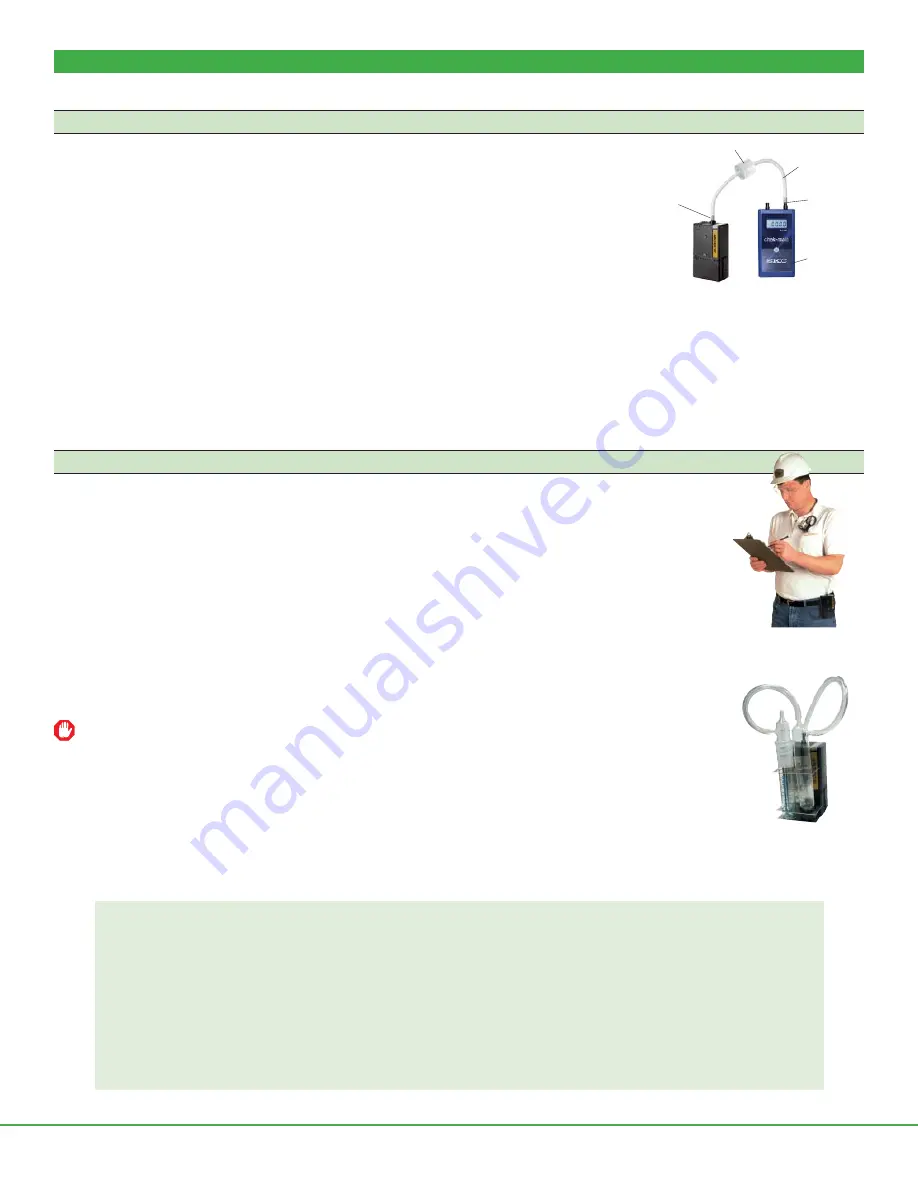
Form 37714 Rev 1809
Page 3 of 13
Operation
High Flow Applications (1000 to 3000 ml/min)
Set/Calibrate Flow Rate
• Allow pump to equilibrate after moving it from one temperature extreme to another.
• Charge battery completely before calibration and sampling.
1.
Ensure that the ba
tt
ery is fully charged and that the pump has run for
fi
ve minutes before
calibrating. Leave the pump running.
2. Prepare the calibrator.
See calibrator instructions
.
3. Set up a calibration train: Using
fl
exible tubing, connect the calibrator outlet (suction port)
to the representative sample medium inlet. Using ¼-inch Tygon tubing, connect the sample
medium outlet to the pump inlet.
See right
.
4.
Using a screwdriver, set the pump
fl
ow rate by turning the
fl
ow adjustment screw on top of the pump
(Figure 1)
,
clockwise
to increase
or
counterclockwise
to decrease
fl
ow, until the calibrator indicates the method-speci
fi
ed
fl
ow rate. Take a minimum of three readings
and record the average
fl
ow rate, as per OSHA/NIOSH instructions.
5. Press the on/o
ff
bu
tt
on to turn o
ff
the pump. Disconnect the calibrator and
fl
exible tubing from the representative sample medium
and proceed to
Set Up/Sample
.
Set Up/Sample
• Allow pump to equilibrate after moving it from one temperature extreme to another.
• Protect sample pump from weather when sampling outdoors.
• Powering the pump with any device other than the approved battery pack voids the UL Listing for intrinsic safety.
• Do
not
use the pump with the Battery Eliminator in hazardous locations. UL Listing for intrinsic safety is not in effect
during pump operation with Battery Eliminator.
• Use of any device other than the approved battery pack or Battery Eliminator to power the pump voids any warranty.
• Charge battery completely before calibration and sampling.
1. Replace the representative sample medium with new unexposed medium for sample collection.
2. Place the sample medium where appropriate for sampling.
a. For
personal sampling,
clip the sample collection medium to the worker in the breathing zone and the
pump to the worker’s belt using the belt clip.
When using an impinger, an in-line trap (SKC Cat. No. 225-22 or 225-22-01) is required between the pump and
impinger to prevent fumes from accidentally being drawn into the sampler. Failure to use an appropriate in-line
trap during impinger sampling voids any warranty.
b.
For sampling with an impinger,
mount the single or dual impinger and trap (SKC Cat. No. 225-20-01 or
225-20-02) to the face of the sampler using the accessory mounting screws
(Figure 1)
or place them in a
holster at the worker’s waist.
3. Press the on/o
ff
bu
tt
on to clear the elapsed time displayed on the LCD and to start sampling. Record the
start time and other pertinent information. The LCD will automatically display elapsed pump run time.
See below.
Possible Displays During Sampling
Flow or Ba
tt
ery Fault Shutdown -
If the pump is unable to compensate due to excessive back pressure or a low ba
tt
ery
condition exists, it will shut down and timing functions will pause. The LCD will display either a ba
tt
ery-shaped icon
or a
fl
ow fault icon (
) depending on the cause of the shutdown. Upon
fl
ow fault, the pump will a
tt
empt to restart up
to
fi
ve times. To restart from
fl
ow fault, correct the blockage and press the on/o
ff
bu
tt
on twice.
The elapsed run time
display will reset to 0 when the pump is restarted.
If the ba
tt
ery icon is displayed, recharge the ba
tt
ery before sampling.
Displayed Elapsed Run Time -
Elapsed run time is displayed continuously on the LCD. For elapsed times after 999
minutes, the display still shows elapsed time but alternates between displaying the
fi
rst two digits of the elapsed time
and the last three digits. For example, a pump that has run for 1,440 minutes would display
fi
rst “01” and then “440.”
The display maximum is 99 999, which is 99,999 minutes.
4. At the end of the sampling period, press the on/o
ff
bu
tt
on and record stop time and other pertinent information.
chek-mate
Calibrator
Sample medium
Tygon
tubing
Calibration train with
fi
lter cassette
Pump
inlet
Suction
port
Clip sample medium
to worker and pump
to belt.
Impinger holder on pump
with impinger and trap