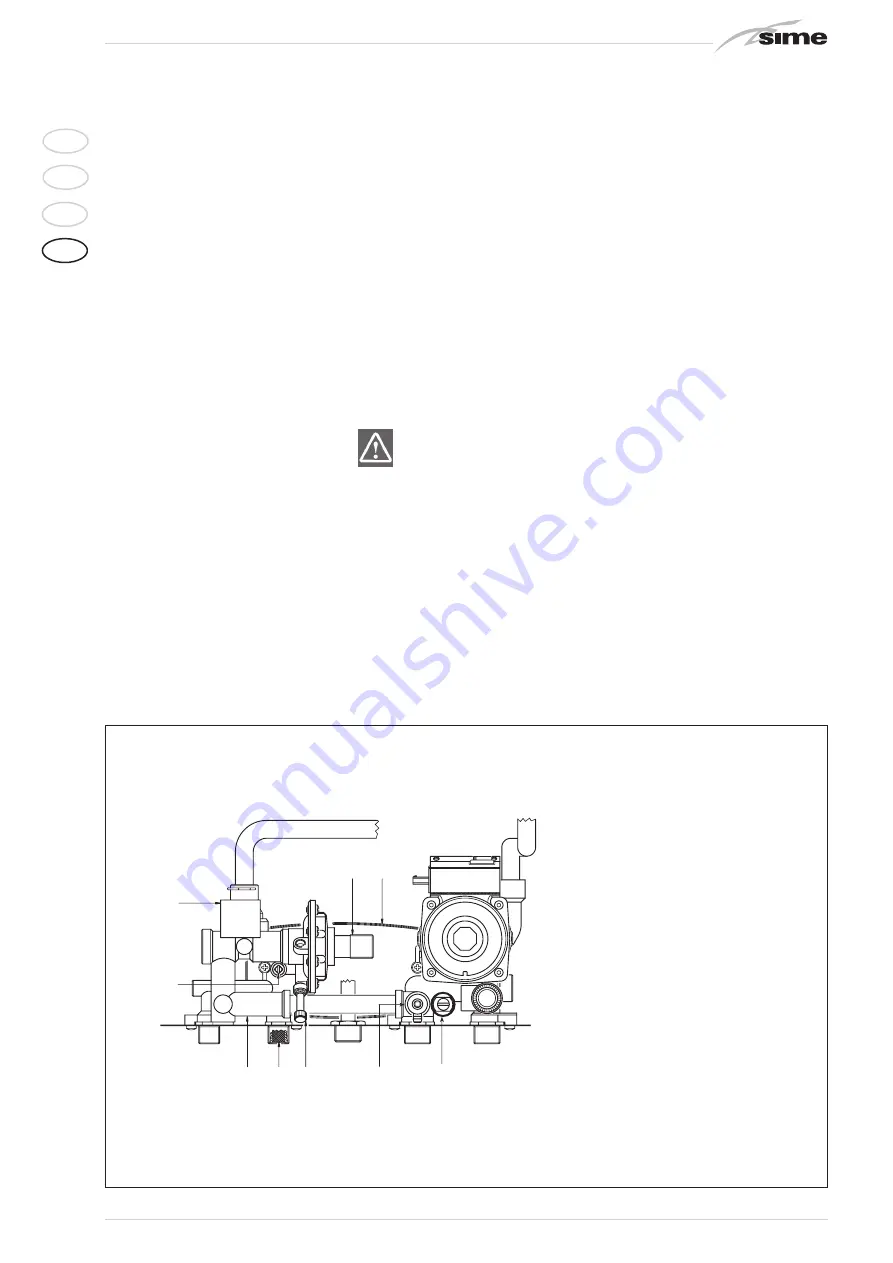
76
IT
ES
PT
GB
The boiler must be installed in a fixed loca-
tion and only by specialized and qualified
firms in compliance with all instructions
contained in this manual. Furthermore, the
installation must be in accordance with cur-
rent standards and regulations.
2.1
VENTILATION OF BOILER ROOM
The
m
odels
“25 - 30 Solar”
, with a herme-
tically sealed combustion chamber and air
supply circuit,may be installed in any room
in the home.
2.3
SUPPLEMENTARY ACCESSORIES
To simplify connections to the plant boiler, it
is possible to use any of the following sup-
plementary accessories that are supplied
with assembly instructions:
–Installation plate, code 8075416
–Kit with gas/inlet water curves and taps,
code 8075418
–Kit with taps, code 8091806
–Kit with replacement fittings for wall-
mounted boilers of other brands, code
8093900.
2.4
CONNECTING UP SYSTEM
To protect the heat system from damaging
corrosion, incrustation or deposits, before
installation it is extremely impor tant to
clean the system using suitable products
such as, for example, Sentinel X300 or
X400. Complete instructions are provided
with the products but, for further informa-
tion, you may directly contact SENTINEL
PERFORMANCE SOLUTIONS LTD.
For long-term protection agains corrosion
and deposits, the use of inhibitors such as
Sentinel X100 is recommended after clea-
ning the system. It is important to check
the concentration of the inhibitor af ter
each system modification and during main-
t enance f ollowing t he manuf actur er’s
instructions (specific tests are available at
your dealer). The safety valve drain must be
connected to a collection funnel to collect
any discharge during interventions. If the
heating system is on a higher floor than the
boiler, install the on/off taps supplied in kit
code 8091806 on the heating system deli-
very/return pipes.
WARNING: Failure to clean the heat
system or add an adequate inhibitor
invalidates the device’s warranty.
Gas connections must be made in accor-
dance with current standards and regula-
tions. When dimensioning gas pipes from
the meter to the module, both capacity
volume (consumption) in m
3
/h and gas
density must be taken into account.
The sections of the piping making up the
system must be such as to guarantee a
supply of gas sufficient to cover the maxi-
mum demand, limiting pressure loss
between the gas meter and any apparatus
being used to not greater than:
–1.0 mbar for family II gases (natural gas);
–2.0 mbar for family III gases (butane or
propane).
An adhesive data plate is sticked inside the
front panel; it contains all the technical data
identifying the boiler and the type of gas for
which the boiler is arranged.
2.4.1
Filter on the gas pipe
The gas valve is supplied ex factory with an
inlet filter, which, however, is not adequate
to entrap all the impurities in the gas or in
gas main pipes.
To prevent malfunctioning of the valve, or in
certain cases even to cut out the safety
device with which the valve is equipped,
install an adequate filter on the gas pipe.
2.5
SYSTEM FILLING
(fig. 5)
Filling of the boiler and the system is done by
the charge cock (2). The charge pressure,
with the system cold, must be between
1
and
1.2 bar
.
During system filling you are recommended to
keep the main switch turned OFF.
Filling must be done slowly so as to allow any
air bubbles to be bled off through the air val-
ves. Should the pressure have risen well above
the limit expected, discharge the over pressu-
re by opening the pressure-relief valve.
2.5.1
Emptying the system
(fig. 5)
Use the drain tap to empty the system (9).
Turn off the boiler before doing this.
2
INSTALLATION
Fig. 5
KEY
1 D.H.W. inlet/outlet manifold
2 Fill tap
3 D.H.W. filter
4 By-pass
5 Water rate adjuster
6 D.H.W. exchanger
7 Microswitches
8 Water flow switch
9 Boiler discharge
8
5
7 6
4
2
3
1
9
Summary of Contents for FORMAT.zip 25 Solar
Page 1: ...IT ES PT GB CERTIFICAZIONE DEL SISTEMA DI QUALITA AZIENDALE Format zip Solar ...
Page 2: ......
Page 95: ......