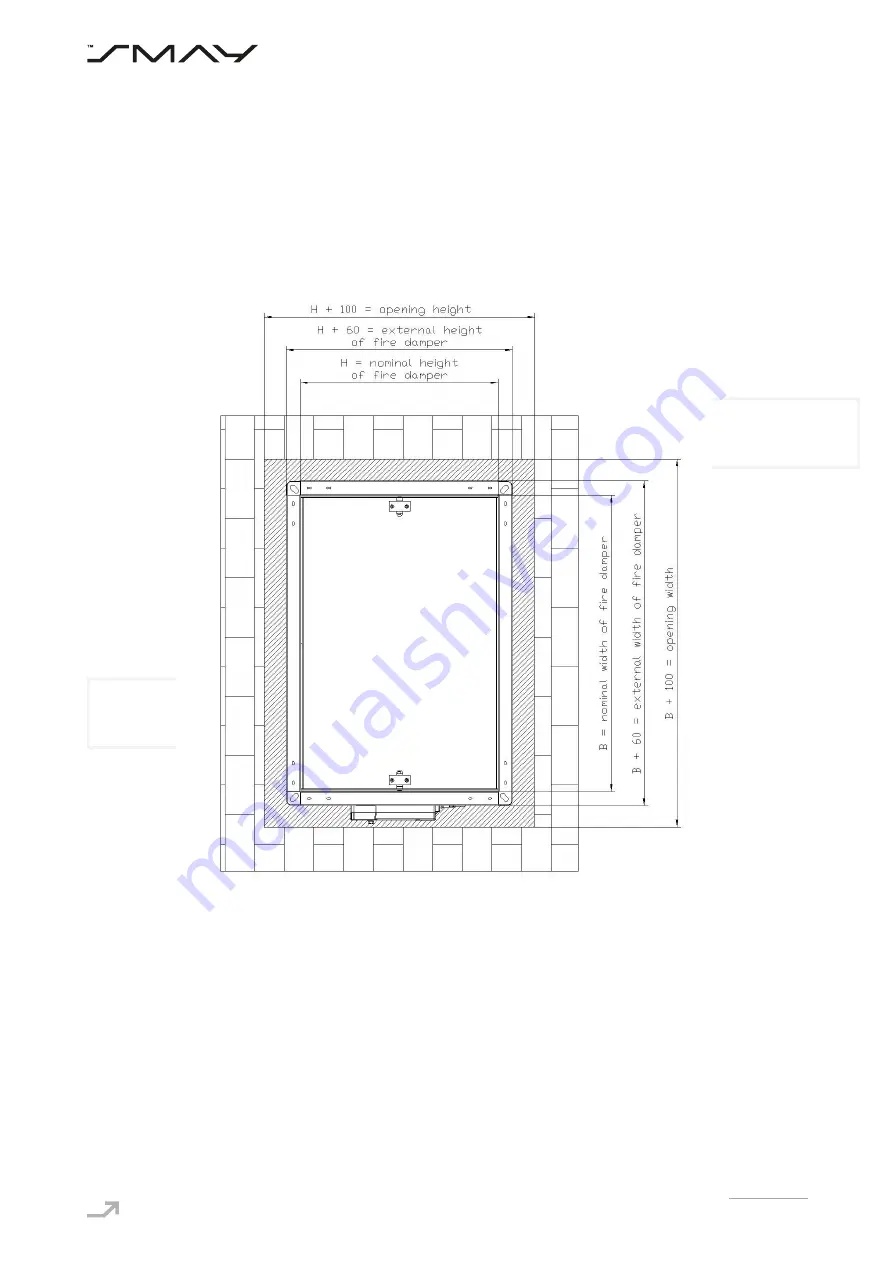
Version 6.00
Date of editing: 16.09.2022
r.
Page 18 of 30
Technical documentation
KWP-L
7.2.
INSTALLATION TECHNOLOGY
–
RIGID WALL
a.
Make an opening in the wall with the dimensions 100 [mm] (acceptable
80 ÷ 120 [mm])
greater than the
nominal dimensions of the fire damper = B+100 and H+100.
b.
Put the closed fire damper into the installation opening and support or suspend, in this way that the minimum
installation depth mark is on the plane of wall surface.
c.
After setting the fire damper as described, fill the gap between the fire damper and the wall with cement,
cement-lime mortar or concrete.
d.
After the mortar has dried (about 48 hours), remove the supports or suspensions, check the fire damper correct
operation and leave it in open position.
Figure 6. Installation method of fire dampers KWP-L in rigid wall with vertical rotation axis of baffle