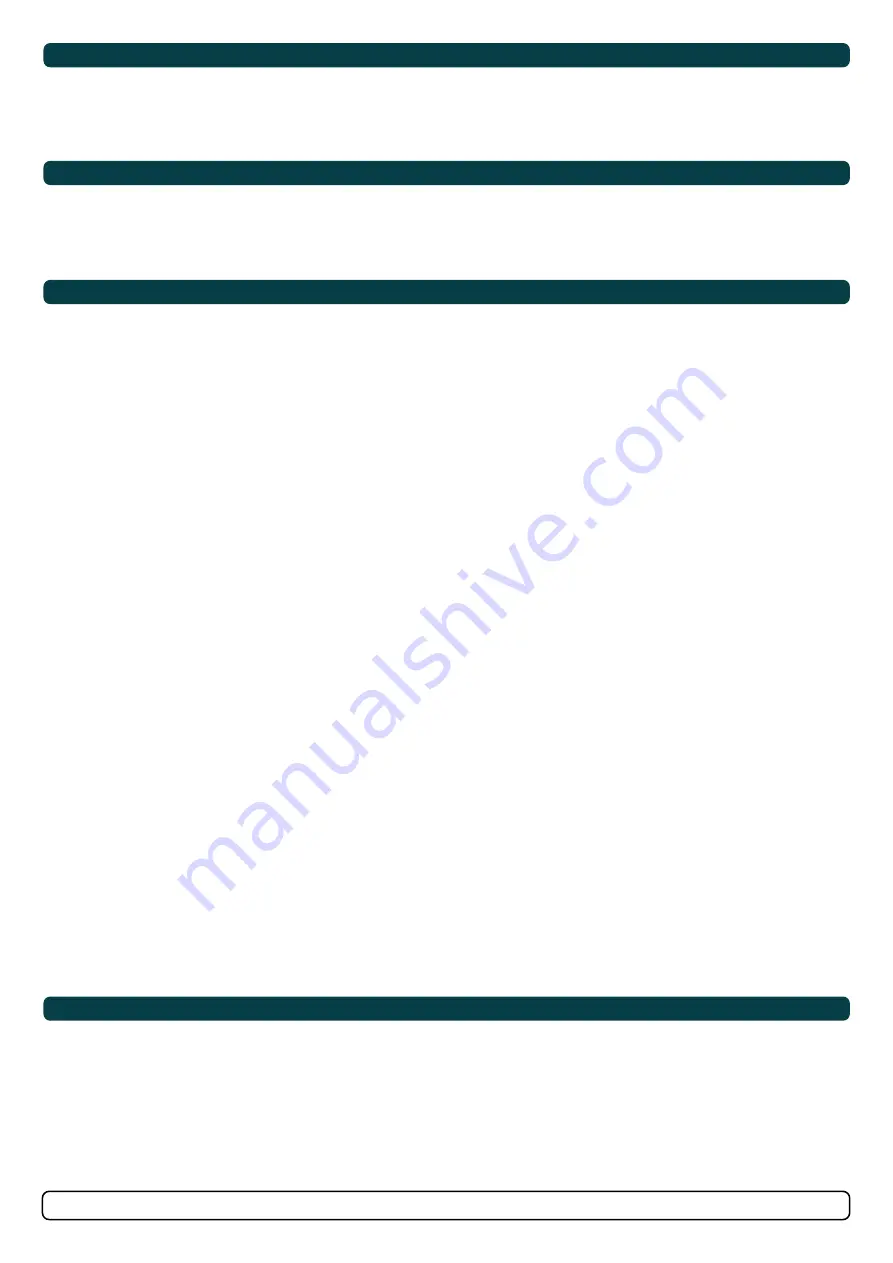
23
7241
5
2022
-
ERV130 & ERV170 & ERV210
MC_0033
Pre-delivery Checklist
[].......... The bolts holding the gear house and motor bracket together are tightened correctly.
[].......... The bolts holding the motor to its bracket are tightened correctly.
[].......... All electrical connections are clean, dry and tight, and the correct cable, fuse and main
switch size.
[].......... Check that there is no electrical connection between the electro motor body and positive
terminal on the motor, and between the electro motor body and the negative (A1) terminal
on the motor with an ohm meter.
[].......... Anti-fouling has been applied to the gear house and propeller but NOT anodes, sealing/
rubber fi ttings or propeller shafts.
[].......... Propeller is fastened correctly to the shaft.
[].......... Propeller turns freely in tunnel.
[].......... The anode and/ or holding screw is tightened well with thread glue.
[].......... Check the boat for potential water leakage around installation areas.
[].......... Correct drive direction as per control panel.
[].......... User Manual is supplied to the owner.
The thruster has been installed as per the instructions in this manual and all points in checklist above have been controlled.
Signed: .........................................................................................
Date: .............................................................................................
Thruster type: ................................................................................................................................................................................................
Serial number:...............................................................................................................................................................................................
Date of delivery:.............................................................................................................................................................................................
Correct drive direction as per control panel: ..................................................................................................................................................
The compartment for the thruster has been isolated from general bilge water and has no obvious or suspected risks for flooding:
......................................................................................................................................................................................................................
......................................................................................................................................................................................................................
......................................................................................................................................................................................................................
Other comments by installer: ........................................................................................................................................................................
.......................................................................................................................................................................................................................
.......................................................................................................................................................................................................................
At Sleipner we continually reinvest to develop and offer the latest technology in marine advancements. To see the many unique designs we have
patented visit our website www.sleipnergroup.com/patents
Find your local professional dealer from our certifi ed
worldwide network for expert service and support.
visit our website
www.sleipnergroup.com/support
For additional supporting documentation, we advise you
to visit our website
www.sleipnergroup.com
and fi nd your
Sleipner product.
Service and Support
Product Spare Parts and Additional Resources
Warranty statement
Patents
MC_0024
MC_0024
MC_0024
MC_0024
MC_0024
1.
Sleipner Motor AS (The “Warrantor”) warrants that the equipment (parts, materials, and embedded software of products) manufactured by
the Warrantor is free from defects in workmanship and materials for purpose for which the equipment is intended and under normal use and
maintenance service (the “Warranty”).
2.
This Warranty is in effect for two years (Leisure Use) or one year (Commercial and other Non-leisure Use) from the date of delivery/purchase by
the end user, with the following exceptions;
(a) For demonstration vessels, or vessels kept on the water, the dealer is considered as the end user from 6 months after their launch of the
vessel;
(b) The warranty period starts no later than 18 months after the fi rst launch of the vessel.
Please note that the boat manufacturer and dealer must pay particular attention to correct maintenance and service both by the products
manuals as well as general good practice for the location the boat is kept in the period the boat is in their care. In cases where the 6 and 18
months grace periods for boat builders and dealers are passed, it is possible to obtain a full warranty upon inspection and approval of the
warrantor or such representative.
3. Certain parts, classifi ed as wearable or service parts, are not covered by the warranty. A failure to follow the required maintenance and service
work as described in the product manual render all warranty on parts or components directly or indirectly affected by this void. Please also note
that for some parts, time is also a factor separately from actual operational hours.
4.
This Warranty is transferable and covers the equipment for the specified warranty period.
5. The warranty does not apply to defects or damages caused by faulty installation or hook-up, abuse or misuse of the equipment including
exposure to excessive heat, salt or fresh water spray, or water immersion except for equipment specifically designed as waterproof.
6.
In case the equipment seems to be defective, the warranty holder (the “Claimant”) must do the following to make a claim:
(a) Contact the dealer or service centre where the equipment was purchased and make the claim. Alternatively, the Claimant can make the
claim to a dealer or service centre found at www.sleipnergroup.com. The Claimant must present a detailed written statement of the nature
and circumstances of the defect, to the best of the Claimant’s knowledge, including product identifi cation and serial nbr., the date and place of
purchase and the name and address of the installer. Proof of purchase date should be included with the claim, to verify that the warranty period
has not expired;
(b) Make the equipment available for troubleshooting and repair, with direct and workable access, including dismantling of furnishings or similar,
if any, either at the premises of the Warrantor or an authorised service representative approved by the Warrantor. Equipment can only be returned
to the Warrantor or an authorised service representative for repair following a pre-approval by the Warrantor’s Help Desk and if so, with the
Return Authorisation Number visible postage/shipping prepaid and at the expense of the Claimant.
7.
Examination and handling of the warranty claim:
(a) If upon the Warrantor’s or authorised service Representative’s examination, the defect is determined to result from defective material or
workmanship in the warranty period, the equipment will be repaired or replaced at the Warrantor’s option without charge, and returned to the
Purchaser at the Warrantor’s expense. If, on the other hand, the claim is determined to result from circumstances such as described in section
4 above or a result of wear and tear exceeding that for which the equipment is intended (e.g. commercial use of equipment intended for leisure
use), the costs for the troubleshooting and repair shall be borne by the Claimant;
(b) No refund of the purchase price will be granted to the Claimant, unless the Warrantor is unable to remedy the defect after having a reasonable
number of opportunities to do so. In the event that attempts to remedy the defect have failed, the Claimant may claim a refund of the purchase
price, provided that the Claimant submits a statement in writing from a professional boating equipment supplier that the installation instructions
of the Installation and Operation Manual have been complied with and that the defect remains.
8. Warranty service shall be performed only by the Warrantor, or an authorised service representative, and any attempt to remedy the defect by
anyone else shall render this warranty void.
9.
No other warranty is given beyond those described above, implied or otherwise, including any implied warranty of merchantability, fitness for
a particular purpose other than the purpose for which the equipment is intended, and any other obligations on the part of the Warrantor or its
employees and representatives.
10. There shall be no responsibility or liability whatsoever on the part of the Warrantor or its employees and representatives based on this Warranty
for injury to any person or persons, or damage to property, loss of income or profit, or any other incidental, consequential or resulting damage or
cost claimed to have been incurred through the use or sale of the equipment, including any possible failure or malfunction of the equipment or
damages arising from collision with other vessels or objects.
11.
This warranty gives you specific legal rights, and you may also have other rights which vary from country to country.