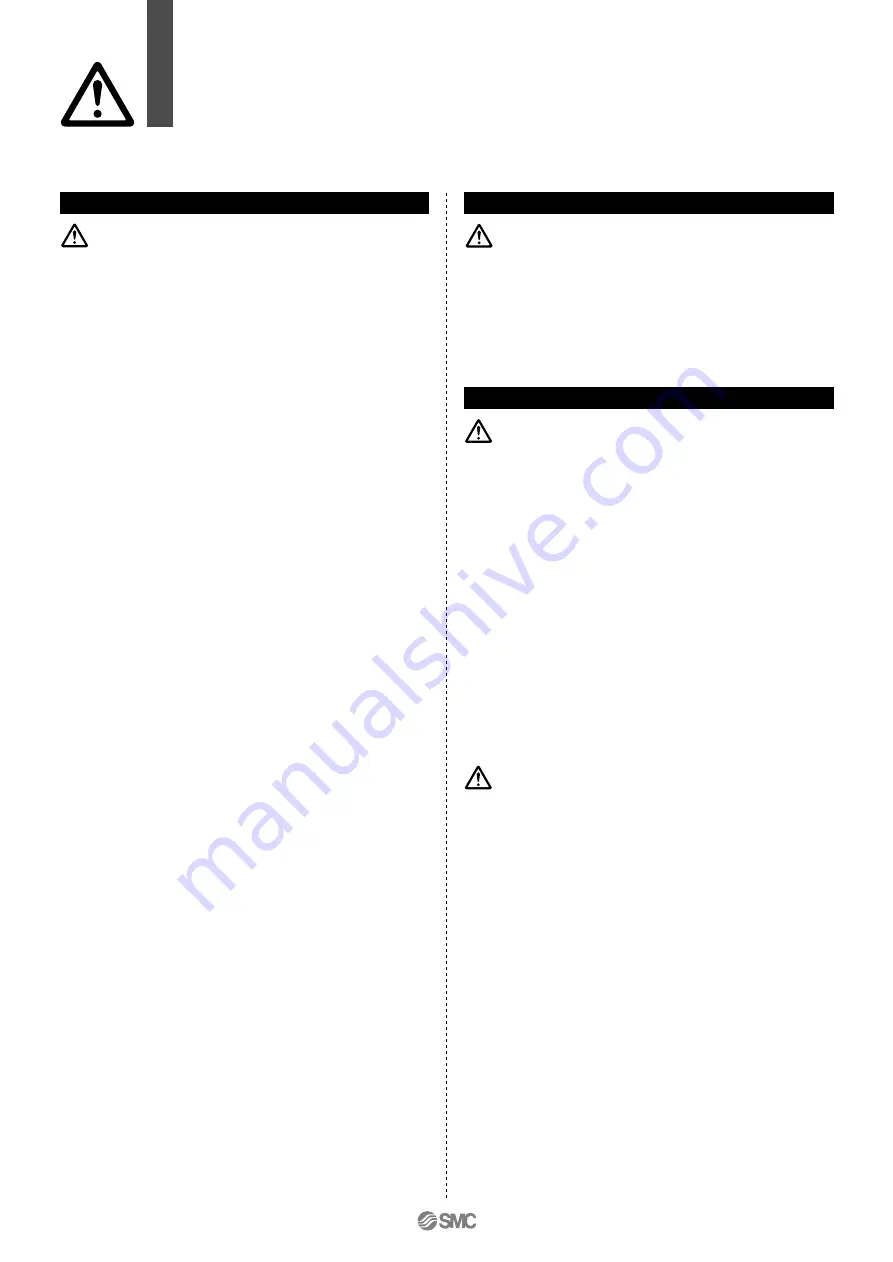
Series
CUJ
Actuator Precautions 1
Be sure to read before handling.
Design
Warning
1. There is a danger of sudden action by air
cylinders if sliding parts of machinery are
twisted, etc., and changes in forces occur.
In such cases, human injury may occur; e.g., by catching
hands or feet in the machinery, or damage to the machinery
itself may occur. Therefore, the machine should be designed
to avoid such dangers.
2. A protective cover is recommended to minimize
the risk of human injury.
If a driven object and moving parts of a cylinder pose a danger
of human injury, design the structure to avoid contact with the
human body.
3. Securely tighten all stationary parts and
connected parts so that they will not be-
come loose.
Especially when a cylinder operates with high frequency or is
installed where there is a lot of vibration, ensure that all parts
remain secure.
4. A deceleration circuit or shock absorber may be
required.
When a driven object is operated at high speed or the load is
heavy, a cylinder’s cushion will not be sufficient to absorb the
impact. Install a deceleration circuit to reduce the speed
before cushioning, or install an external shock absorber to
relieve the impact. In this case, the rigidity of the machinery
should also be examined.
5. Consider a possible drop in circuit pressure
due to a power outage, etc.
When a cylinder is used in a clamping mechanism, there is a
danger of work pieces dropping if there is a decrease in
clamping force due to a drop in circuit pressure caused by a
power outage, etc. Therefore, safety equipment should be
installed to prevent damage to machinery and human injury.
Suspension mechanisms and lifting devices also require
consideration for drop prevention.
6. Consider a possible loss of power source.
Measures should be taken to protect against human injury and
equipment damage in the event that there is a loss of power to
equipment controlled by pneumatics, electricity or hydraulics,
etc.
7. Design circuitry to prevent sudden lurching
of driven objects.
When a cylinder is driven by an exhaust center type
directional control valve or when starting up after residual
pressure is exhausted from the circuit, etc., the piston and its
driven object will lurch at high speed if pressure is applied to
one side of the cylinder because of the absence of air
pressure inside the cylinder. Therefore, equipment should be
selected and circuits designed to prevent sudden lurching,
because there is a danger of human injury and/or damage to
equipment when this occurs.
8. Consider emergency stops.
Design so that human injury and/or damage to machinery and
equipment will not be caused when machinery is stopped by a
safety device under abnormal conditions, such as a power
outage or a manual emergency stop.
Design
Warning
9. Consider the action when operation is re-
started after an emergency stop or abnormal
stop.
Design the machinery so that human injury or equipment
damage will not occur upon restart of operation.
When the cylinder has to be reset at the starting position,
install safe manual control equipment.
Selection
Caution
Warning
1. Confirm the specifications.
The products included in this catalog are designed according
to use in industrial compressed air systems. If the products
are used in conditions where pressure and/or temperature
are out of specification, damage and/or malfunction may be
caused. Do not use in these conditions. (Refer to
specifications.)
Consult SMC if you use a fluid other than compressed air.
2. Intermediate stops
When intermediate stopping of a cylinder piston is performed
with a 3 position closed center type directional control valve, it
is difficult to achieve stopping positions as accurate and
precise as with hydraulic pressure due to the compressibility
of air.
Furthermore, since valves and cylinders are not guaranteed
for zero air leakage, it may not be possible to hold a stopped
position for an extended period of time. Contact SMC in case
it is necessary to hold a stopped position for an extended
period.
1. Operate within the limits of the maximum
usable stroke.
The piston rod will be damaged when operated with a stroke
exceeding the maximum stroke range. Refer to the air
cylinder selection procedures regarding the maximum usable
stroke.
2. Operate the piston within a range such that
collision damage will not occur at the end of
the stroke.
Operate within a range such that damage will not occur when
the piston having inertial force stops by striking the cover at
the stroke end. Refer to the cylinder selection procedures for
the range within which damage will not occur.
3. Use a speed controller to adjust the cylinder
drive speed, gradually increasing from a low
speed to the desired speed setting.
4.
Provide an intermediate support for a
cylinder with a long stroke.
If the cylinder has a long stroke, provide an intermediate
support to prevent the rod from sagging and the tube from
bending, as well as to prevent damage to the rod due to
vibrations or external loads.
16
Summary of Contents for CDUJB10-20D
Page 1: ...Mini Free mount Cylinder Series CUJ 4 6 8 10 CAT ES20 157 A...
Page 27: ......