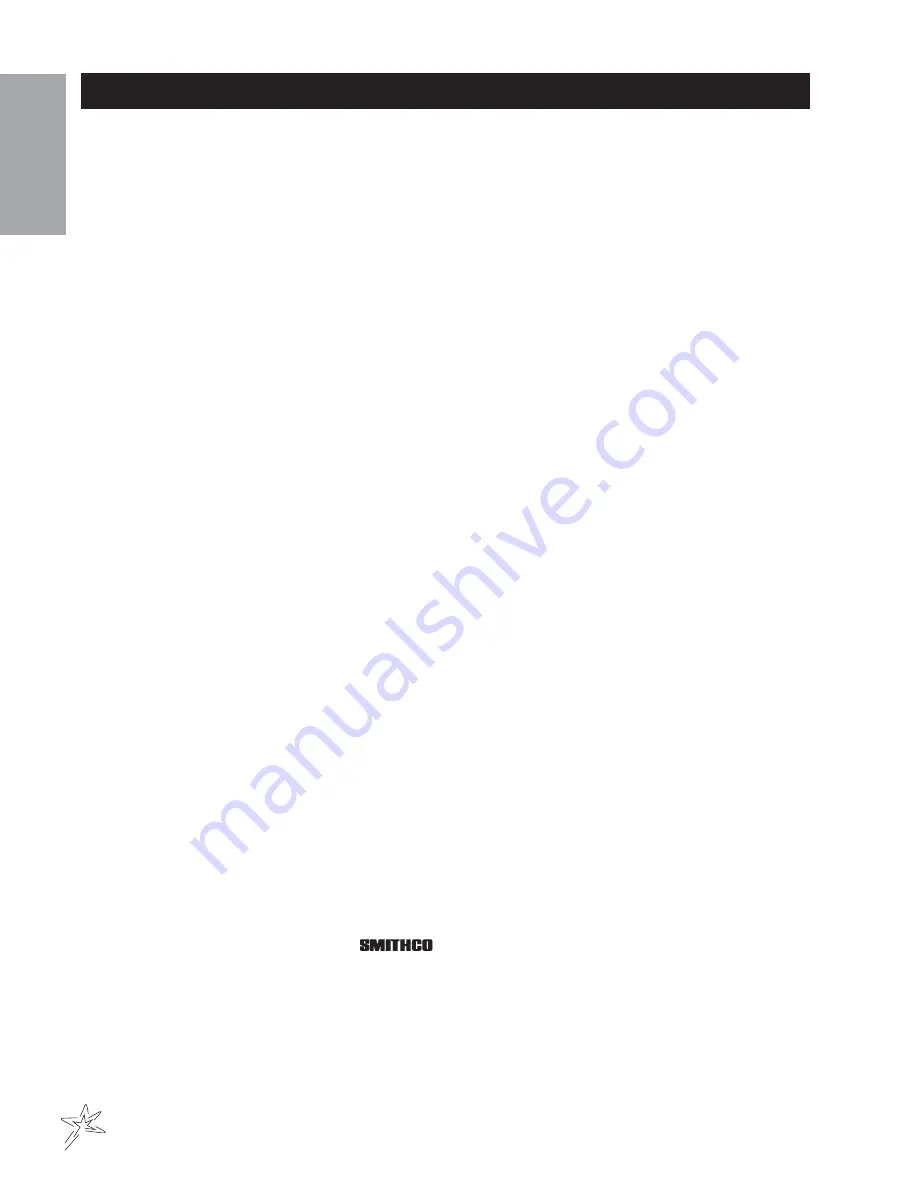
2
Introduction
SAFE PRACTICES
1. It is your responsibility to read this manual and all publications associated with this machine.
2. Never allow anyone to operate or service the machine or its optional equipment without proper training and
instructions. Never allow minors to operate any equipment.
3. Learn the proper use of the machine, the location and purpose of all the controls and gauges before you
operate the equipment. Working with unfamiliar equipment can lead to accidents.
4. Wear all the necessary protective clothing and personal safety devises to protect your head, eyes, ears,
hands and feet. Operate the machine only in daylight or in good artificial light.
5. Inspect the area where the equipment will be used. Pick up all debris you can find before operating.
Beware of overhead obstructions and underground obstacles. Stay alert for hidden hazards.
6. Never operate equipment that is not in perfect working order or without decals, guards, shields, or other
protective devices in place.
7. Never disconnect or bypass any switch.
8. Carbon monoxide in the exhaust fumes can be fatal when inhaled, never operate a machine without proper
ventilation.
9. Fuel is highly flammable, handle with care.
10. Keep engine clean. Allow the engine to cool before storing and always remove the ignition key.
11. Disengage all drives and set park brake before starting the engine.
12. Never use your hands to search for oil leaks. Hydraulic fluid under pressure can penetrate the skin and
cause serious injury.
13. This machine demands your attention. To prevent loss of control or tipping of the vehicle:
A. Use extra caution in backing up the vehicle. Ensure area is clear.
B. Do not stop or start suddenly on any slope.
C. Reduce speed on slopes and in sharp turns. Use caution when changing directions on slopes.
D. Stay alert for holes in the terrain and other hidden hazards.
14. Before leaving operator’s position:
A. Disengage all drives.
B. Set park brake.
C. Shut engine off and remove the ignition key.
D. If engine has to run to perform any maintenance keep hands, feet, clothing and all other parts of body
away from moving parts.
15. Keep hands, feet and clothing away from moving parts. Wait for all movement to stop before you clean,
adjust or service the machine.
16. Keep the area of operation clear of all bystanders.
17. Never carry passengers.
18. Stop engine before making repairs/adjustments or checking/adding oil to the crankcase.
19. Use parts and materials supplied by
only. Do not modify any function or part.
20. Use caution when booms are down as they extend out beyond the center line of the machine.
21. The tank is a confined space, take precaution.
These machines are intended for professional maintenance on golf courses, sports turf, and any other
area maintained turf and related trails, paths and lots. No guaranty as to the suitability for any task is
expressed or implied.
Summary of Contents for 15-600
Page 14: ...12 Diagrams HYDRAULICDIAGRAM...
Page 16: ...14 Parts BODY FRAMEDRAWING...
Page 18: ...16 Parts NOSECONEDRAWING...
Page 20: ...18 Parts NOSECONEDRAWING...
Page 22: ...20 Parts FRONTAXLEDRAWING...
Page 24: ...22 Parts OILANDFUELTANKDRAWING...
Page 26: ...24 Parts SEATPANEL DRAWING...
Page 28: ...26 Parts ENGINE PUMPSANDEXHAUSTDRAWING...
Page 30: ...28 Parts ENGINE PUMPSANDEXHAUSTDRAWING...
Page 32: ...30 Parts SPRAYPUMPDRAWING...
Page 34: ...32 Parts TANKDRAWING TURBO QUADAGITATORDRAWING...
Page 36: ...34 Parts PARKBRAKEANDREARAXLEDRAWING...
Page 38: ...36 Parts 15 301 ORBITROL DRAWING...
Page 40: ...38 Parts 76 398 HYDROSTATIC PUMP DRAWING...
Page 42: ...40 Parts 76 197EATONGEARPUMPDRAWING...
Page 44: ...42 Parts 16 998HYPROPUMPDRAWING...
Page 46: ...44 Accessories 1752PLUMBINGDRAWING RAVEN440...
Page 48: ...46 Accessories 1754PLUMBINGDRAWING RAVEN203...
Page 55: ...53 Accessories NOTES...
Page 56: ...54 Accessories 17 58518 HDSUPERBOOMDRAWING...
Page 58: ...56 Accessories 17 58518 HDSUPERBOOMDRAWING...
Page 62: ...60 Accessories 17 58020 HDSUPERBOOMDRAWING...
Page 64: ...62 Accessories 17 58020 HDSUPERBOOMDRAWING...
Page 68: ...66 Accessories 16 906ELECTRICHOSEREELDRAWING...
Page 72: ...70 Accessories 16 129MANUALHOSEREELDRAWING...
Page 74: ...72 Accessories 14 308HOSEREELMOUNT FORHDBOOMS...
Page 80: ...78 Accessories 17 505FOAMMARKERFOR1750DRAWING...
Page 82: ...80 Accessories FOAMER NOZZLEMOUNT HOSEGUARDMOUNTDRAWING...
Page 90: ...88 Accessories 15 620CHEMICALCLEANLOAD PARTSDRAWING...