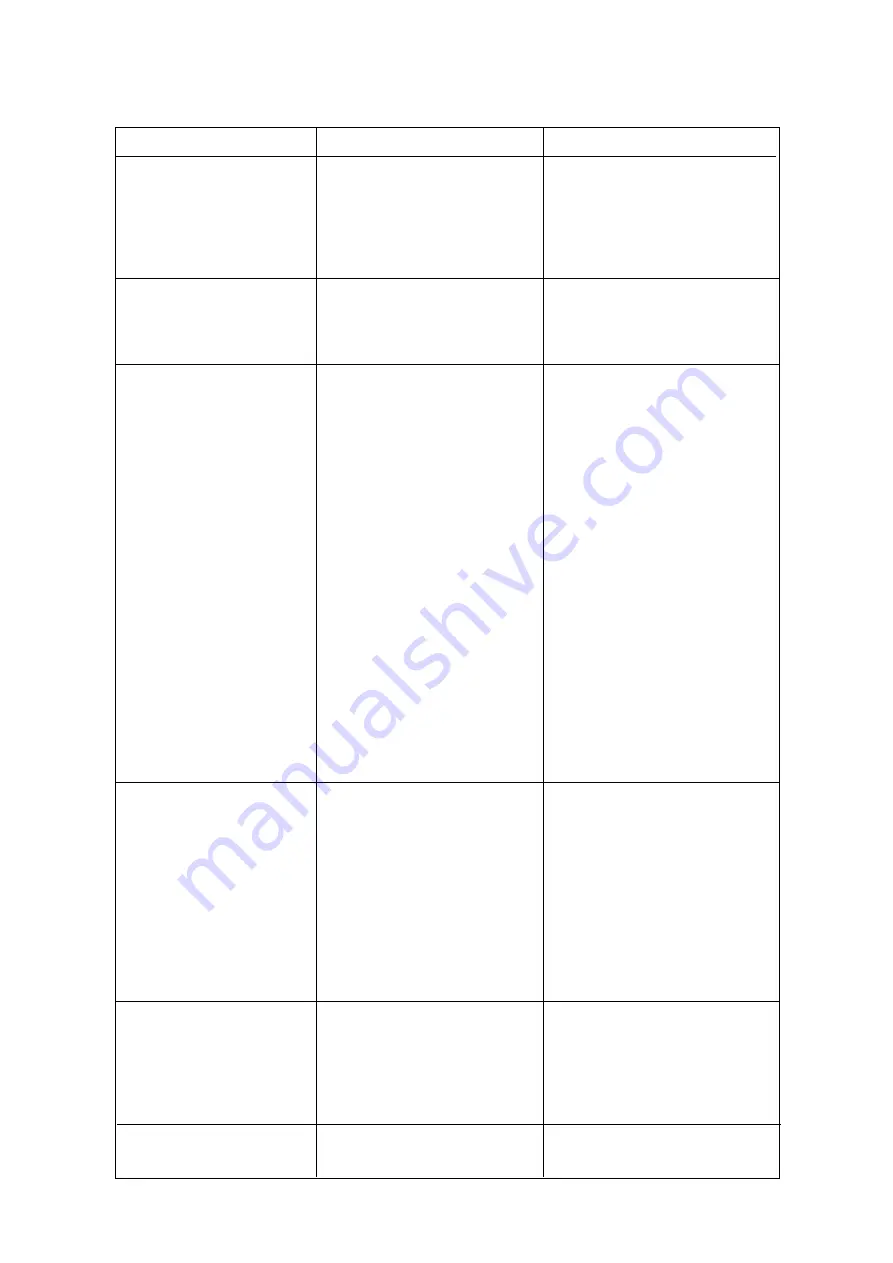
Irregular cubes
Some jets plugged
Remove jet cover and clean
size & some cloudy
Shortage of water
See shortage of water
Unit not level
Level as required
Cubes too large
Freezing cycle too long
Adjust evap. thermostat
Inoperative evaporator thermostat
Replace thermostat
Decreased ice capacity
Inefficient compressor
Replace
Leaky water valve
Repair or replace
Non-condensable gas in system
Purge the system
Poor air circulation or excessive
Relocate the unit or provide for
hot location
more ventilation
(
Overcharge of refrigerant
Correct the charge. Purge off slowly
Capillary tube partially restricted
Blow charge, add new gas & drier,
after evacuating system with
vacuu pump
Hot gas solenoid valve leaking
Replace valve
Undercharge of refrigerant
Charge to data plate indication
Discharge head pressure too high
See incorrect discharge pressure
Poor harvest
Restriction in incoming water line
Check water valve strainer and flow
control. If necessary enlarge the
flow control orifice
Water inlet valve not opening
Valve coil with open winding
Replace valve
Hot gas valve orifice restricted
Replace hot gas valve assy
Discharge head pressure too low
See incorrect discharge pressure
Incorrect discharge pressure
Inoperative fan pressure control
Replace pressostat
Inoperative fan motor
Replace
Water regulating valve misadjusted Adjust its setting stem
Excessive water in unit base
Water tubing leaking
Check. Tighten or replace
SERVICE DIAGNOSIS
SYMPTOM
POSSIBLE CAUSE
SUGGESTED CORRECTION
Page 11
Summary of Contents for SDE-34-L
Page 5: ...SDE 30 ...
Page 6: ...SDE 34 ...
Page 7: ...SDE 40 ...
Page 8: ...SDE 50 ...
Page 9: ...SDE 64 ...
Page 10: ...SDE 84 ...
Page 11: ...SDE 170 ...
Page 12: ...SDE 220 ...