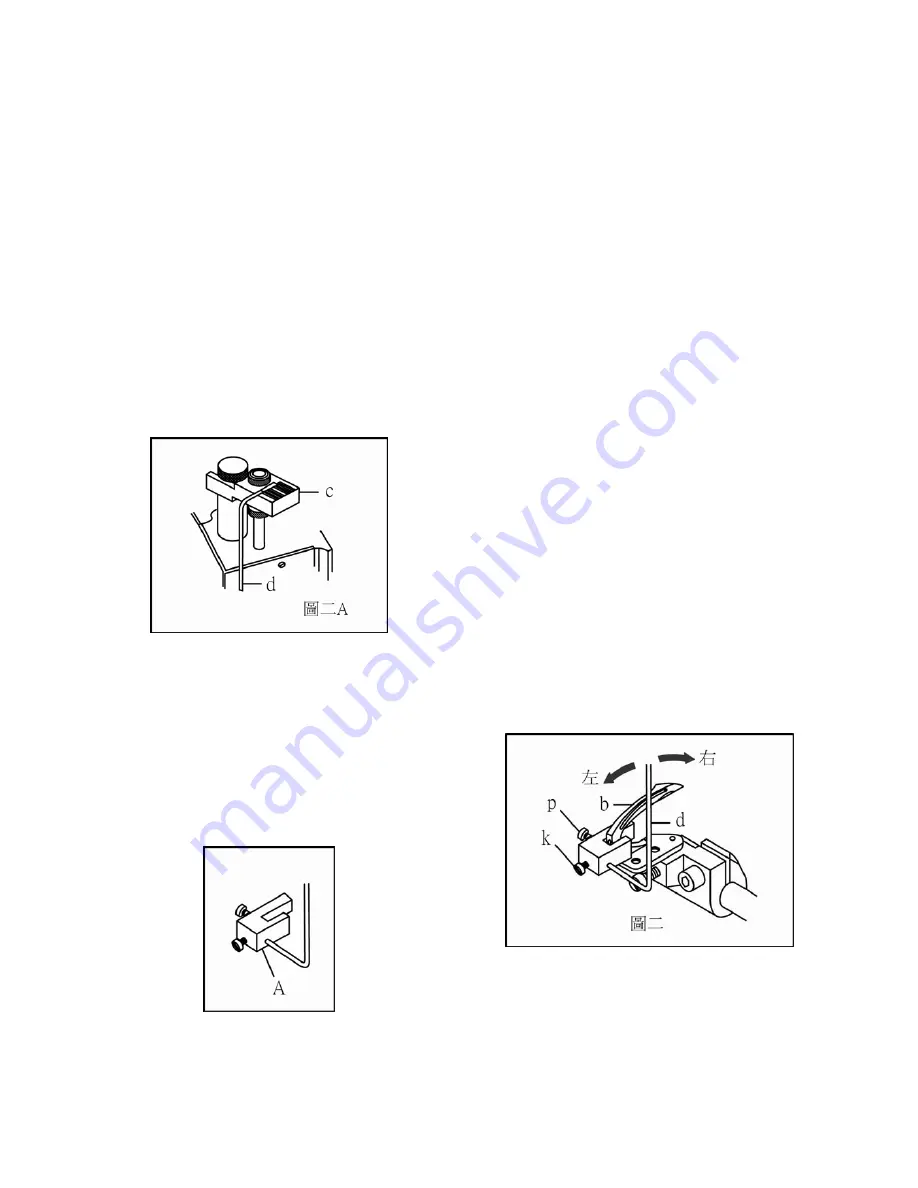
-20-
3-6-3
組裝指針組
A
於下飾線勾針
b
上,將螺
絲
p
鎖緊,同時調整指針
d
的尖端指在刻度量
具
c
的刻度上,再將螺絲
k
鎖緊,旋轉手輪,
向左擺動當針柱
a
頂到止塊螺絲
h
時,注意指
針
d
所指示的刻度;當再旋轉手輪,向右擺動
到同樣位置時檢查指針
d
,是否位於前述情形
位於同一個刻度上
(
圖二
)
。
3-6-4
將指針左右擺動於同一刻度上的調整
方法,由前後軸連接襯套
g
鬆開螺絲
e
進行調
整
(
圖三
)
。
刻度量具
c
:零件本校車定規
K13-11
(ERP NO.07401311)
指針組
A
:零件本校車定規
K13-10
(ERP NO.07401310)
指針
d
:零件本校車定規
K13-1
(ERP NO.07401301)
3-6-3 Please install the measuring gauge
pointer set “A” on the looper “b” and
tig
hten it by
screw ”p”. In the mean
ti
me, please adjust the
tip
of pointer “d” to the scale of measuring gauge “c”
and
tig
hten it by screw ”k”. To turn the
handwheel and move the pointer “d” to the le
ft
till
the top of needle bar push the stop screw “h”.
Please make a noted of the scale of pointer “d”. In
the other way, to move the pointer “d” to the
right and make sure it to indicate in the same
scale or not?? (Fig 2)
3-6-4 Please loosen the screw “e” on the front
& rear co
nnecting
sleeve “g” for adjus
ting
the
pointer “d” to locate at same scale. (Fig 3)
Measuring gauge “c”: K13-11 in spare parts book.
(ERP NO.07401311)
Measuring gauge pointer set “A”: K13-10 in spare
parts book. (ERP NO.07401310)
Pointer “d”: K13-1 in spare parts book.
(ERP NO.07401301)