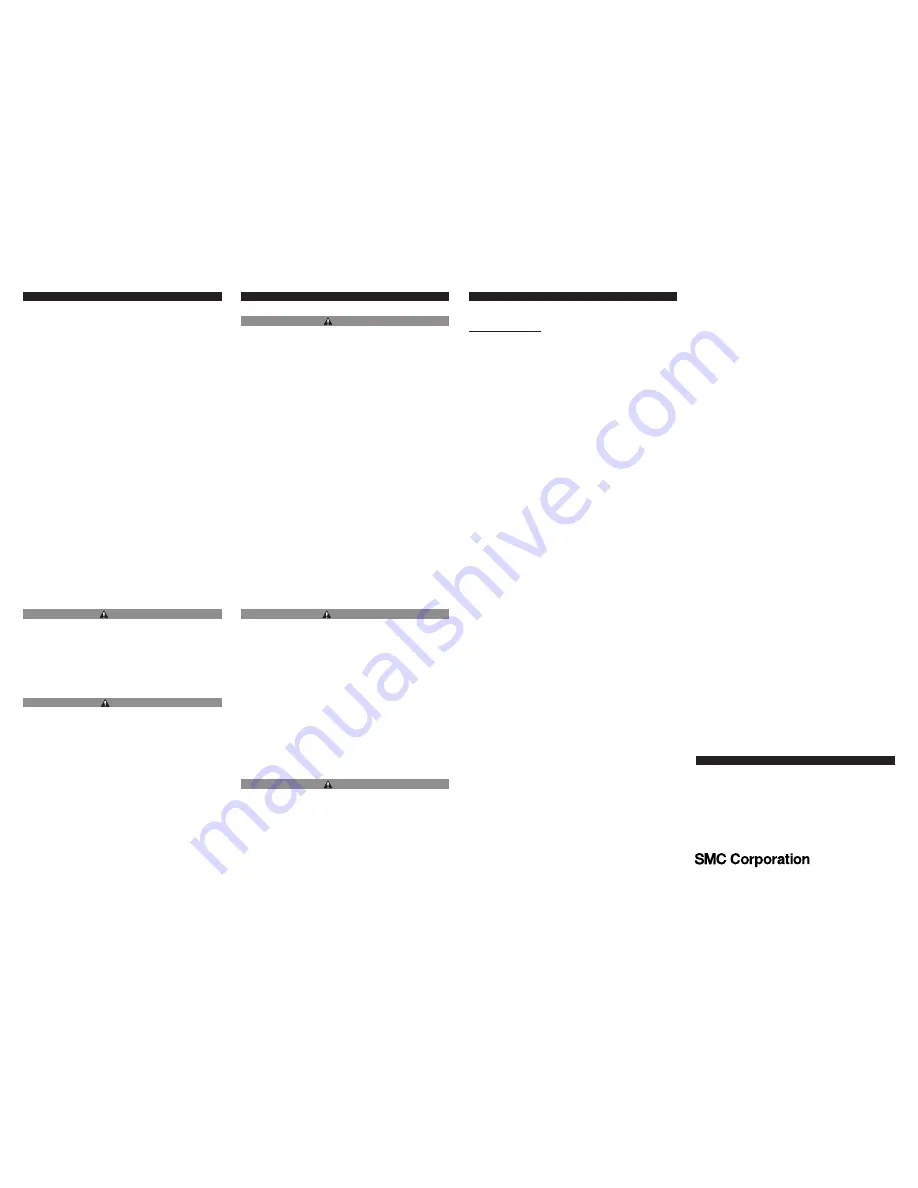
3 Installation (continued)
5. Quality of operating fluids
Install a suitable filter (strainer) immediately up stream of the valve to
prevent foreign matter within the fluid from causing malfunctions and
seal failure. Any foreign matter can promote wear of the valve seat and
can stick to sliding parts.
6. Quality of operating air.
1) Use clean air.
If the compressed air supply includes chemicals, synthetic materials
(including organic solvents), salinity, corrosive gas, etc., it can lead
to damage or malfunction.
2) Install an air filter.
Install an air filter at the up stream side to the valve. Filtration degree
should be 5ìm or less.
3) Install an air dryer, after cooler, etc.
Compressed air that includes excessive drainage may cause
malfunction of valves and other pneumatic equipment. To prevent
this, install an air dryer or after cooler, etc.
4) If excessive carbon powder is seen, install a mist separator on the
upstream side of the valve.
If excessive carbon powder is generated by the compressor, it may
adhere to the inside of valves and cause malfunction. For
compressed air quality, refer to “Air Cleaning Equipment” catalog.
7. Ambient environment
Operate within the ambient operating temperature range. After
confirming the compatibility of the product’s component materials with
the ambient environment, operate so that fluid does not adhere to the
product’s exterior surfaces.
8. Countermeasures for static electricity.
Since static electricity may be generated depending on the fluid being
used, implement suitable countermeasures.
SGH100-TFM86
3.12 Mounting
WARNING
1. Stop operation if air leakage increases and the equipment does
not operate properly.
Check mounting conditions after air and power supplies are connected.
Initial function and leakage tests should be performed after installation.
2. Instruction manual (this document)
Install product only after reading and understanding the safety
instructions. Keep on file so that it can be referred to when necessary.
3. Coating
Warnings or specifications indicated on the product should not be
erased, removed, or covered up.
CAUTION
1. Do not apply external force to the pilot valve section.
Apply spanner to the external connection part when tightening.
2. Do not warm the pilot valve assembly with heat insulation
material.
Heat insulation tape should only be used on the piping or the body of
the valve.
3. Secure with brackets, except in the case of steel and copper
piping.
4. Do not use in locations subjected to vibrations. If this is
impossible, the arm from the body should be as short as possible
to prevent resonance.
5. Installing the product horizontally should be avoided. Machining
chips could collect in the plate ass'y and the life expectancy of the
product will be reduced.
4 Maintenance
4.1 Electrical precautions
CAUTION
1. Applied voltage.
When electric power is connected to the solenoid valve, be careful to apply
the proper voltage. Improper voltage may cause malfunction or coil
damage.
2. Confirm the connections.
After completing the wiring, confirm that the connections are made
correctly.
3. Use electrical circuits that do not generate chattering in their
contacts.
4. Use a voltage that is within ±10% of the rated voltage.
5. When a surge from the solenoid affects the electrical circuitry, adopt
an option that comes with the surge voltage protection circuit.
4.2 Operating Environment
WARNING
1. Perform maintenance procedures as shown in the instruction
manual. (This document).
If handled improperly malfunction or damage of machinery/equipment may
occur.
2. Removing the product
To avoid the risk of being burned, ensure that the valve has had sufficient
time to cool before performing work.
1. Shut off the fluid supply and release the fluid pressure in the system.
2. In the case of air pilot or air-operated type, shut off the supply air
source and discharge the compressed air inside the pilot piping.
3. Shut off the power supply.
4. Remove the product.
3. Low frequency operation.
Valves should be operated at least once every 30 days to prevent
malfunction. (Use caution regarding the air supply).
For optimum usage, conduct regular inspections every 6 months.
4. Manual override
When the manual override is operated, connected equipment will be
actuated.
5.
Do not disassemble the product. Products that have been
disassembled cannot be guaranteed.
CAUTION
1. Filters and strainers
1. Be careful regarding clogging of filters and strainers.
2. Replace filter elements after one year of use, or earlier if the pressure
drop reaches 0.1 MPa.
3. Clean strainers when the pressure drop reaches 0.1 MPa.
2. Lubrication (Pilot air line)
When using after lubricating, never forget to lubricate continuously.
3. Storage
In case of long term storage after use with heated water, thoroughly
remove all moisture to prevent rust and deterioration of rubber materials,
etc.
4 Maintenance (continued)
4. Drain flushing
Remove drainage from air filters regularly. (Refer to the specifications.)
Precautions on Handling
Valves will reach high temperatures from high temperature fluids. Use
caution, as there is a danger of being burned if a valve is touched directly.
5 Contacts
URL http://www.smcworld.com (Global) http://www.smceu.com (Europe)
Specifications are subject to change without prior notice from the manufacturer.
© SMC Corporation All Rights Reserved.
AUSTRIA
(43) 2262 62 280
NETHERLANDS
(31) 20 531 8888
BELGIUM
(32) 3 355 1464
NORWAY
(47) 67 12 90 20
CZECH REP.
(420) 5 414 24611
POLAND
(48) 22 211 9600
DENMARK
(45) 70 25 29 00
PORTUGAL
(351) 21 471 1880
FINLAND
(358) 207 513513
SLOVAKIA
(421) 2 444 56725
FRANCE
(33) 1 64 76 1000
SLOVENIA
(386) 73 885 412
GERMANY
(49) 6103 4020
SPAIN
(34) 945 18 4100
GREECE
(30) 210 271 7265
SWEDEN
(46) 8 603 0700
HUNGARY
(36) 1 371 1343
SWITZERLAND
(41) 52 396 3131
IRELAND
(353) 1 403 9000
UNITED KINGDOM
(44) 1908 56 3888
ITALY
(39) 02 92711