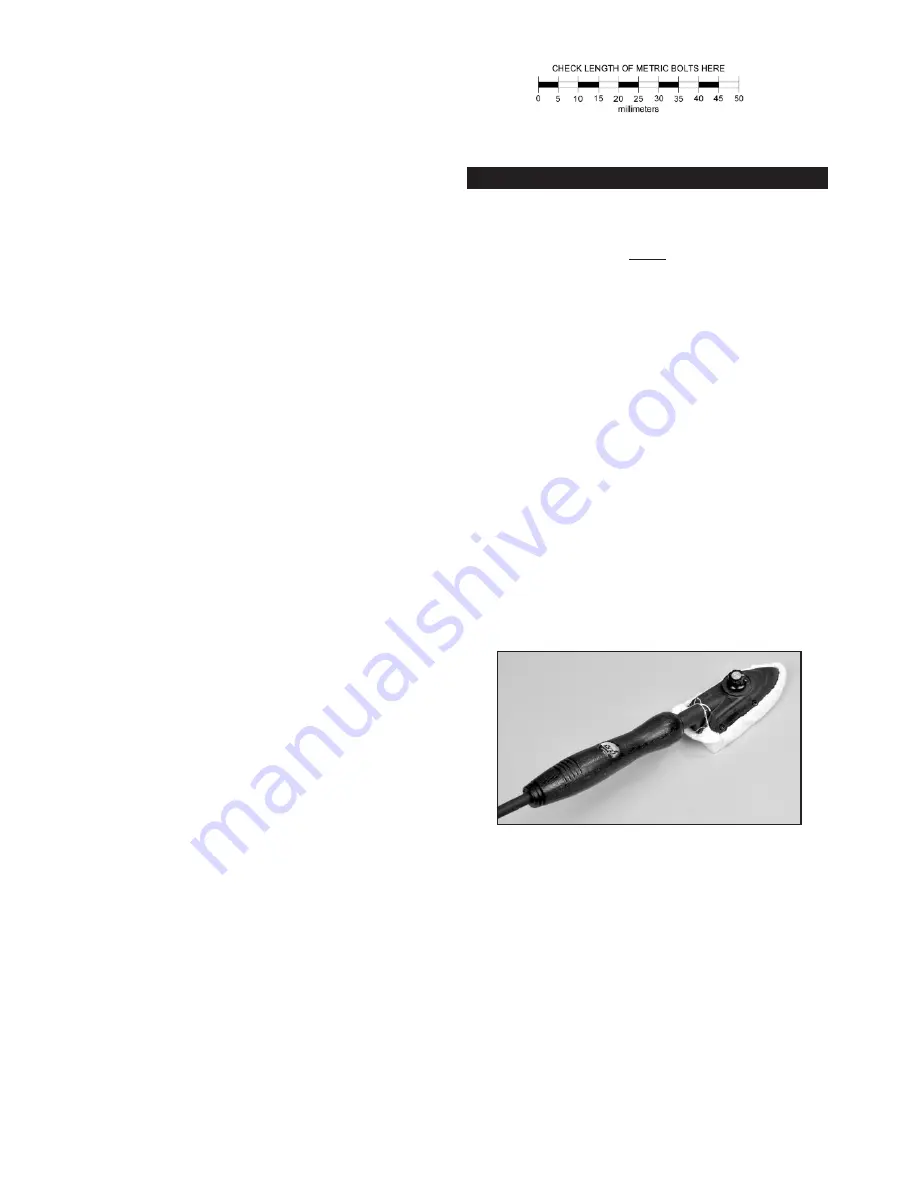
❑
(2) 3-1/2” dia. Main Wheels
❑
(2) 4mm dia. x 62mm Axles
❑
(2) 7.5mm Hex Nuts; for axles
❑
(4) 4mm ID Wheels Collars; for axles
❑
(1) Right Fiberglass Wheel Pant; painted white
❑
(1) Left Fiberglass Wheel Pant; painted white
Tailwheel
❑
(1) Tailwheel Assembly, including Wheel, formed Wire, Nylon
Bearing, and Wheel Collars(2)
❑
(2) M3 x 12mm Sheet Metal Screws
Electric Motor Mount
❑
(1) Plywood Electric Motor Box Assembly; for electric motors
❑
(1) Balsa Triangle Stock; for motor mount reinforcement
❑
(2) Velcro® Straps
❑
(4) M4 x 20mm Socket-Head Mounting Bolts; for electric
motor mount to firewall
❑
(4) M4 Flat Washers; for electric motor mount to firewall
❑
(4) M4 x 16mm Socket-Head Mounting Bolts; for electric
motor to mounts
❑
(4) M4 Split-Ring Lock Washers; for electric motor to mounts
❑
(4) M4 Blind Nuts; for electric motor to mounts
Engine Mounts for Glow Engine
❑
(2) Nylon Engine Mounts; for glow engines
❑
(4) M4 x 20mm Mounting Bolts, for engine mount to firewall
❑
(4) M4 Flat Metal Washers, for engine mount to firewall
Fuel Tank for Glow Engine
❑
(1) Fuel Tank
❑
(1) Rubber Stopper Assembly
❑
(1) Fuel Pick-Up Weight, Metal
❑
(1) Fuel Line Tubing, for inside tank
❑
(1) laser-cut plywood Fuel Tank Support
Control Horns
❑
(4) Nylon Control Horns; for ail(2), ele(1), rud(1)
❑
(2) Nylon Control Horn Retaining Plates; for ele(1), rud(1)
❑
(12) M2 x 14 mm Screws; for control horns
Pushrods
❑
(2) 39-1/2" long Wire Pushrods, threaded on one end,
including M2 Hex Nuts(2); for elev. & rud.
❑
(2) 6-3/4" long Wire Pushrods, threaded on one end,
including M2 Hex Nuts(2); for ail.
❑
(1) 17-3/4" long Wire Pushrod, , threaded on one end,
including M2 Hex Nut; for throttle
❑
(1) 13-3/4" long Nylon Pushrod Tube, for throttle
Miscellaneous
❑
(1) 19mm OD x 495 mm Aluminum Tube Main Wing Joiner
❑
(1) Molded Clear Plastic Side Window, Right Front
❑
(1) Molded Clear Plastic Side Window, Left Front
❑
(2) Molded Clear Plastic Side Windows, Rear
❑
(2) M6.5 x 30 mm Nylon Wing Bolts with slotted head
❑
(4) Metal Clevis; for ail(2), ele(1), rud(1), throttle)1)
❑
(5) small pieces of Fuel Tubing; for metal clevis keepers
❑
(4) Pushrod Snap Keepers; for ail(2), ele(1), rud(1)
❑
(4) M3 x 10mm Sheet Metal Screws, for cowling
❑
(4) M3 x 12mm Socket-Head Bolts, for wheel pants
❑
(3) M4 x 20mm Socket-Head Bolts, for main landing gear
❑
(3) M4 Split-Ring Lock Metal Washers, for main landing gear
❑
(1) Metal Pushrod Keeper with Set Screw and Hex Nuts,
for throttle servo connector
❑
(2) 240mm long Plastic Cinch Straps
❑
(1) Small Balsa Block; for fuel tank stop
Your KADET SENIOR ARF is covered with Oracover
®, a premium
quality covering made in Germany, and sold in the U.S. by Hanger-
9 as Ultracote
®
.
Colors
Oracover® #10 White (Ultracote® #HANU870)
and
Oracover® #29 Transparent Red (Ultracote® #HANU950)
or
Oracover® #59 Transparent Blue (Ultracote® #HANU954)
If sometime in the future you need replacement covering or
matching paint for repairs, they are available from your local hobby
dealer or online from Hanger-9.
How To Tighten Loose Covering
After you open your KADET SENIOR and take all the covered
parts out of their plastic bags, the covering may begin to wrinkle.
This is not unusual and is no cause for alarm.
Your airplane was built and covered in a part of the world which
has relatively high humidity and therefore, the wood was likely car-
rying a fair amount of moisture. When exposed to drier air, the
wood typically loses this moisture, dimensionally "shrinking" in the
process. In turn, this may cause some wrinkles. However, wrin-
kles are easy to remove by just using a hobby type heat iron. Cau-
tion: Trying to remove the wrinkles by hastily going over them with
a heat gun can lead to more problems. You should take your time
to carefully go over the entire model with a covering iron, as we
will describe.
We suggest using a model airplane covering iron for this process.
Cover the iron's shoe with a thin cotton cloth, such as an old t-
shirt, to prevent scratching the covering as you work.
After covering your iron, the next step is to set the iron to the cor-
rect temperature. This is critical for achieving a good result! The
iron should be set to about
220
O
F - 250
O
F (104
O
C - 121
O
C)
as
measured on the bottom of the iron using a thermometer.
If you do not have a thermometer, you can find the correct tem-
perature by trial and error. Set your iron to a medium setting.
Glide the iron over some of the covering that is over over solid
wood, such as the sheeted wing center section. Observe the cov-
ering to see if any bubbles appear. If bubbles appear, the covering
is getting too hot! Turn down the temperature of the iron.
If no bubbles appear, turn up the heat slightly and repeat the test.
Keep adjusting until you “zero in” on the correct temperature. Find
the temperature that will get the covering to stick down without
forming bubbles or causing the seams to pull away.
4
COVERING MATERIAL