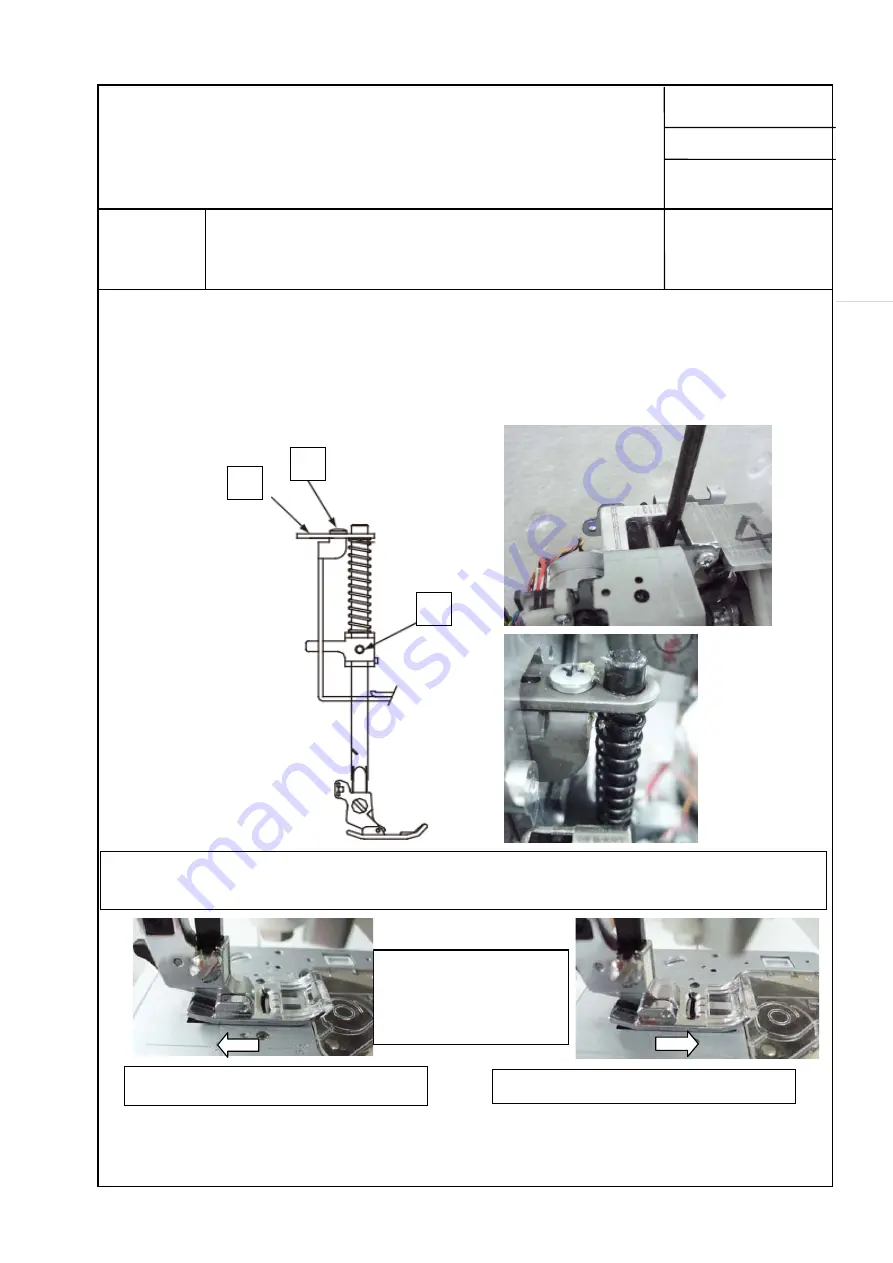
Service Manual
Original issue
May 2014
Page
17/64
Model
XL-420
| 17
SEC.5-3 Presser foot height and direction (3)
Adjustment-2
When needle ditch on the presser foot and needle hole at the needle plate do not match
towards fabric feed direction.
1.
Insert screw driver as shown on picture below and loosen screw (D) at the upper
part of needle bar bracket (C)
2.
After adjustment, tighten screw (D) securely and check to see whether presser foot
is operated smoothly with presser foot lever.
Shift presser foot backward to adjust.
Please note that parts of needle bar driving unit are removed in order to explain upper part (C)
and screw.
C
D
B
Shift presser foot forward to adjust
Note: The presser foot
shown in this picture is
not for FQ-4