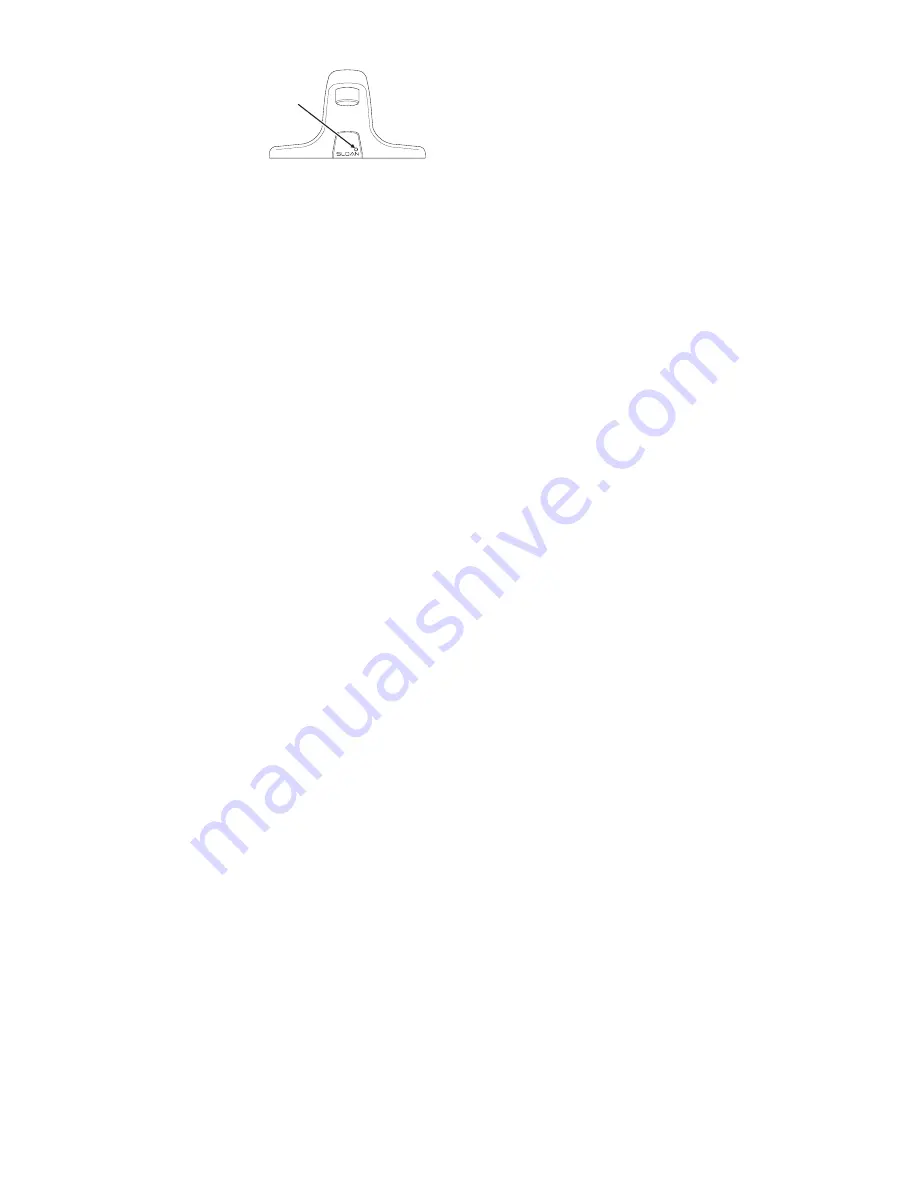
TROUBLESHOOTING GUIDE
1. PROBLEM:
Sensor troubleshooting
LED does not function
(red indicator light
does not flash during
set-up procedure).
CAUSE:
No battery power is being supplied to Sensor.
SOLUTION:
Ensure that the batteries are installed properly. Check that
the orientation of each battery matches the positive (+)
and negative (-) symbols shown on the bottom of the
battery compartment. Reinsert the Battery Compartment
into the Control Module.
CAUSE:
Insufficient battery power is being supplied to sensor.
SOLUTION:
One (or more) of the batteries is “dead.” To ensure proper
operation, insert four (4) new C-size Alkaline batteries.
Check that the orientation of each battery matches the
positive (+) and negative (-) symbols shown on the bottom
of the Battery Compartment. Reinsert the Battery
Compartment into the Control Module.
CAUSE:
Sensor Cable is not properly inserted.
SOLUTION:
Disconnect and reconnect Sensor Cable to the Control
Module.
CAUSE:
Sensor range is set at minimum distance.
SOLUTION:
Increase Sensor range. Use a small screwdriver to turn the
potentiometer screw (white screw in a blue base)
clockwise.
CAUSE:
Control Module assembly is defective.
SOLUTION:
Replace EBF-60-A Control Module assembly.
2. PROBLEM:
Faucet does not deliver any water when Sensor is
activated.
INDICATOR:
Solenoid valve produces audible “CLICK.”
CAUSE:
Water supply valve is closed.
SOLUTION:
Open the Supply Stop.
INDICATOR:
Solenoid valve DOES NOT produce an audible “CLICK.”
CAUSE:
Solenoid lead is not properly connected to the Control
Module.
SOLUTION:
Disconnect and reconnect Solenoid lead to the Control
Module.
CAUSE:
Batteries are not installed properly.
SOLUTION:
Check that the orientation of each battery matches the
positive (+) and negative (-) symbols shown on the bottom
of the battery compartment. Reinsert the Battery
Compartment into the Control Module. The
troubleshooting LED should flash RED when a user is
detected.
3. PROBLEM:
Faucet delivers only a slow flow or dribble when
Sensor is activated.
CAUSE:
Water supply valve is partially closed.
SOLUTION:
Completely open the Supply Stop.
CAUSE:
Solenoid Filter is clogged.
SOLUTION:
Remove, clean, and reinsert. Replace EBF-1004-A
Solenoid Filter Kit if necessary.
CAUSE:
Aerator or Spray head is clogged.
SOLUTION:
Remove, clean, and reinsert.
4. PROBLEM:
Faucet does not stop delivering water or continues to
drip after user is no longer detected (automatic
shut-off fails even when batteries are removed).
CAUSE:
Solenoid Valve has been connected backwards.
SOLUTION:
Disassemble Solenoid Valve compression fittings at both
the inlet and outlet positions. The water should flow from
inlet through the Solenoid Valve to the outlet according to
the direction of the arrow shown on the side of the
Solenoid Valve. Reconnect the compression fittings in the
correct orientation.
CAUSE:
Solenoid Valve is dirty.
SOLUTION:
Backflush by reversing water flow (opposite to the direction
shown by the arrow on the side of the Solenoid Valve)
through the Solenoid Valve. Reconnect the compression
fittings in the correct orientation. Activate faucet.
CAUSE:
Solenoid Valve Module is defective.
SOLUTION:
Replace EBF-62-A Solenoid Valve Module.
5. PROBLEM:
The water temperature is too hot or too cold on a
faucet connected to hot and cold supply lines with
two Back Checks.
CAUSE:
Supply Stops are not adjusted properly.
SOLUTION:
Adjust Supply Stops.
CAUSE:
One Back Check is installed backwards.
SOLUTION:
Reinstall Back Check.
NOTE:
For some systems, a thermostatic mixing valve may be
required.
If further assistance is required, please contact the Sloan Valve Company
Installation Engineering Department at 1-888-SLOAN-14.
IMPORTANT NOTES
DO NOT INSTALL THE BATTERIES UNTIL THE FAUCET IS COMPLETELY INSTALLED. If the batteries are installed before the sensor
cable has been connected to the control module, the faucet will not properly set the sensing range for the sink on which it has been installed.
LED
8