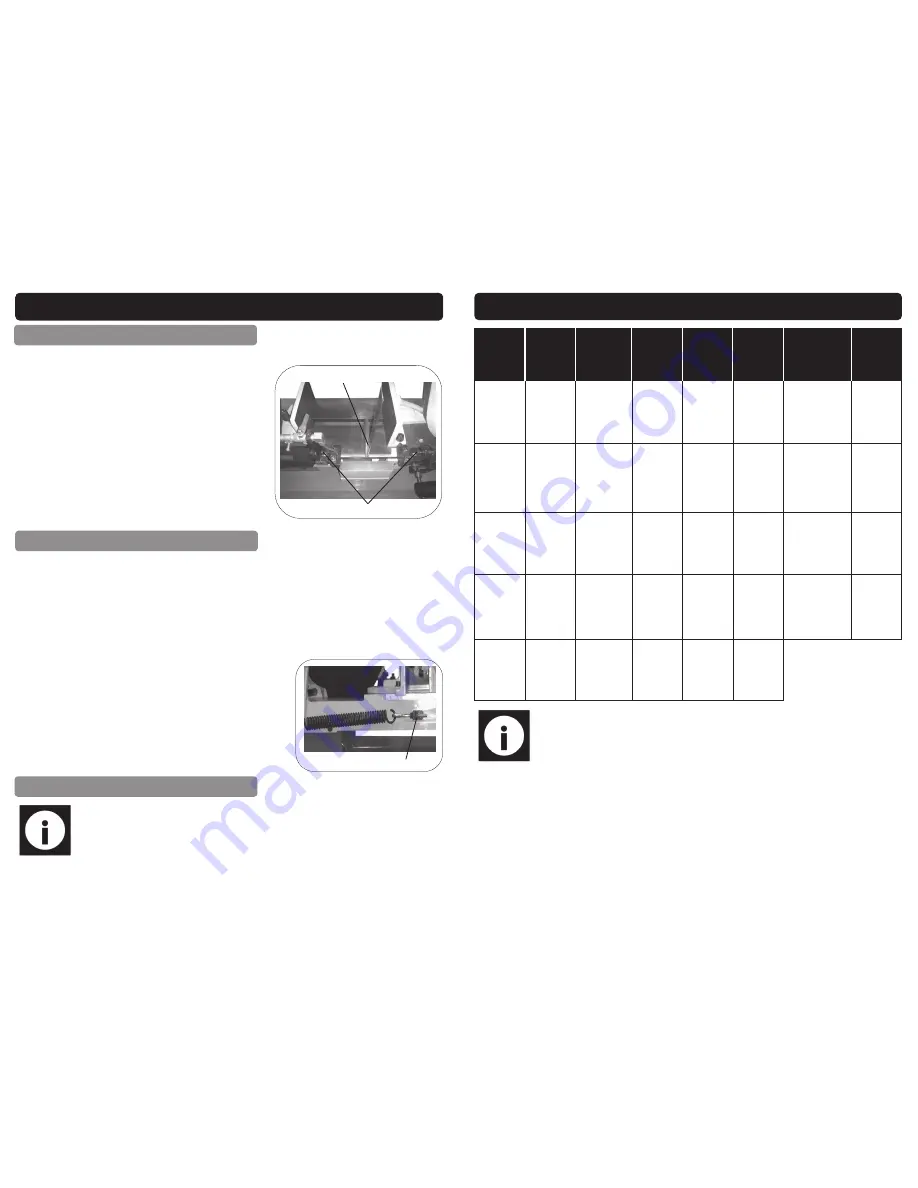
22
MAINTENANCE INSTRUCTIONS….cont
SETTING THE BLADE SQUARE TO THE BED AT 90
˚
1.Ensure the bow is at its lowest position.
2.Disconnect from the mains supply.
3.Place an engineer`s set square onto the bed
and touching the blade (Fig.12).
4.If any adjustment is needed then loosen the two
cap head bolts (Fig.12,A).
5.Rotate both blade guides in the required direc-
tion until the blade makes contact with the set
square along the entire width of the blade.
6.Once set correctly, re-tighten both cap head
bolts.
7.The blade guide bearings may need to adjusted.
Fig.12
A
Set square
Note:
The correct guide bearing adjustment is very important, this will
make the blade run smoother and evenly without any snagging or twisting
whilst the blade is running. It will also prolong the blade life.
BLADE GUIDE BEARING ADJUSTMENT
The bow weight is one of the most important adjustments on the saw. If the bow
weight is set incorrectly then expect poor performance, crooked cuts, teeth stripping
from the blade, stalling and the blade coming off the blade pulleys. The hydraulic
cylinder feed rate will not compensate for improper bow weight. A new machine will
have the bow weight pre-set, if you need to adjust the bow weight then follow the
steps below.
1.Disconnect the mains from the supply.
2.Ensure the bow is at its lowest position.
3.Turn the hydraulic cylinder knob anti-clockwise until it
stops.
4.Place a scale on the Blade tensioning knob, lift the
saw bow up, the scale should read between 5-6kgs.
5.If it doesn't then adjust the tension nut (Fig.7,A) until it
reaches between 5-6kgs.
A
Fig.7
ADJUSTING THE BOW WEIGHT
15
OPERATING INSTRUCTIONS….cont
Material
Speed
M/Min
(FPM)
Material
Speed
M/Min
(FPM)
Material
Speed
M/Min
(FPM)
Material
Speed
M/Min
(FPM)
Carbon
steel
60 - 108
(196 - 354)
Tool steel
62
(203)
Alloy steel
34 - 98
(111 - 321)
Free
machining
stainless steel
46 - 62
(150 - 203)
Steel
section
54 - 67
(180 - 220)
High speed
tool steel
23 - 36
(75 - 118)
Mold steel
75
(246)
Gray cast iron
33 - 75
(108 - 255)
Thin tube
54 - 67
(180 - 220)
Cold work
tool steel
95 - 213
(29 - 65)
Water
hard
tool steel
242
(74)
Ductile
austenitic cast
iron
65 - 85
(20 - 26)
Aluminium
alloy
67 - 163
(220 - 534)
Hot work
tool steel
62
(203)
Stainless
steel
26
(85)
Malleable cast
iron
98
(321)
Copper
alloy
70 - 147
(229 - 482)
Oil
hardening
tool steel
62 - 65
(203 - 213
Cold
rolled
stainless
Steel
26 - 62
(85 - 203)
Note:
The above table is an approximate guide reference only, various
factors mean some materials may require different speeds to the ones
quoted.