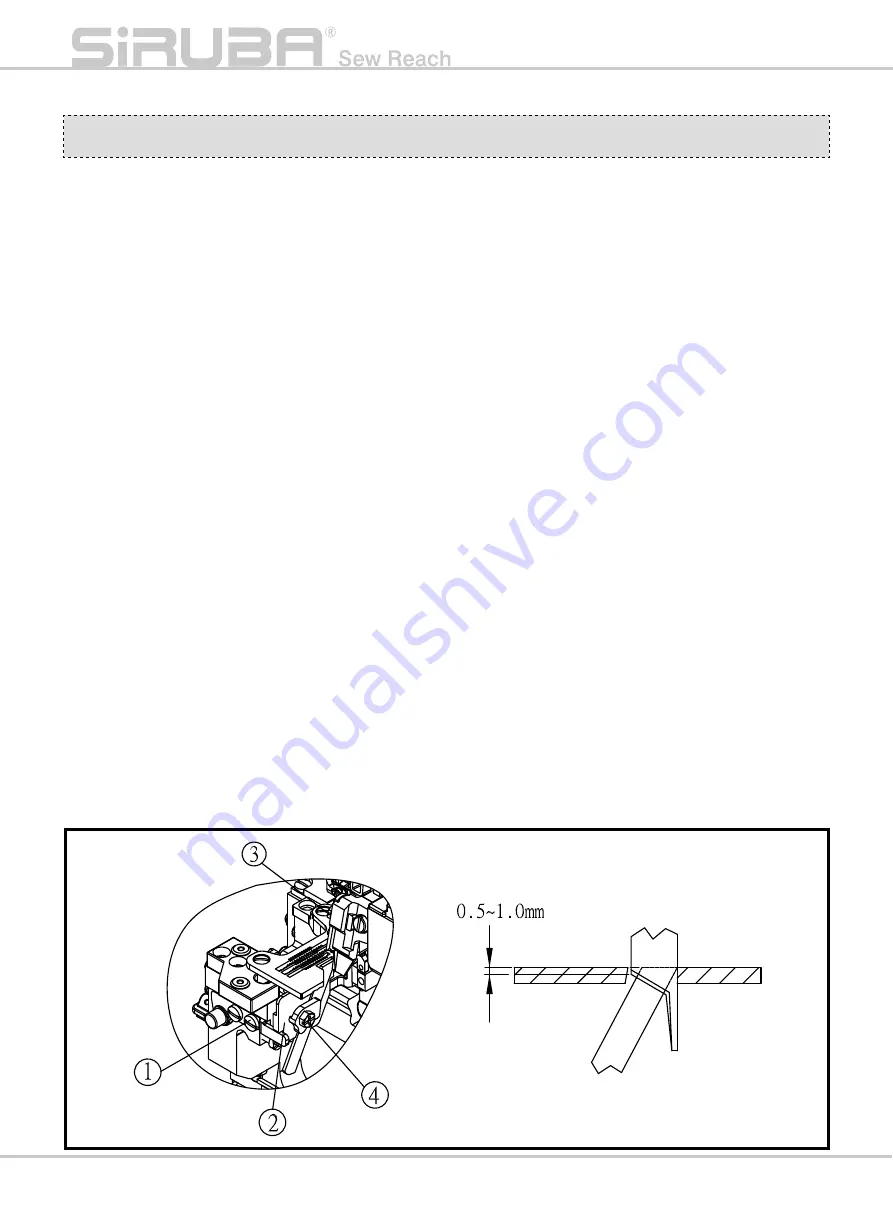
圖
29 / Fig. 29
更換切刀
REPLACE THE TRIMMERS
1.
更換上切刀
(1)
放鬆螺絲①將下刀座②向左邊推,輕鎖螺絲
①
。
(2)
取下螺絲③換上新刀片後,輕輕鎖緊螺絲③
。
(3)
轉動皮帶輪使上刀移至下死點,調整上刀高
低使上刀與下刀相交約
0.5~1.0mm
,鎖緊
螺絲。
(4)
放鬆螺絲①使下刀座還原位置,並試驗上下
刀能確實剪斷車縫線,鎖緊螺絲
①。
2.
更換下切刀
(1)
放鬆螺絲①將下刀座②向左邊推,輕鎖螺
絲。
(
圖
29)
(2)
放鬆螺絲④取下舊刀換上新刀。
(3)
調整下刀之刀口與針板面平齊後,鎖緊螺絲
④。
(4)
放鬆螺絲①使下刀座還原位置並試驗上下刀
能確實剪斷車縫線,鎖緊螺絲①。
(
圖
29)
1.Replace the upper trimmer:
(1)Loosen the screw
①
and move the lower
trimmer holder
②
to the left. Then, tighten
the screw
①
a little.
(2)Remove the screw
③
and put the new
trimmer. Then, tighten the screw
③
a little.
(3)Turn the pulley to move the upper trimmer to
the lower dead point. Adjust the height of
the upper trimmer so that the upper trimmer
can cross the lower trimmer about 0.5 ~
1.0 mm. After that, tighten the screw .
(4)Loosen the screw
①
and return the lower
trimmer to its original position. Test if the
upper and the lower trimmer can cut the
thread exactly, and then tighten the screw
①
.
2.Replace the lower trimmer:
(1)Loosen the screw
①
and move the lower
trimmer holder
②
to the left. Then,tighten
the screw
①
a little.(Fig. 29)
(2)Loosen the screw
④
. Take off the trimmer
and replace a new one.
(3)Adjust the edge of the lower trimmer to be
alight with the surface of the needle plate.
Then, tighten the screw
④
.
(4)Loosen the screw
①
to return the lower
trimmer holder to its original position and
test if the upper and the lower trimmer can
cut the thread exactly. Then, tighten the
screw
①
.(Fig. 29)
P23
Summary of Contents for 700KT
Page 1: ...700KT INSTRUCTION BOOK PARTS LIST...
Page 2: ...i...
Page 4: ...h Consider environment s safety may be caught in moving parts Wear object cause 1 P1...
Page 5: ...2 P2 Introduction...
Page 7: ...P4 Introduction...
Page 8: ...5 P5...
Page 9: ...6 P6 Introduction...
Page 10: ...7 ground P7...
Page 39: ...P36...
Page 40: ...P37...
Page 41: ...P38...
Page 42: ...P39...
Page 43: ...P40...
Page 44: ...P41...
Page 45: ...P42...
Page 46: ...P43...
Page 47: ...P44...
Page 48: ...P45...
Page 49: ...P46 SK4306 2 SK4306 2 KJ01J E KJ01J E KJ01J...
Page 50: ...P47 SK4306 2 SK4306 2 KJ01J KJ01J E KJ01J E...
Page 51: ...P48...
Page 52: ...P49...
Page 53: ...P50...
Page 54: ...P51...
Page 55: ...P52...
Page 56: ...P53...
Page 57: ...P54...
Page 58: ...P55...
Page 59: ...P56...
Page 60: ...P57...
Page 61: ...P58...