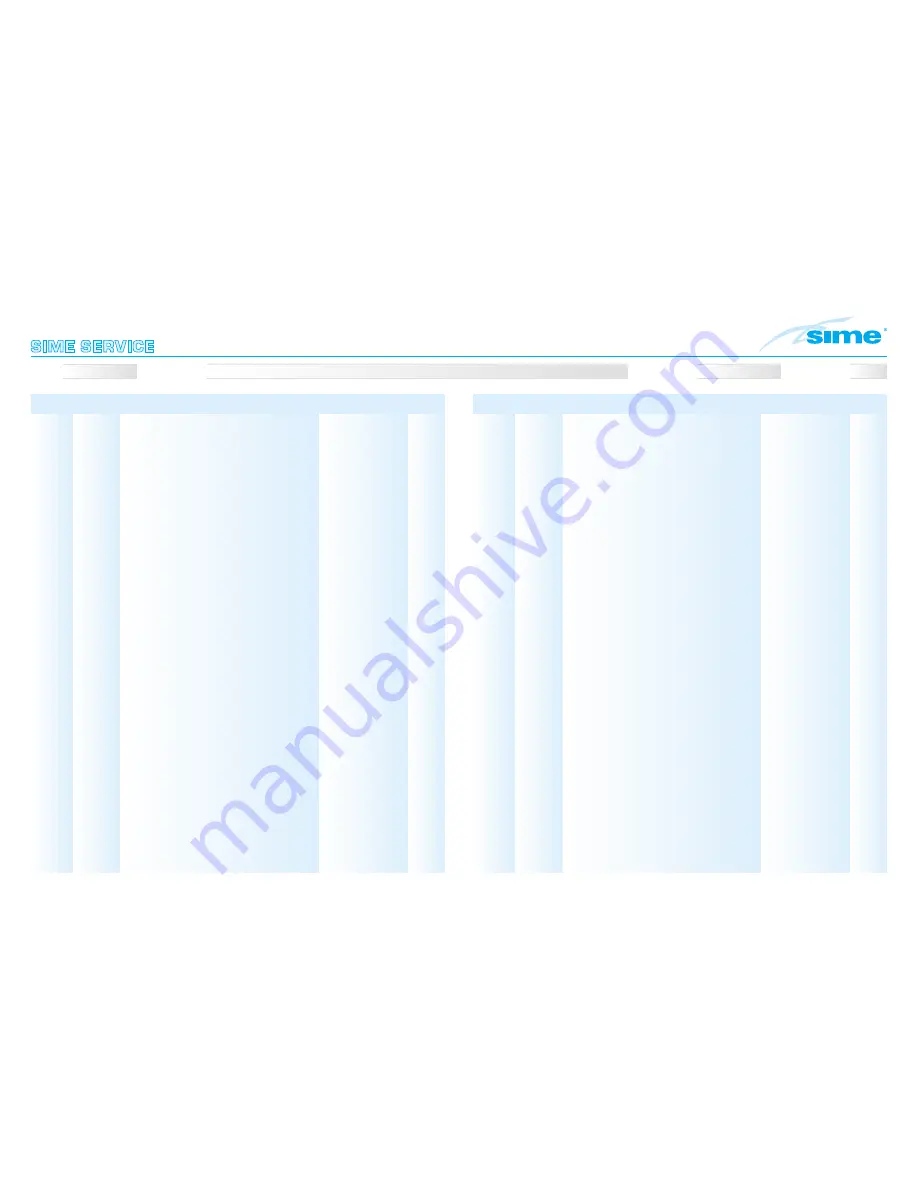
Fonderie Sime S.p.A. - Via Garbo, 27 - 37045 Legnago (Verona) - Tel. +39-0442 -631111 - Fax +39-0442-631292 - www.sime.it
POSITION
CODE
DESCRIPTION
MODEL
NOTE
COD.
TYPE
DATE
PAGE
• Recommended stock parts - Componenti da tenere a scorta
POSITION
CODE
DESCRIPTION
MODEL
NOTE
57
6226607 Pipe fixing spring
58
• 6272300 Circulating pump CP 53 Myson motor
80C
58 A • 6272301 Circulating pump VA 55 Dab motor
80C
58 B • 6272302 Circulating pump CP 63 Myson motor
100C
59
• 6226416 O-ring Ø 75,87x2,62 for Myson
59 A • 6028705 Gasket EP709 for Dab
80C
60
6281520 OR for Myson pump
60 A
6281521 OR for Dab pump
80C
61
2000201 Screw M5x40
62• 60402
01 Pressure relief valve
63
6288200 Sealed chamber side panel
64
• 6280510 3-ways junction
65
• 5192100 Air pressure switch
66
2013304 Fastener for self tapping screw
67
• 6243810 SIT gas valve type 845 SIGMA
68
6226856 Gas inlet pipe
69
6226945 Pipe connecting gas valve-main burner
70
2030228 Gasket Ø 17x24x2
71
6146302Brass nut 3/4”
72
2030227 Gasket Ø 12x18x2
73
6289800 Control panel
74
6273210 Guidelight - 2 ways out
75
6217005 Temperature and pressure gauge
76
• 6230687 Main PCB with ignition
77
• 6201501 Trimmer spindle Ø 5
78
• 6201505 Trimmer spindle Ø 6
79
• 6260701 Rotary switch
80
2211610
Earth faston
81
• 6098304 Ignition transformer
8262
89900 Control panel protecting cover
83
6290300 Control panel cable cover
84
6290200 Room stat connection cover
85
6290100 Knob Ø 40
86
6009585 Control panel bracket
87
6290001 Flap door
80C
87 A
6290002 Flap door
100C
88
• 6131401
Microswitch for flowmeter
89
5191900 Divertor valve micro support
90
6226605 Fixing spring
91
2051100 Retaining spring
9262
88350 Sealed chamber front panel
80C
92A
62
88360 Sealed chamber front panel
100C
93
6001210 Peephole
94
6287321 Casing
80C
94 A
6287331 Casing
100C
95
• 2013302 Fastener for self tapping screw
96
2004510 Screw 8Px7/8”
97
6112420
Control panel screw
98
6028624 Air diaphragm Ø 87.5
99
5192200 Gasket for sealed chamber
100
6263905 Fan pressure test point
101
6223351 Venturi
80C
101 A
6223352 Venturi
100C
102• 6197709 Time programmer
103
6142330 Quarter bend 1/2” x 15
103 A
6147231 Straight fitting 1/2” Ø 15
LPG
104
6177505 Ball cock 3/4” x 22
104 A
6245000 Ball cock 3/4”
LPG
105
6177506 Ball cock 1/2” x 15
105 A
6245001 Ball cock 1/2”
LPG
106
6177504 Gas cock 1/2” x 1/2”
106 A
6063601 Gas cock 1/2”
LPG
107
6157602Pressure relief valve drain pipe
5191110
Complete control panel
6127210
Main cable L=2000
6245335 845 Sigma gas valve connector
6278671 6 pole LUMBERG cable connector
6278673 6 pole Stocko cable connector
6278674 8 pole STOCKO cable connector
6278675 5 pole STOCKO cable connector
6278688 10 pole LUMBERG cable connector
• 5144712Conversion kit to LPG
80C
• 5144713
Conversion kit to LPG
100C
• 6233506 Fuse T1,6A 250V
• 6281506 O-ring kit for hydraulic group
3820044/528
FORMAT C UK
12.09.2001
3/4
Summary of Contents for Murelle 25 BF
Page 24: ...Format C installation and servicing instructions...
Page 53: ...26...