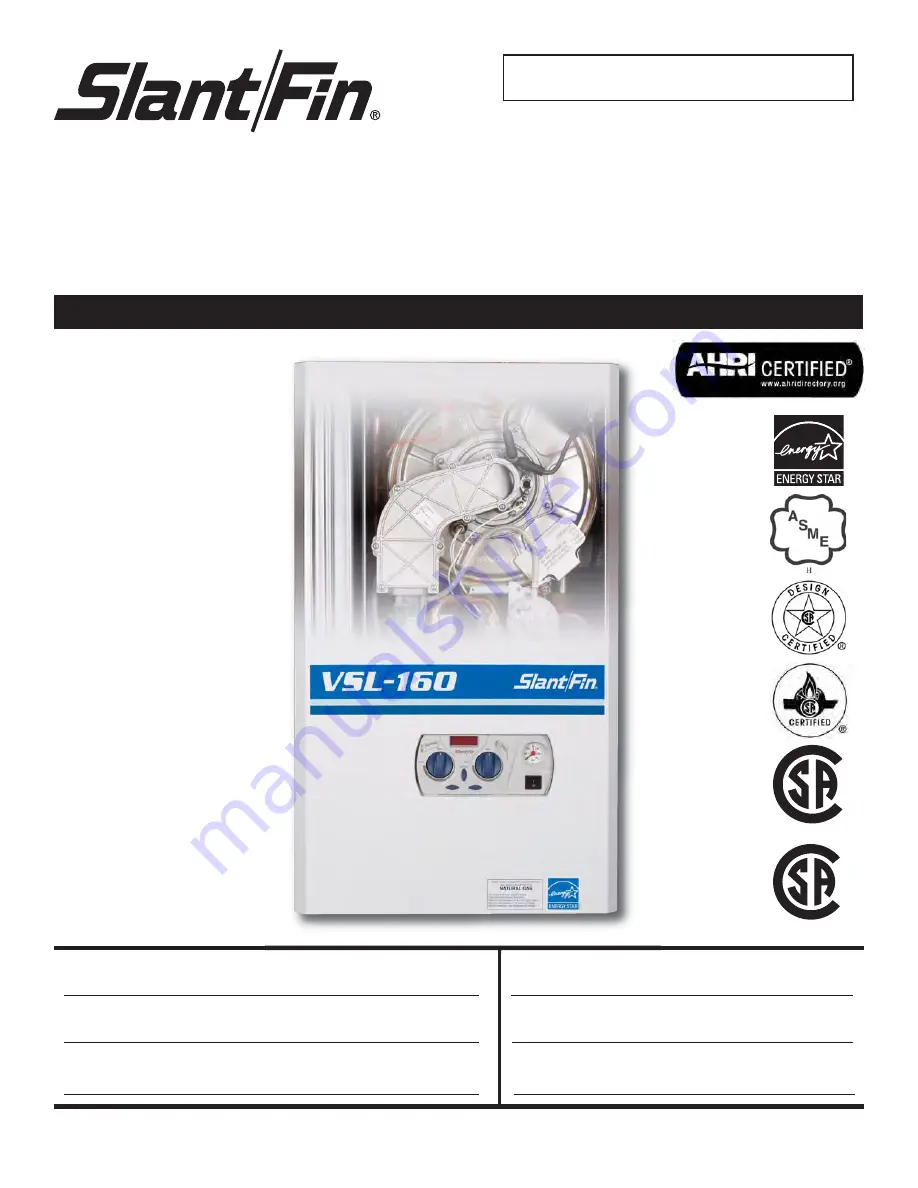
Part # 819506000-R00 Printed in U.S.A. 513 PUBLICATION VSL-40 rev.B
Heating Contractor
Address
Phone Number
Boiler Model Number
Boiler Serial Number
Installation Date
INSTALLATION INSTRUCTIONS
DIRECT-VENT SEALED COMBUSTION CONDENSING BOILER
HOT WATER MODEL VSL-160B & VSL-160C (COMBI BOILER)
GAS-FIRED BOILER FOR NATURAL AND L.P. PROPANE GASES
VSL Boiler
®
C
US
®
LLC
This manual must be left with owner and should be
hung on or adjacent to the boiler for reference.
Summary of Contents for VSL-160B
Page 3: ...3 SAFETY INSTRUCTIONS...
Page 95: ...95 14 MAINTENANCE...
Page 97: ...97 14 MAINTENANCE...
Page 99: ...99 16 SPARE PARTS...
Page 100: ...100 16 SPARE PARTS...
Page 101: ...101 16 SPARE PARTS...
Page 107: ...107 NOTE 62403559 R00 May 03 2012...