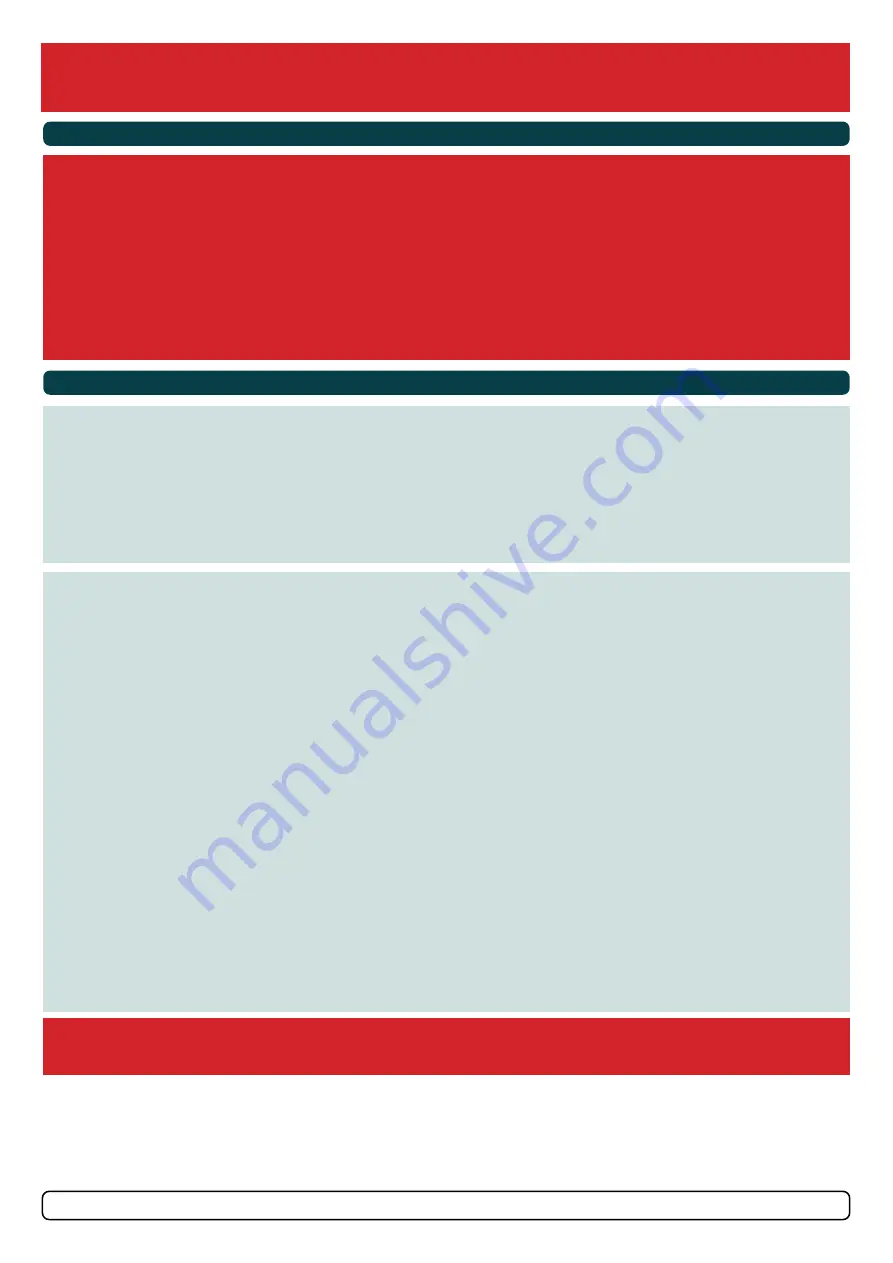
3
6398
12
2022
-
HydroPOD 35 & 50
The installer must read this document to ensure necessary familiarity with the product before installation.
Instructions in this document cannot be guaranteed to comply with all international and national regulations. It is the responsibility of the
installer to follow all applicable international and national regulations when installing Sleipner products.
The recommendations given in this document are guidelines ONLY, and Sleipner strongly recommends that advice is obtained from a person
familiar with the particular vessel and applicable regulations.
This document contains general installation instructions intended to support experienced installers. If you are not skilled in this type of work,
please contact professional installers for assistance.
If required by local regulation, electrical work must be done by a licensed professional.
Appropriate health and safety procedures must be followed during installation.
Faulty installation of Sleipner products will render all warranties given by Sleipner Motor AS.
MC_0038
Responsibility of the Installer
Failure to follow the considerations and precautions can cause serious injury,
damage and will render all warranties given by Sleipner Motor as VOID.
MC_0411
MC_0425
For thruster systems
• Do not install the thruster in a position where you need to cut a stiffener/ stringer/ support that may jeopardise the hull integrity without checking
with the boat builder this can be done safely.
• We advise painting the gear house and propellers with anti-fouling.
(NB: Do not paint the anodes, sealing, rubber fi ttings or propeller shafts)
• There is only room for a thin coat of primer and two layers of anti-fouling between the tunnel and the props.
• Never run the thruster out of water.
MC_0440
General Installation Considerations and Precautions Guidelines
NEVER Disassemble any part of the Ignition Protected assembly. Tampering with the Ignition Protected assembly will cause it to lose this
safety feature. If there is a problem with your Ignition Protected motor, please contact your dealer.
MC_0007
MC_0427
For SX/P35 and SX/P50 thruster systems
• Ensure that the external thruster assembly does not disturb the water flow under the hull. At higher speeds, if the thruster is installed to
low it can cause damage to the thruster and/ or add additional drag and unwanted water splashing.
• The minimum tunnel depth from the water surface is 140mm (5,51‘) to the centre of tunnel diameter. Place the Thruster as deep as possible for
better performance and reduced noise.
• When installing the thruster ensure it does not foul existing equipment inside the boat like motor bedding etc.
• If able ensure that stern-drives/ trim-tabs do not interfere with the water flow from the thruster as this can reduce the thrust effectiveness
considerably. We recommend the use of our Sleipner cowls to enhance the performance and allow installation in shallow draft boats. Sleipner
cowls will also minimise the effect if stern-drives/ trim-tabs obstruct the thruster.
• Ensure there is enough space both inside and outside the transom of the boat and the thruster does not get in conflict with existing equipment
inside the boat like steerage links etc.
(NB: It is possible to mount the tunnel offset from the boat’s centre line if necessary.)
• Heat protection cut off is calculated from the thruster motor. To avoid cable overheating do not install place the volt cables from the thruster to the
control box near any heat sources.
(NB: excluding SXP thrusters)
• Do not lift it by internal cable connections, main terminals.
• The thruster power supply circuit must include the recommended sized fuse and a battery isolation switch.
• The electro motor, components and cables must be mounted so they remain dry at all times.
• Do not use abrasive tools damaging the existing Epoxy coating when preparing for antifouling paint.