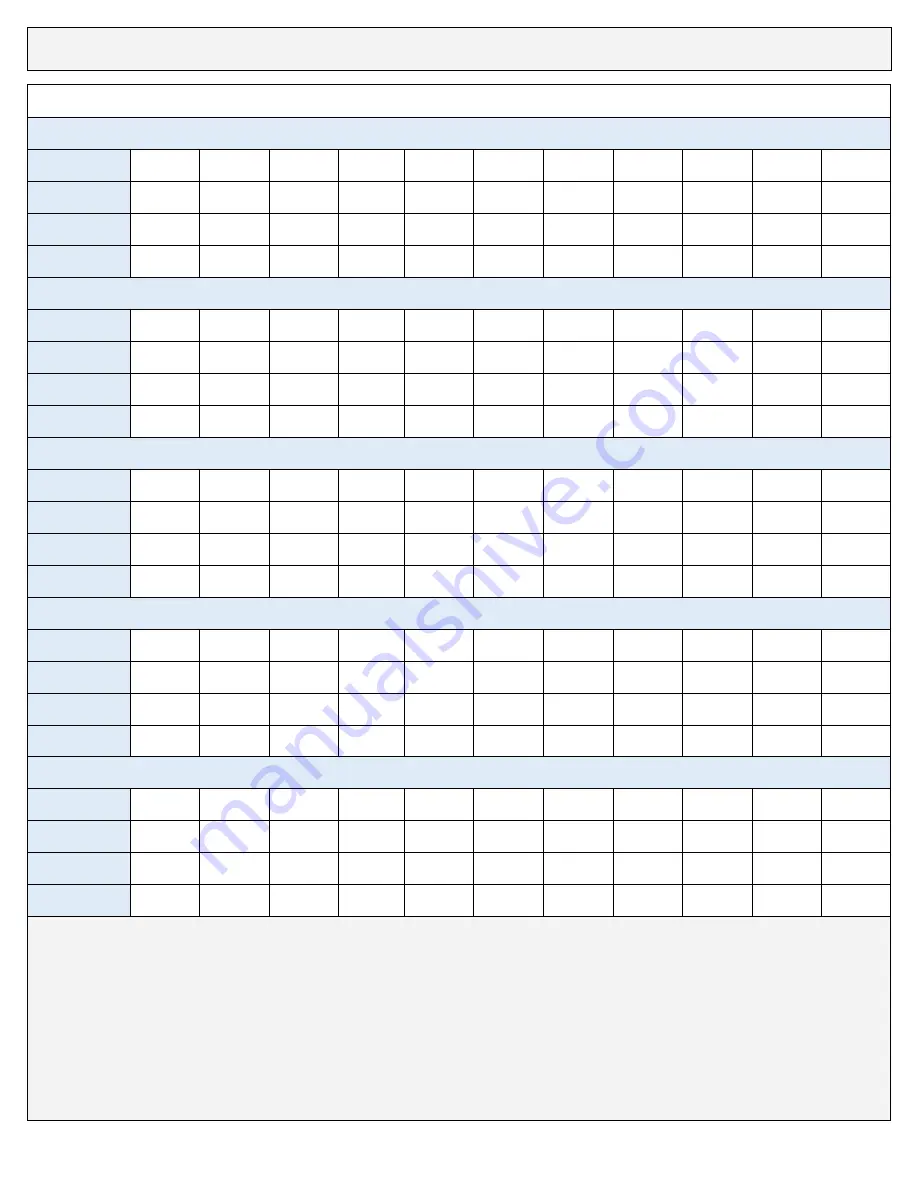
43
Load Charts: URW306
-
T and URW306
URW306
-
T/URW306 (4
-
Part Hook)
Stage 1+2
W/R
6
8
10
11
13
15
17
18.6
MAX
-
EXT
5800
5800
5150
4570
3760
3180
2780
2420
HALF
-
EXT
5800
5800
5100
4520
3600
2750
2100
1760
NOT
-
EXT
5800
5800
4730
3700
2550
2000
1500
1100
Stage 3
W/R
8.5
10
11
13
15
16
18
20
23
25.8
MAX
-
EXT
5000
4500
3900
3150
2710
2500
2160
1870
1580
1360
HALF
-
EXT
5000
4500
3900
3150
2570
2350
1870
1410
1050
880
NOT
-
EXT
5000
4500
3750
2770
2250
2000
1500
1130
720
480
Stage 4
W/R
13
15
16
20
23
26
30
33
MAX
-
EXT
2330
2080
1960
1650
1430
1220
1080
900
HALF
-
EXT
2330
2060
1940
1500
1170
910
650
500
NOT
-
EXT
2330
1810
1540
1050
740
560
330
260
Stage 5
W/R
15
16
20
23
26
30
33
36
40.2
MAX
-
EXT
1670
1480
1100
920
820
710
650
590
570
HALF
-
EXT
1670
1480
1070
920
780
650
550
440
350
NOT
-
EXT
1670
1480
910
610
470
340
260
200
80
Stage 6
W/R
16
18
20
23
26
30
33
36
39
43
47.3
MAX
-
EXT
720
660
610
550
510
450
410
370
350
300
280
HALF
-
EXT
720
660
610
550
510
450
410
330
270
190
150
NOT
-
EXT
720
660
610
550
450
290
240
170
130
110
80
The above tables are for RATED LOADs; in order to determine the SPYDERCRANE
’
s NET
-
RATED Capacity, deduct
70 lbs
(if using the 4
-
Part Hook Block).
To use this Load Chart, you must determine the SPYDERCRANE
’
s:
Deployment State
Boom Stage
Working Radius (W/R)