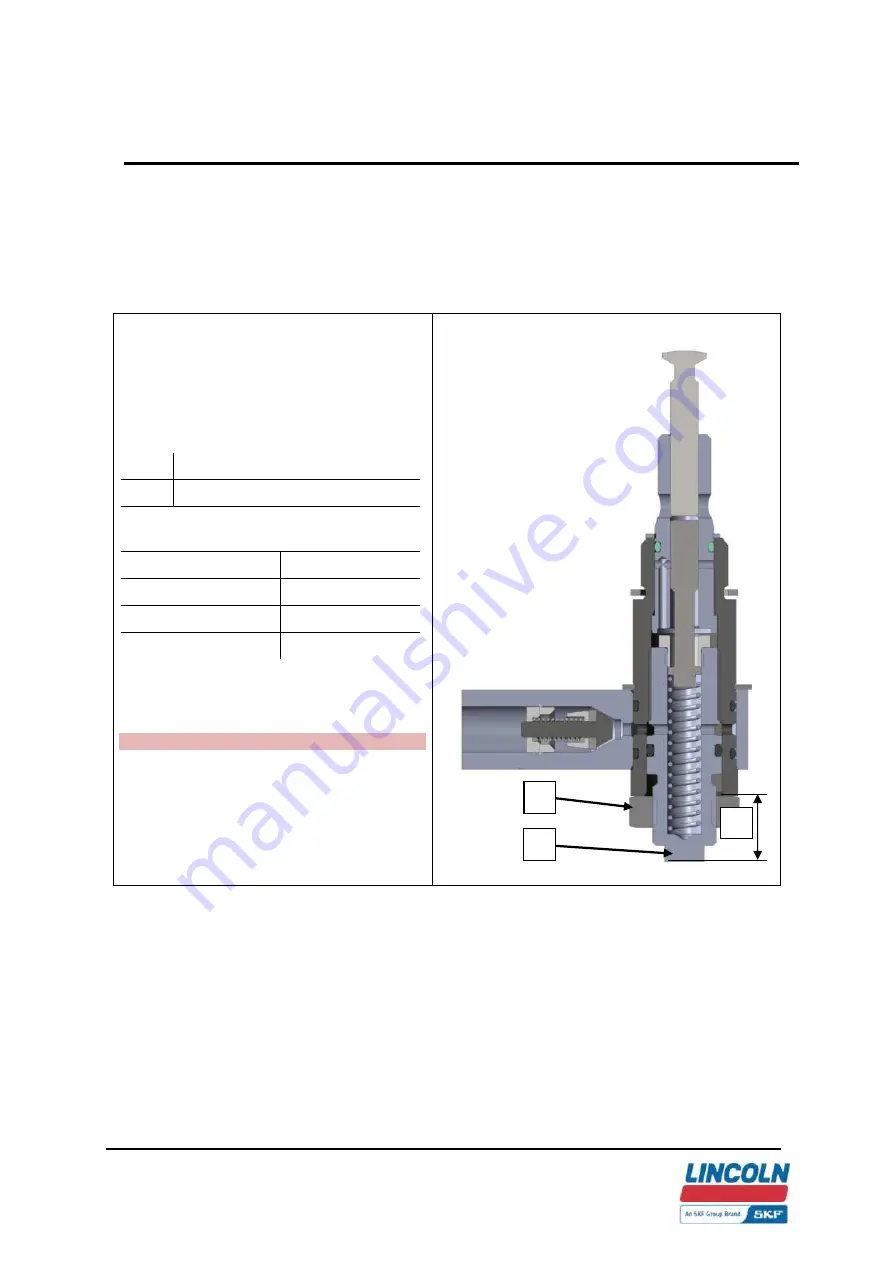
Installation Instructions
Pump P 215
810-55192-1
Page 29 / 45
Rev. 012
2018/11/30
8.4. Adjustment of the pump elements
NOTE:
The output of the pump elements can be
modified also during operation:
➢
Loosen counternut (1).
➢
In order to adjust the flow rate, turn
the spindle (2).
= lower flow rate
= higher flow rate
The measure R states the approximate
flow rate.
R = 22.0 mm
Full supply
R = 20.5 mm
¾ supply
R = 19.0 mm
½ supply
R = 17.5 mm
¼ supply
➢
After adjusting the flow rate, retighten
the counternut (1).
Tightening torque = 15 Nm
–
1 Nm
1
2
R
Summary of Contents for Lincoln 215-M049
Page 1: ...Installation Instructions Pump P 215 810 55192 1 Page 1 45 Rev 012 2018 11 30 P 215...
Page 23: ...Installation Instructions Pump P 215 810 55192 1 Page 23 45 Rev 012 2018 11 30...
Page 43: ...Installation Instructions Pump P 215 810 55192 1 Page 43 45 Rev 012 2018 11 30 M100 M049 100XY...