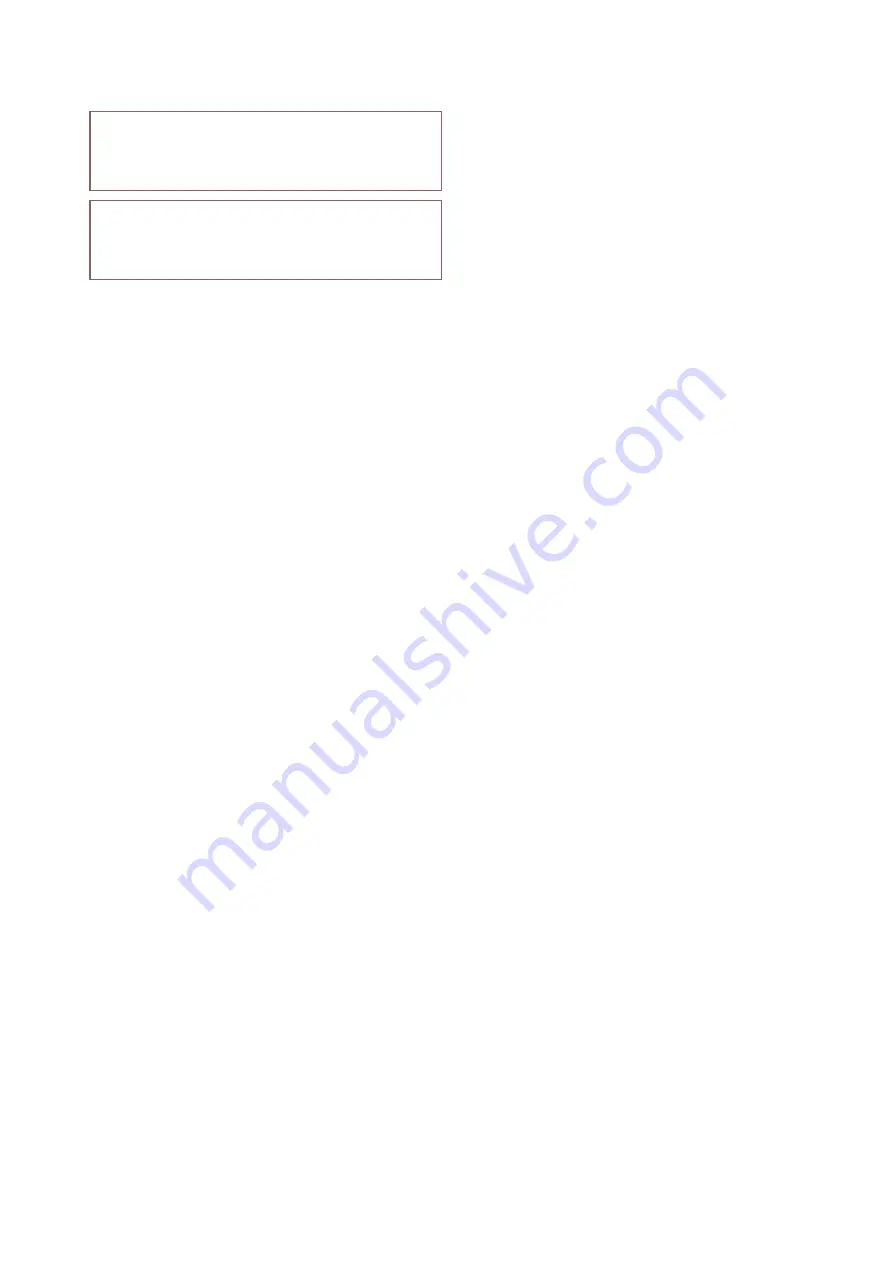
5
8.2
5.1.6
Longer Studs
For thicker than standard decks, simply fit longer studs as
appropriate (Thread M8 x 1.25). Studs to special lengths may
be obtained from Simpson-Lawrence Engineering Limited.
5.2.0
Wiring
5.2.1
General Recommendations
Warning! Carefully check to ensure that the capstan motor is
wired to correct polarity. It is possible to damage the gearbox
if the motor is wired to the wrong polarity.
The wiring system should be of the two cable fully insulated
return type, which avoids possible electrolytic corrosion
problems. Most modern installations are negative return
(negative earth) but polarity should be checked.
Solenoids should be mounted as close to the battery as
possible, in a dry location using the mounting holes provided.
Under no circumstances should solenoids or solenoid control
boxes be installed in chain lockers or similar damp or semi
exposed areas.
Overload protection must be built into the capstan wiring
circuit. This protects the wiring and prevents undue damage to
the capstan motor, in the event of it being stalled by an
excessive load in service. It is advisable to site the Breaker/
Isolator in a dry, readily accessible place, as it must be
manually reset should an overload occur that causes it to trip
to the OFF position.
If you are NOT using the Breaker/Isolator recommended, an
alternative MUST have identical characteristics.
NB:
Crimp terminals should be used on all wire ends for good
electrical connections.
5.2.2
Control Switch Installation
Follow the mounting instructions supplied with the switch.
Remember when using more than one control switch, it is
important to their correct operation, that they are wired in a
parallel circuit.
5.3
Test
Immediately after installation, it is recommended that the
capstan is tested to ensure it functions correctly in all modes,
e.g., forward, reverse and manual operations should be tested.
5.4
Protection of Below Deck Parts
Check all terminals or connections are firmly secured. Coat
ALL below deck surfaces, including the terminals, with rubber
or plastic type paint (automotive underseal is one convenient
way) OR wrap completely in self amalgamating tape OR coat/
protect in a similar way with some other system suitable for a
marine environment.
4.0
SPECIFICATION
4.1
Performance Data:
Typical Working Figures (12V/24V) Warping
Load
Speed
Current Draw
110kg(220lb)
8.0m(26ft)/min
80 Amp - 12V
110kg(220lb)
8.0m(26ft)/min
40 Amp - 24V
Typical Working Figures (12V/24V) Anchoring
Load
Speed
Current Draw
110kg(220lb)
18.0m(59ft)/min
80 Amp -12V
110kg(220lb)
18.0m(59ft)/min
40 Amp - 24V
Motor
4 Pole Permanent Magnet
Weight
10kg (22lb)
5.0
INSTALLATION
5.1.0
Fitting Capstan To Deck
5.1.1
Preparation
The capstan must always be mounted vertically. DO NOT
mount capstan in a horizontal direction as oil will leak from the
gearbox and the capstan will wear out prematurely. If the deck
top is uneven a suitable mounting pad may be required to take
up camber or sheer. Decks which are thin, of foam or balsa
laminate construction, will require a backing piece in order to
spread the load which will be applied locally to the deck while
the capstan is in use. Care must be taken if the deck is of
uneven thickness and a mounting pad and/or backing piece
fitted that the top and bottom surfaces are parallel for optimum
clamping.
5.1.2
Position of Capstan
Select a site for the capstan on the deck that is a comfortable
position for the operator to tail rope off the drum and preferably
feed rope straight into the storage area. A position for the
switch should be found that makes it accessible to the capstan
operator’s foot or knee.
5.1.3
Access
Allow for access to the top of the drum during maintenance.
5.1.4
Mounting Template
Place the mounting template in the desired position. Drill a
clearance hole for the motor to pass through as detailed and
six 10mm (3/8") holes for the studs. The studs supplied suit
decks and mounting pads up to 75mm (3") thickness.
5.1.5
Fitting
Place the capstan and studs through the holes in the deck,
when satisfied that all is correct, fit any packing, the clamping
ring, the nuts and washers, and tighten evenly and firmly using
a 150mm (6") long spanner.