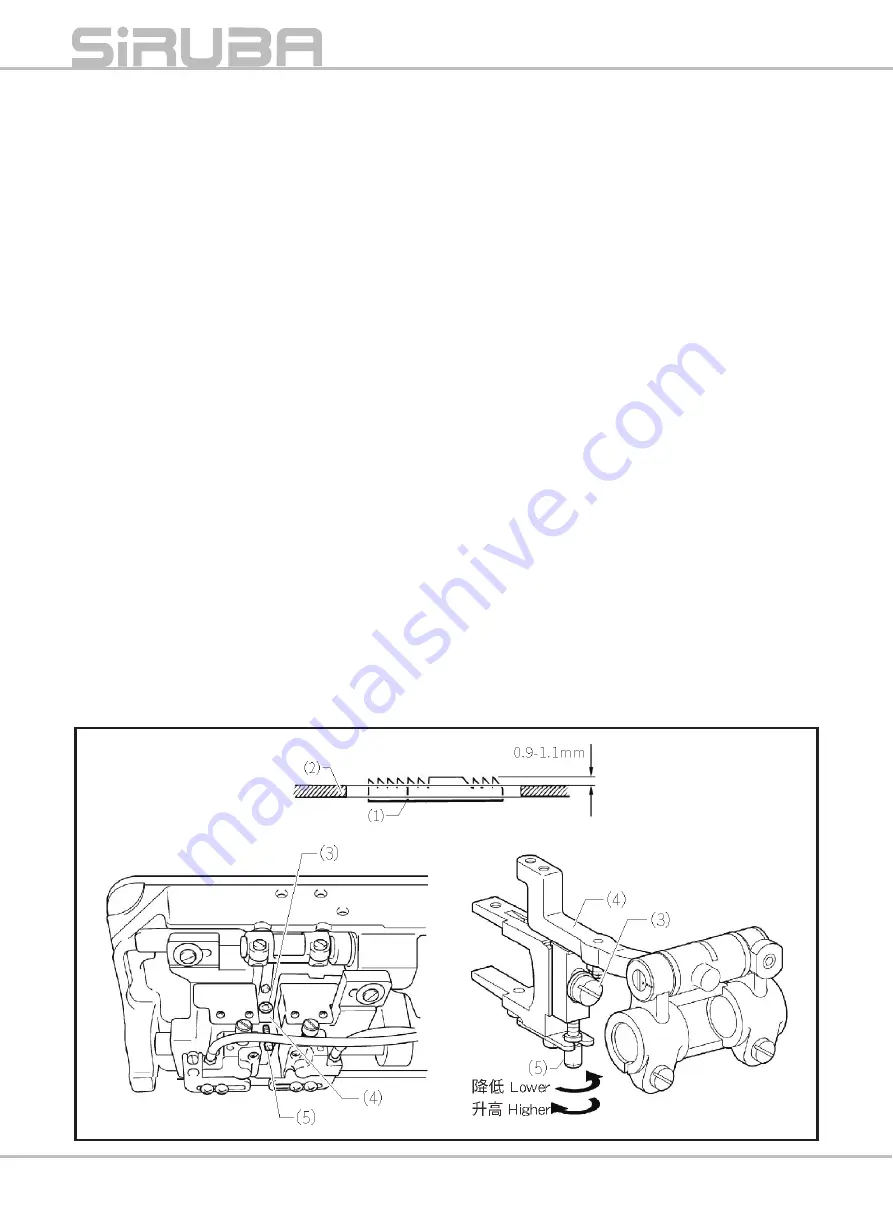
Feed dog height
Turn the machine pulley forward until the feed dog (1) is at
its highest position, and then adjust so that the feed dog (1)
protrudes 0.9-1.1 mm from the top of the needle plate (2)
1.Tilt back the nachine head
2.Loosen the screw (3) just enough so that the feed bar (4) can
slide
3.Turn the height adjustment screw (5) as shown in the illustration
to adjust the height of the feed dog (1)
4.Securely tighten the screw (3)
5.Recheck the height of the feed dog (1)
※
If the feed is too high
●
The feed dog may touch the needle plate
●
The stitch length may become longer than the stitch length dial
setting
●
Thread tightening may be poor when using thick threads
●
It may be difficult to obtain uniform stitch lengths for normal
feed and reverse feed
●
Lower thread trimming errors may occur
※
If the feed is too low
●
The stitch length may become shorter than the stitch length dial
setting
●
It may be difficult to obtain uniform stitch lengths for normal
feed and reverse feed
●
The feed dog may touch the movable knife
●
Large variations in stitch length may occur at slow and fast
sewing speeds
送布⽛的高度
轉動手動輪,送布⽛(
1
)上升到最高位
置,此位置進行調整,使送布⽛(
1
)距
針板(
2
)上面
0.9-1.1mm
1.
放下縫紉機頭
2.
將螺釘(
3
)旋松一點,使送布台(
4
)
能滑動即可
3.
轉動高度調節螺釘(
5
),調節送布⽛
(
1
)的高度
4.
將螺釘(
3
)擰緊
5.
再次確認送布⽛(
1
)的高度
※ 送布⽛過高的情況
●送布⽛會碰到針板
●針跡長度會⽐實際針距大
●用粗線時,線鬆緊不良
●正送布與倒送布的線跡長度難能一致
●可能發生底線切線錯誤
※ 送布⽛過低的情況
●針跡長度會⽐實際針距小
●正送布與倒送布的線跡長度難能一致
●送布⽛碰動刀
●低速和高速縫紉的線跡長度差變大
P26
Summary of Contents for DT828L
Page 1: ...DT828L INSTRUCTIONS BOOK PARTS LIST...
Page 21: ...1 1 1 2 1 1 2 1 1 1 1 1 2mm A B 3 A 3 3 B P15...
Page 35: ...P29...
Page 45: ...P39...