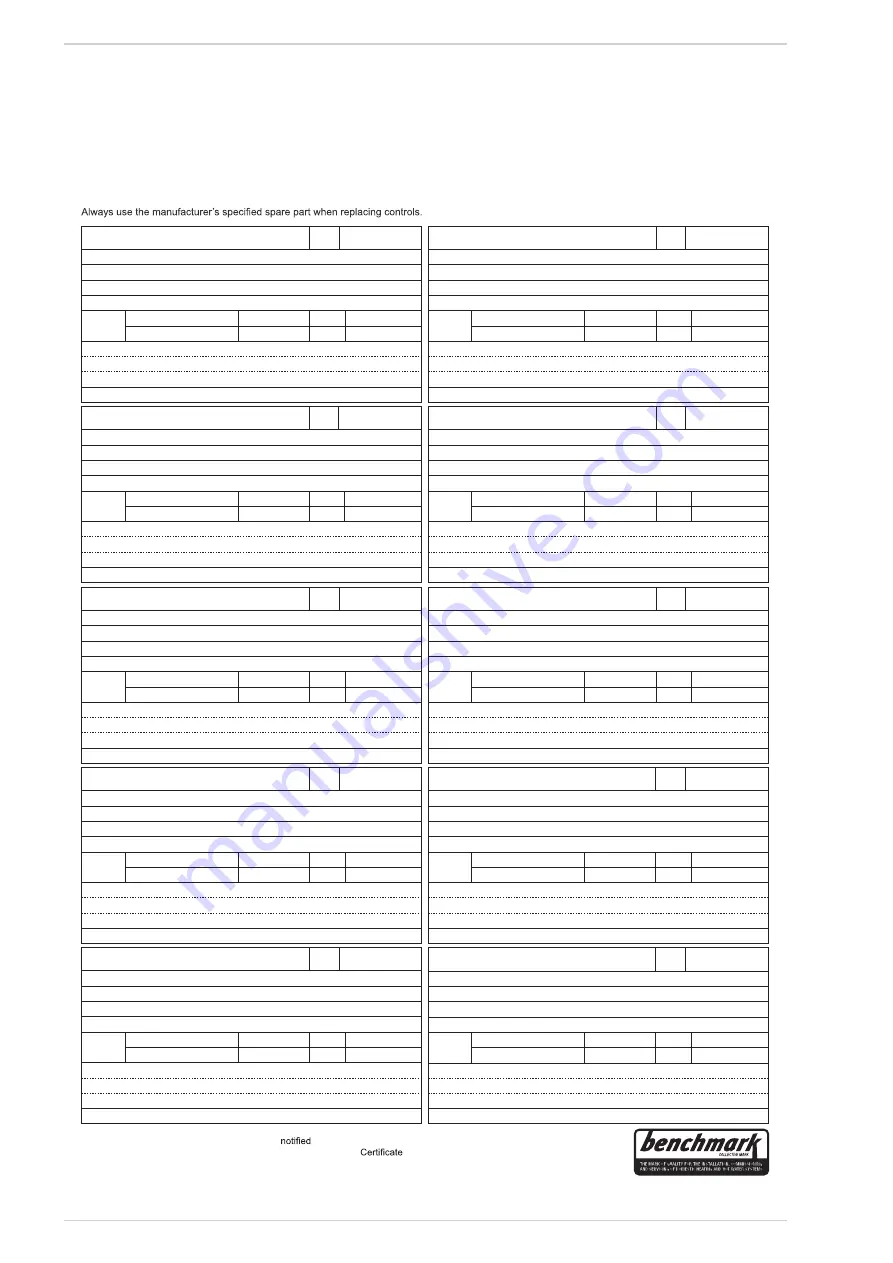
31
*All installations in England and Wales must be
to Local Authority Building Control (LABC) either directly or through a
Competent Persons Scheme. A Building Regulations Compliance
will then be issued to the customer.
© Heating and Hotwater Industry Council (HHIC)
www.centralheating.co.uk
It is recommended that your heating system is serviced regularly and that the appropriate Service Interval Record is completed.
Service Provider
Before completing the appropriate Service Record below, please ensure you have carried out the service as described in the manufacturer’s instructions.
SERVICE RECORD
SERVICE 01
Date:
Engineer name:
Company name:
Telephone No:
Gas safe register No:
Record:
At max. rate:
CO ppm
AND
CO² %
At min. rate:
(Where Possible)
CO ppm
AND
CO² %
Comments:
Signature
SERVICE 02
Date:
Engineer name:
Company name:
Telephone No:
Gas safe register No:
Record:
At max. rate:
CO ppm
AND
CO² %
At min. rate:
(Where Possible)
CO ppm
AND
CO² %
Comments:
Signature
SERVICE 03
Date:
Engineer name:
Company name:
Telephone No:
Gas safe register No:
Record:
At max. rate:
CO ppm
AND
CO² %
At min. rate:
(Where Possible)
CO ppm
AND
CO² %
Comments:
Signature
SERVICE 04
Date:
Engineer name:
Company name:
Telephone No:
Gas safe register No:
Record:
At max. rate:
CO ppm
AND
CO² %
At min. rate:
(Where Possible)
CO ppm
AND
CO² %
Comments:
Signature
SERVICE 05
Date:
Engineer name:
Company name:
Telephone No:
Gas safe register No:
Record:
At max. rate:
CO ppm
AND
CO² %
At min. rate:
(Where Possible)
CO ppm
AND
CO² %
Comments:
Signature
SERVICE 06
Date:
Engineer name:
Company name:
Telephone No:
Gas safe register No:
Record:
At max. rate:
CO ppm
AND
CO² %
At min. rate:
(Where Possible)
CO ppm
AND
CO² %
Comments:
Signature
SERVICE 07
Date:
Engineer name:
Company name:
Telephone No:
Gas safe register No:
Record:
At max. rate:
CO ppm
AND
CO² %
At min. rate:
(Where Possible)
CO ppm
AND
CO² %
Comments:
Signature
SERVICE 08
Date:
Engineer name:
Company name:
Telephone No:
Gas safe register No:
Record:
At max. rate:
CO ppm
AND
CO² %
At min. rate:
(Where Possible)
CO ppm
AND
CO² %
Comments:
Signature
SERVICE 09
Date:
Engineer name:
Company name:
Telephone No:
Gas safe register No:
Record:
At max. rate:
CO ppm
AND
CO² %
At min. rate:
(Where Possible)
CO ppm
AND
CO² %
Comments:
Signature
SERVICE 10
Date:
Engineer name:
Company name:
Telephone No:
Gas safe register No:
Record:
At max. rate:
CO ppm
AND
CO² %
At min. rate:
(Where Possible)
CO ppm
AND
CO² %
Comments:
Signature