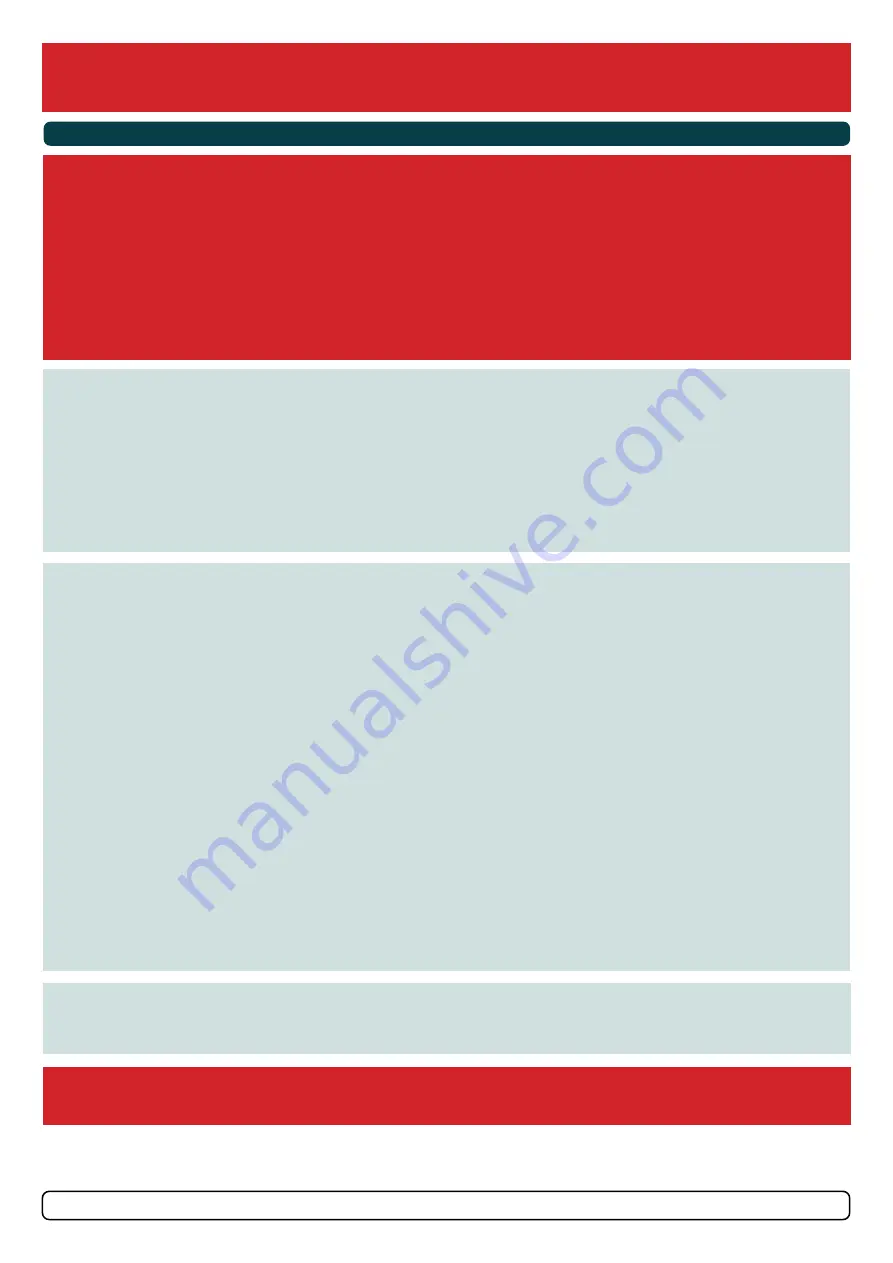
3
5897
14
2022
-
SE IP 60 s2
NEVER Disassemble any part of the Ignition Protected assembly. Tampering with the Ignition Protected assembly will cause it to lose this
safety feature. If there is a problem with your Ignition Protected motor, please contact your dealer.
MC_0007
MC_0031
For electric motor thrusters
• The thruster must NOT be installed in compartments that require ignition proof electric equipment. If necessary, make a separate compartment.
(NB: Ignition Protected systems are tested to be installed in areas with possible explosive gases in accordance with ISO 8846)
• When installing the thruster electric motor in small compartments, ensure the compartment is well ventilated to allow for cooling of the electro
motor.
• If the height of the room you are installing the thruster is limited, the thruster can be installed horizontally or at any angle in-between.
- If the electro motor is positioned more than 30 degrees off vertical, it must be supported separately.
- Beware of keeping installation within advised measurements. No part of the propeller or gear house must be outside the tunnel.
• The electro motor, components and cables must be mounted so they remain dry at all times.
• We advise painting the gear house and propellers with anti-fouling.
(NB: Do not paint the anodes, sealing, rubber fi ttings or propeller shafts)
• Do not fi nish the inside of the tunnel with a layer of gel-coat/ topcoat or similar. There is only room for a thin coat of primer and two layers of anti-
fouling between the tunnel and the props.
• Don’t install the electric motor close to easily flammable objects or equipment as it will reach over 100°C before the temperature switch is
activated.
• Do not store items close to the thruster motor. Any loose items near the thruster motor is a potential fi re hazard and can cause undesired short-
circuiting.
• Do not lift it by internal cable connections, main terminals.
• The thruster power supply circuit must include the recommended sized fuse and a battery isolation switch.
The installer must read this document to ensure necessary familiarity with the product before installation.
Instructions in this document cannot be guaranteed to comply with all international and national regulations. It is the responsibility of the
installer to follow all applicable international and national regulations when installing Sleipner products.
The recommendations given in this document are guidelines ONLY, and Sleipner strongly recommends that advice is obtained from a person
familiar with the particular vessel and applicable regulations.
This document contains general installation instructions intended to support experienced installers. If you are not skilled in this type of work,
please contact professional installers for assistance.
If required by local regulation, electrical work must be done by a licensed professional.
Appropriate health and safety procedures must be followed during installation.
Faulty installation of Sleipner products will render all warranties given by Sleipner Motor AS.
MC_0038
Responsibility of the Installer
MC_0426
For DC electric motors
• The electro motor will generate some carbon dust so any storage compartments must be separated from the thruster to prevent nearby items
becoming dusty/ dirty.
(NB: IP version motors generate dust but are enclosed.)
Failure to follow the considerations and precautions can cause serious injury,
damage and will render all warranties given by Sleipner Motor as VOID.
MC_0411
MC_0425
For thruster systems
• Do not install the thruster in a position where you need to cut a stiffener/ stringer/ support that may jeopardise the hull integrity without checking
with the boat builder this can be done safely.
• We advise painting the gear house and propellers with anti-fouling.
(NB: Do not paint the anodes, sealing, rubber fi ttings or propeller shafts)
• There is only room for a thin coat of primer and two layers of anti-fouling between the tunnel and the props.
• Never run the thruster out of water.
• The electric/ hydraulic motor must be handled with care. Do not place down the thruster on the motor drive shaft or gear leg if attached.