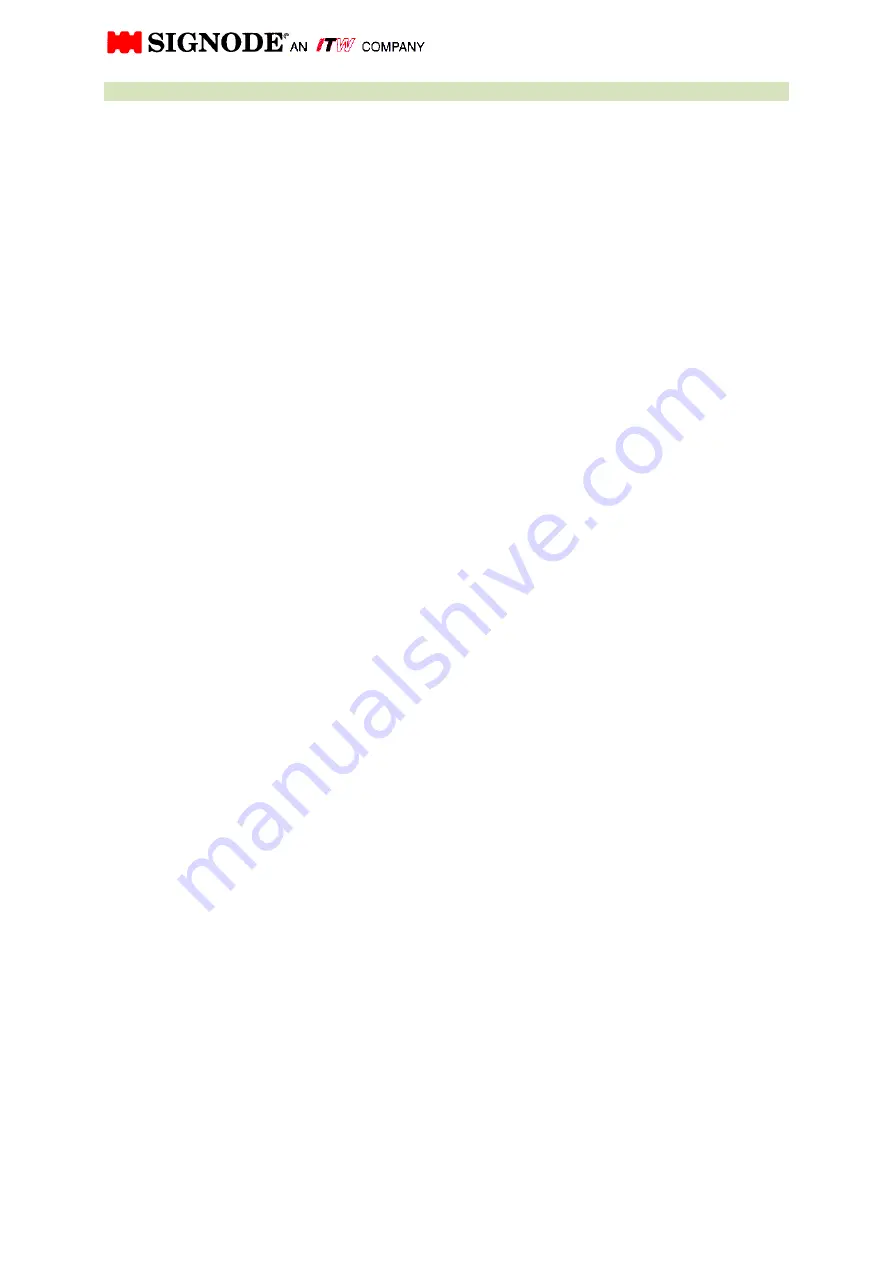
13
5. PREVENTIVE MAINTENANCE
Daily:
- Clean feed wheel and chain by using an air pistol.
- Shutter must be open to clean sealing mechanism, remove remaining weld scrap.
- Check whether strap limit switch works free of trouble and the strap tail is clamped.
(see section 7.2.)
Weekly:
- Check strap transportation, disconnect chain, check bearing and chain links, check feed
wheel ring if necessary exchange.
- Check strap guide wedge.
Clean switch actuator with air pistol. Check strap gates for easy movement.
- Check shutter for easy movement and apply oil to guide ways of rails if necessary.
Monthly:
- Grease the guide shaft
(see drwg. 464631, pos. 106, page 33).
- Remove and clean gripper complete, vibrator support and loop grip and apply with creep
oil (light oil).
- Apply grease to the vibrator guide way – the guide way will be lubricated with a high
temperature grease, (see drwg. 464655, pos. 20, 25, page 39).
- Needle bearing eccentric arm - eccentric shaft will be lubricated with a high temperature
grease, (see drwg. 464655 pos. 21, page 39)
- Grease bolt for eccentric arm (connection between vibrator and eccentric lever,
(see drwg. 464655, pos. 27).
-
Grease the cam follower roller and check the cam follower roller for proper
rotation. Apply grease on both sides of lever - cam follower roller will be lubricated
with MOLYKOTE LONGTERM 2 PLUS, (see drwg. 464631, pos. 63, 64, 65, page 33).
- Check wear parts according to the enclosed recommended spare parts list and replace
parts if necessary.
Annually:
-
Check all electrical connections and retighten any which appear to be loose.
-
Check the weld motor brushes and inspect the motor armature for wear.
-
Grease the needle bearing pos. 18 of strap drive (see drwg. 464626 page 47)
-
Check the Belleville washer inside the gripper, loop gripper and vibrator support and replace
washers if necessary (see page 39 pos 75, Page 39a and b).
ATTENTION:
After a period of time or after exchange of wear parts check welded joints of strap samples.
Readjustments might be necessary, e.g. pressure of plungers or changes of welding time
(see section "Head Adjustments" point 7.1 and 7.4)
Summary of Contents for AK200HDX-19
Page 13: ...SERVICE AND MAINTENANCE MANUAL FOR STRAPPING HEAD MODEL AK200 HDX 19 25 32 mm ...
Page 18: ...4 Strapping head drive allegory ...
Page 47: ...33 ...
Page 54: ...39 b ...
Page 65: ...50 50 Brake 100 14 Strap center Insert these screws with loctite ...
Page 67: ...52 Intermediate shaft 464291 ...
Page 77: ...62 Insert guide wedge 464636 ...
Page 80: ...65 ...
Page 81: ...66 ...