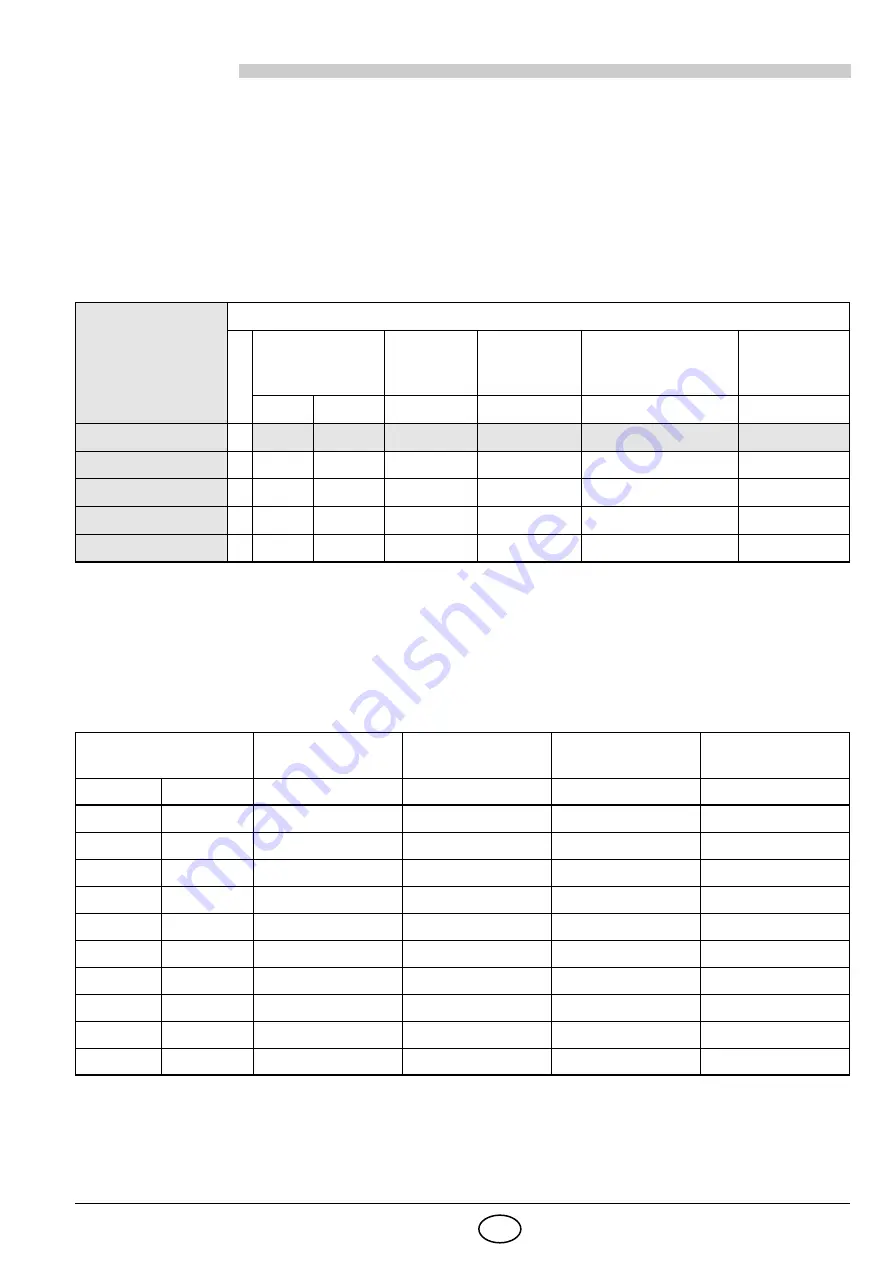
2684
6
GB
4.
WORKING
4.1 COMBUSTION ADJUSTMENT
In conformity with Efficiency Directive 92/42/EEC the application of the burner on the boiler, adjustment and
testing must be carried out observing the instruction manual of the boiler, including verification of the CO and
CO
2
concentration in the flue gases, their temperatures and the average temperature of the water in the boiler.
To suit the required appliance output, choose the proper nozzle and adjust the pump pressure, the setting of
the combustion head, and the air damper opening in accordance with the following table.
■
ADJUSTMENTS FOR SIME BOILERS
The values shown in the table are measured on a SIME boiler (as per EN 267).
They refer to 12.5% CO2 at sea level and with light oil and room temperature of 20 °C.
▲
Burner adjustments carried out in factory.
In case of matching with a boiler different from the “Rondò-Estelle 6” model, for the adjustments fol-
low what indicated in the table.
■
APPROXIMATE ADJUSTMENTS FOR INSTALLATION ON OTHER BOILERS
The values shown in the table are measured on a CEN boiler (as per EN 267).
They rfer to 12.5% CO2 at sea level and with light oil and room temperature of 20 °C.
4.2 NOZZLES RECOMMENDED:
Monarch type R
;
Delavan type W - B
Steinen type S - Q ;
Danfoss type S - B
For 2.00 – 250 GPH nozzle it is advisable to use, if possible,
full cones.
BOILER
BURNER - Code 8099050 - Model MACK 6
Nozzle
Pump
pressure
Burner
output
Combustion
head adjustment
Air damper
adjustment
GPH
Angle
bar
kg/h
±
4%
Set-point
Set-point
Rondò-Estelle 6
▲
1.10
60° W
12
4.4
2.0
3.0
Rondò-Estelle 7
1.25
60° W
13
5.2
2.5
3.5
1R 6
1.50
60° B
12
6.0
3.0
3.5
1R 7
1.75
60° B
12
7.0
3.5
4.0
1R 8
1.75
60° B
14
7.6
4.0
5.0
Nozzle
Pump
pressure
Burner
output
Combustion
head adjustment
Air damper
adjustment
GPH
Angle
bar
kg/h ± 4%
Set-point
Set-point
0.85
60°
12
3.4
1
2.1
1.00
60°
12
4.0
1.5
3.2
1.10
60°
12
4.4
2
3
1.25
60°
12
5.0
2
3.4
1.50
60°
12
6.0
3
3.4
1.75
60°
12
7.0
4
4.5
2.00
60°
12
8.0
5
5.2
2.25
60°
12
9.0
6
5.5
2.25
60°
14
9.8
6
6
2.50
60°
12
10.0
6
8