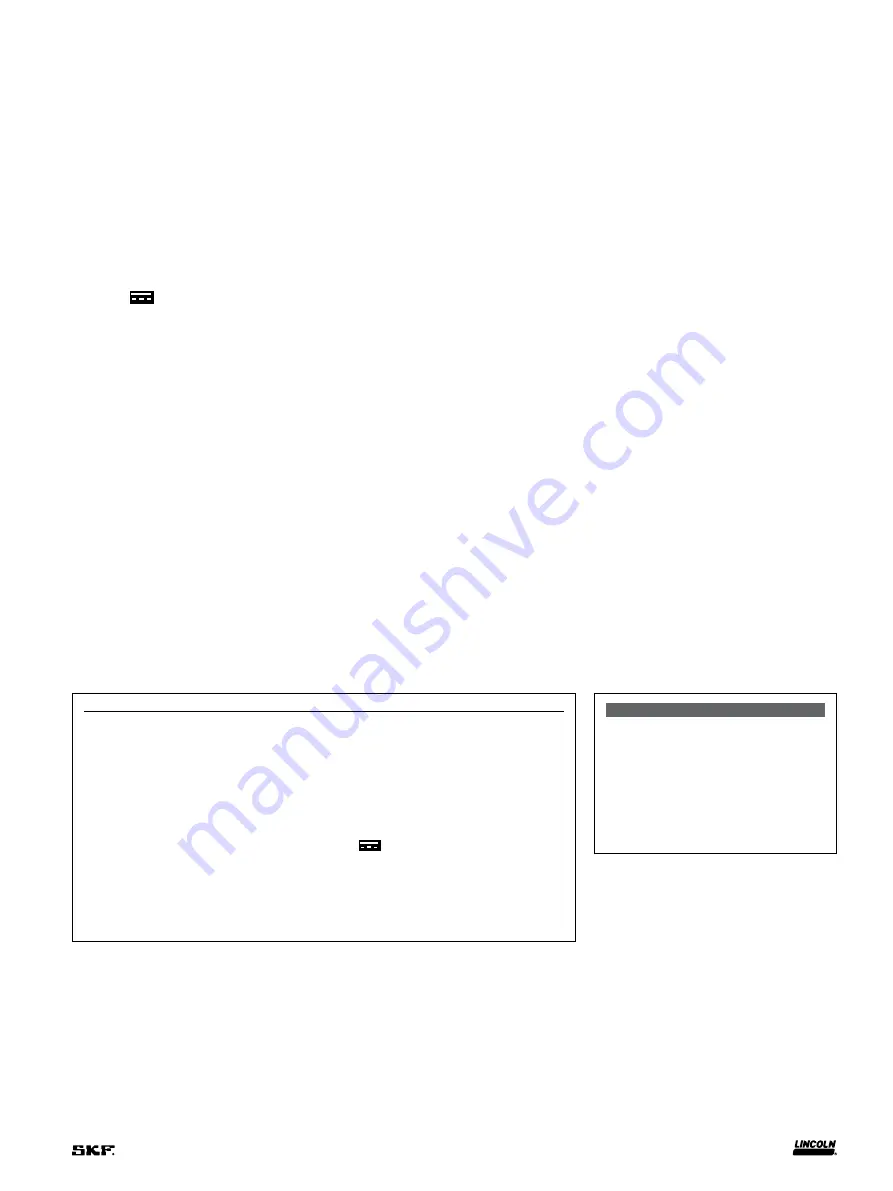
Description
General description
Model 85705 is a pumping unit designed to
operate a Centro-Matic lubrication system.
Unit includes a vent valve to relieve line
pressure to recharge injectors.
FlowMaster II rotary driven hydraulic
pump includes pressure reducing valve,
flow control valve and solenoid oper-
ated (24 V
) “on” and “off” valve.
FlowMaster II pump is fully automatic
when used with a controller and pressure
switch. Pump is double acting, dispensing
lubricant on both “up” and “down” strokes.
Unit is designed to be used with SL-V,
SL-V XL, SL-1, SL-11, SL-32 and SL-33
series injectors or a combination of these.
Model 85705 includes electronic
float switch.
Appropriate use
• Pump on this unit is exclusively designed
to pump and dispense lubricants using
hydraulic power only.
• Maximum specification ratings should not
be exceeded (
• Any other use not in accordance with
instructions will result in loss of claims for
warranty and liability.
WARNING
Do not exceed 3 000 psi
(207 bar)
maximum supply inlet hydraulic pressure
or 3 500 psi
(241 bar)
maximum outlet
pressure.
Exceeding rated pressures may result in
death or serious personal injury, and damage
to system components.
Table 1
Specifications
Supply inlet hydraulic pressure
Max 3 000 psi
(207 bar)
Operating working hydraulic pressure
400 psi
(28 bar)
Maximum output pressure
3 500 psi
(241 bar)
Hydraulic inlet flow
Up to 3.5 gal/min
(13 l/min)
Pump ratio with manifold
10:1
Ambient operating temperature
–40 to +150 °F
(–40 to +66 °C)
Operating voltage
24 V
Hydraulic inlet port
SAE 6 ORFS
Tank return port
SAE 8 ORFS
Maximum hydraulic fluid temperature
250 °F
(121 °C)
Container capacity
60 lbs
(27 kg)
System operation
Operation with
system controller
When system controller times out, a lubrica-
tion cycle is initiated. Solenoid is energized to
deliver hydraulic pressure to pump and vent
valve. Pump begins dispensing lubricant
through injectors to bearings.
When lubrication cycle has completed,
pressure rises in system to actuate pressure
switch. When pressure switch actuates,
control is reset to de-energize solenoid
valve, cutting off hydraulic oil pressure to
pump and vent valve. Pump stops, pressure
vents and pressure switch de-actuates.
Controller begins timing toward next
lubrication event.
3